Bundle Multi (2-in-1) - SAP PP
Learn about planning and implementation of business manufacturing & production processes in a company.Preview Bundle Multi (2-in-1) - SAP PP course
View Course Curriculum Price Match Guarantee Full Lifetime Access Access on any Device Technical Support Secure Checkout   Course Completion Certificate80% Started a new career BUY THIS COURSE (
USD 31 USD 69 )-
90% Got a pay increase and promotion
Students also bought -
-
- Bundle Course - Full Stack Web Development
- 200 Hours
- USD 31
- 3788 Learners
-
- Bundle Course - SAP Logistics (PM - PP - MM - QM - WM - SD - S4HANA Logistics)
- 200 Hours
- USD 31
- 1692 Learners
-
- Career Path - IT Consultant
- 200 Hours
- USD 45
- 5851 Learners
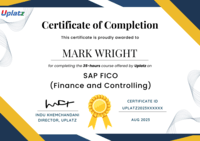
This is the Bundle Multi (2 in1) – SAP PP Course by Uplatz of self-paced training (pre-recorded videos) on the following modules:
1).SAP PP
2).SAP PP course
SAP Production Planning is a core SAP module that provides a devoted system for planning and implementation of business manufacturing & production processes in an company.
SAP PP contains master data, configurations and transaction data for completion of plan to production process. It helps in detailed planning for achieving the production goals and helps in recording, tracking of all production & manufacturing process. SAP PP handles all business processes related to production of a company. SAP PP includes all activities like Material Requirement Planning (MRP), Bill of Materials (BOM), Capacity Planning (CP) and Supply Chain Planning (SCP).
Since factories, small manufacturing units, foundries, etc. have manufacturing plants, SAP PP module forms a vital part of their infrastructure as it provides the capabilities for efficient management of production facilities and processes.SAP PP is completely integrated with other modules of SAP such as SAP MM, QM, PM, FICO. SAP PP sub-modules differ as per industry type for e.g. discrete production, repetitive production, or production industries.
SAP PP module manages the key steps in executing a production order viz. Convert Planned Order to Production Order, Issue the Production Order, Issue Goods for Production Order, Production Order Confirmation, Good Receipts w.r.t Production Order.
In Bundle Multi (2 in 1) SAP PP course by Uplatz you will have a comprehensive SAP PP training in the form of self-paced videos. The SAP PP course will help you to: 1) Understand Business from Production & Planning department perspective, 2) Map customer business processes in SAP, 3) Integrate PP module with other functional areas like Materials, Finance, Costing etc., 4) Design/enhance operational and analytical reports for customer, 5) Train users for using SAP system
This SAP PP Bundle Multi training by Uplatz provides in-depth knowledge of all functions within PP module with practical examples and live server configurations.
At a high-level these are some of the topics covered under this SAP PP course: Production Planning Master Data, Master Planning, Material Requirement Planning, Production Orders, Discrete Manufacturing, Repetitive Manufacturing, Integration points of Production Planning with other modules, Reporting & Tools.
Course/Topic 1 - SAP PP - all lectures
-
In this first video lecture, you will get an overview on what exactly is ERP, the goals and objectives of ERP, SAP and its history, different technical and functional modules of SAP, use of SAP PP module in enterprises and what is its purpose and necessity.
-
In this video, you will learn about Bill of Material (BOM) in SAP PP module, what is a single-level and multi-level BOM and how users can create these in the system. It will be further proceeded with the Consumption Based Planning (CBP) and its different features like Reorder Point Planning, Forecast Based Planning and Time Based Planning.
-
In this lecture, you will learn the steps to perform the Automatic ROP like creating a Material Master, maintaining the stock for the material by creating PO and GR, monitoring the stock overview, creating, releasing and confirming PO, technical completion of PO and viewing actual or target cost comparison.
-
In this video, you will understand how to calculate the Production Order and the work in process for individual and multiple orders. You will also learn the Variance Calculation for PO which is KKS2 and the Actual Settlement for Production Order along with how to close a Production Order. Lastly, it will be concluded with the Plant independent requirements and how we can manually create this in the planning table.
