Bundle Course - SAP SCM (Supply Chain Management)
You will learn practical implementation, configuration, and management of the SAP SCM modules. Carve your career path as an SAP Functional Consultant.Preview Bundle Course - SAP SCM (Supply Chain Management) course
Price Match Guarantee Full Lifetime Access Access on any Device Technical Support Secure Checkout   Course Completion Certificate86% Started a new career BUY THIS COURSE (
GBP 22 GBP 49 )-
86% Got a pay increase and promotion
Students also bought -
-
- SAP QM (Quality Management)
- 20 Hours
- GBP 12
- 250 Learners
-
- SAP PM (basic to advanced)
- 18 Hours
- GBP 12
- 402 Learners
-
- Career Path - SAP Functional Consultant
- 500 Hours
- GBP 99
- 7893 Learners
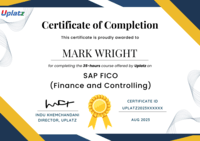
This SAP Supply Chain Management (SAP SCM) course is a bundle of relevant courses provided by Uplatz consisting of self-paced videos on the following SAP modules under SAP SCM:
1.SAP APO (Advanced Planner and Optimizer)
2.SAP MM (Materials Management)
3.SAP PP (