-
In this lecture, you will learn what is Sales and Operation Planning (SOP) and what is its need in the SAP Production Planning module. Also, you will get a pictorial representation of the complete SOP Process Flow from creating Sales Plan to Transfer of Planning Values to Demand Management with a live demonstration on working with the different work flow process for Sales and Operation Planning.
-
In this video, you will get to learn what is a Repetitive Manufacturing Process and what is the need of it in SAP PP module. Also, you will get to understand what is Repetitive Manufacturing Profile, what are the steps involved in creating repetitive Manufacturing Profile, what is Backflushing and Product Cost Collector.
-
In this final lecture, you will understand what is an Availability Check and TOR in SAP Production Planning. You will also understand the configuration settings for these two and what are the steps involved in performing the Availability Check. Further, it will be proceeded with an overview on CO11, CO15 and Milestone Confirmation.
Course/Topic 2 - SAP PP course - all lectures
-
Lecture 1 - SAP PP Introduction
-
Lecture 2 - Master Data in PP
-
Lecture 3 - Configuration Settings for Master Data - part 1
-
Lecture 4 - Configuration Settings for Master Data - part 2
-
Lecture 5 - Material Master - part 1
-
Lecture 6 - Material Master - part 2
-
Lecture 7 - BOM in PP
-
Lecture 8 - Work Center in PP
-
Lecture 9 - PRT and Routing
-
Lecture 10 - Production Version and Different Types of Scrap
-
Lecture 11 - Scraps - Assembly and Component and Operation
-
Lecture 12 - MRP Planning and Consumption-based Planning
-
Lecture 13 - Forecast-based Planning and Time-phased Planning
-
Lecture 14 - Automatic Reorder Point (ROP) Planning and Manual ROP Planning
-
Lecture 15 - Internal Procurement Process - part 1
-
Lecture 16 - Internal Procurement Process - part 2
-
Lecture 17 - Internal Procurement Process - part 3
-
Lecture 18 - Internal Procurement Process - part 4
-
Lecture 19 - Batch Management in PP
-
Lecture 20 - Serial Number Management in PP
-
Lecture 21 - Sales and Operations Planning - SOP
-
Lecture 22 - Strategy Group for MTS and MTO Process
-
Lecture 23 - Strategy Group 25 - MTO Configurable Material or Variant Configuration
-
Lecture 24 - SAP PP integration with SAP QM
-
Lecture 25 - Availability Check in MRP and Introduction to MPS
-
Lecture 26 - Master Production Schedule (MPS)
-
Lecture 27 - Repetitive Manufacturing Process
-
Lecture 28 - SAP PP integration with SAP PI
-
Lecture 29 - SAP PP integration with SAP FI
-
Lecture 30 - Creating Order Types and Production Scheduling Profile
In this course you will learn about;
a).Production Planning Master Data
b).Master Planning
c).Material Requirement Planning
d).Production Orders
e).Discrete Manufacturing
f).Repetitive Manufacturing
g).Integration points of Production Planning with other modules
h).Reporting & Tools.
This course provides a comprehensive introduction to SAP Production Planning (PP), focusing on the key concepts, processes, and configuration necessary for effective production planning and control within an SAP environment.
Part 1: Introduction to SAP PP
Week 1: Overview of SAP PP
a) Introduction to Production Planning concepts and objectives
b) Understanding the integration of SAP PP with other modules (MM, SD, QM)
c) Overview of the course structure and learning outcomes
Week 2: Organizational Structures in PP
a).Configuring organizational units: Plant, Storage Location, and Work Center
b).Understanding production versions and routing
c).Hands-on exercise: Setting up organizational structures in SAP PP
Week 3: Master Data in SAP PP
a).Overview of master data: Material Master, Bill of Materials (BOM), and Routing
b).Creating and managing material master data
c).Configuring BOMs and routings for production processes
d).Hands-on exercise: Building BOMs and routings in SAP
Week 4: Demand Management
a) Understanding demand management concepts and strategies
b) Configuring forecast and planning methods
c)Overview of planning levels: Independent and Dependent Requirements
d) Hands-on exercise: Setting up demand management in SAP PP
Part 2: Production Planning Processes
Week 5: Material Requirements Planning (MRP)
a).Overview of MRP concepts and processes
b).Configuring MRP parameters and settings
c).Understanding MRP runs and results analysis
d).Hands-on exercise: Executing an MRP run and analyzing results
Week 6: Production Order Management
a) Introduction to production orders and their lifecycle
b) Creating and managing production orders
c) Understanding order types and confirmations
d) Hands-on exercise: Creating and processing production orders
Week 7: Capacity Planning
a) Overview of capacity planning concepts
b) Configuring work centers and capacity evaluation
c) Understanding load management and capacity leveling
d) Hands-on exercise: Setting up and evaluating capacity planning
Part 3: Advanced Topics and Capstone Project
Week 8: Shop Floor Control
a) Introduction to shop floor control processes
b) Managing production execution and tracking progress
c) Understanding production reporting and efficiency measurement
d) Hands-on exercise: Monitoring production orders on the shop floor
Week 9: Integration with Other Modules
a) Overview of integration points between SAP PP and other modules (MM, SD, QM)
b) Understanding how production planning affects procurement and sales
c) Case studies on integrated production planning scenarios
d) Hands-on exercise: Exploring integration functionalities
Week 10: Capstone Project
a) Overview of capstone project objectives
b)Participants will design and implement a comprehensive SAP PP solution
c) Presentation of projects and peer reviews
d) Discussion on challenges faced and lessons learned
Recommended Resources:
Textbooks:
1) "Production Planning and Control with SAP ERP" by J. L. D. W. H. H. Rosy and others
2) "SAP PP: Configuration and Implementation" by Karl-Heinz L. and others
Online Resources:
1) SAP Learning Hub for online training modules
2) SAP Community for discussions and knowledge sharing
Tools:
1) SAP ERP system for hands-on practice
Assessment:
1) Weekly quizzes and assignments
2) Mid-term project focused on specific PP functionalities
3) Final capstone project showcasing a complete SAP PP solution
The SAP PP Certification ensures you know planning, production and measurement techniques needed to stand out from the competition.
SAP Production Planning is a module that handles all business processes related to production of a company. SAP PP includes all activities like Material Requirement Planning(MRP), Bill of Materials(BOM), Capacity Planning(CP) and Supply Chain Planning(SCP).
The SAP PP Certification Exam verifies that the candidate possesses fundamental knowledge and proven skills in the area of SAP Production Planning and Manufacturing
SAP Certification is an online and onsite program that enables your organization to keep pace with the latest SAP technology advances. With this program, certification courses and exams can be accessed on-demand for maximum flexibility and convenience. Exams can also be taken onsite.
Uplatz online training guarantees the participants to successfully go through the SAP PP certification provided by Uplatz. Uplatz provides appropriate teaching and expertise training to equip the participants for implementing the learnt concepts in an organization.
Course Completion Certificate will be awarded by Uplatz upon successful completion of the SAP PP online course.
The SAP PP draws an average salary of $102,080 per year depending on their knowledge and hands-on experience. The SAP PP Admin job roles are in high demand and make a rewarding career.
SAP PP module certification can help candidates aspire for the lucrative job opportunities as senior consultants, SAP Production Planning Consultants, assistant managers and senior level managers.
SAP constantly strives to perform research on market trends and business requirements. Based on the current demand, SAP comes up with updated and advanced products with newer features. It is always in trend and thus one of the strong reasons for a fresher to choose a career in SAP.
Note that salaries are generally higher at large companies rather than small ones. Your salary will also differ based on the market you work in.
a).SAP Business Analyst.
b).SAP Consultant.
c).SAP Developer.
d).SAP FICO Consultant.
e).SAP Functional Consultant.
f).SAP Manager.
g).SAP MM Consultant.
h).SAP Project Manager.
Q1)xplain what is SAP PP?
Ans-SAP PP process is related to production planning of a company and it encompasses all activities like MRP (Material Requirement Planning), BOM (Bills Of Material), Routing, Capacity planning, etc. but mainly it contains two segments
a) Material Planning: Material requirements planning, long term planning,
b)Execution Planning: Creation of production order, workflow, conformations, technical completion and good movement
Q2) Mention what are the production process in SAP?
Ans-There are three types of production process in SAP
a) Discrete Manufacturing
b) Repetitive Manufacturing
c) Production- Process Industries
Q3) List out the activities carried out in Production Planning?
Ans-Activities involved in Production Planning includes
a) Processing material master
b) Creation of Bill of Material
c) Displaying work center and routing
d) Maintaining planning calendar
e) Maintaining production lot
f) Maintaining quota file
g) Defining range of coverage profile and profile for safety time
h) Defining MRP views
Q4) Explain what is Routing in SAP PP?
Ans-Routing in SAP PP is referred to a list of activities which are required to produce any material. For example, when you do cost estimation for the material, the system triggers the relevant routing and activity rates for all those described in routing. Which will helpful to calculate the processing cost in product costing.
Q5) What are the steps of Production Execution Process?
Ans-Production Execution steps include
a) Converting planned order to production order
b) Releasing the production order
c) Goods issue for production order
d) Confirmation of production order
e) Goods receipt against production order
Q6)What are the reports generated in product cost controlling information system?
Ans-Product Cost Controlling information system generates information for following areas
a) Product cost planning
b) Cost object controlling with the subcomponents
c) Product cost by period
d) Product cost by order
e) Product cost by sales order
f) Costs for intangible goods and services
g) Actual costing / Material Ledger
Q7) Explain what is “work center” in SAP PP and what is the use of Data in Work Centers?
Ans-“Work Centers” are business objects in SAP-PP that is used in task list operations ( routings, maintenance task lists, inspection plans) and work orders.Data in work center is used for
a)Scheduling: Formulas and operating time are entered, so that the duration of an operation can be calculated
b)Costing: Formulas are entered so that the costs of an operation can be calculated
c)Capacity Planning: The available capacity and formulas for capacity requirements is entered
d)Simplifying operation maintenance: Various default values can be included in the work center
Q8) What is the use of MRP PP evaluations?
Ans-This role contains a function for evaluating the MRP result. This function can be used to find information about the availability of material and to identify any material shortage situation.
Q9) Mention what is the purpose of using Capacity Planning?
Ans-Capacity Planning supports planning in all phases
a) Long term rough cut planning
b) Medium term planning
c) Short term planning
It can be integrated with various SAP applications like SAP-SD, PP, PP-SOP, PP-LTP, PP-SFC, etc.
Q10)Explain how can you create production order without routing and BOM?
Ans-Without BOM and routing you can create a production order by changing the config in OPL8 ( order type dependent parameters) as routing optional. When we try to create an order using C001 it may ask for a sales order.
Q11)Explain what happens to planned after it has been converted into production order?
Ans-When planned order is converted to the production order, the planned order are offset by production order. The planned order reference can be seen in the production order.
Q12)Mention what is the difference between stock transport order and stock transfer order?
Ans-
a).stock transfer order: It is referred to the transfer of stock for the usage in the same company
b).Stock transport order: It is referred to the change of title of stock in the name of the buyer
Q13) Explain what is PRT (Production Resource Tools) in SAP PP?
Ans-PRT (Production Resource Tools) are moveable operating objects used to perform repeated activities in plant or production maintenance, for example, documents such as drawings or programs for which document management functions are used. Various other PRT components include
a) Engineering drawings
b) Jigs
c) Fixtures
d) Measurement Instruments
Q14) Explain how to create PRT master records?
Ans-To create PRT master records you have to follow the following steps
1.Choose logistics/Accounting -> Project System -> Basic data -> Master data -> Production resources and tools -> Create
2.The initial screen for creating a PRT appears
3.Enter a number for the PRT and choose continue
4.The basic data screen appears
5.Maintain the basic data
6.Choose Goto -> Defaults and enter the default values
7.Save the PRT
Q15)ention what is the t-code for changing production order and to display production order?
a).code to change the production order = C002
b).T-code to display the production order = C003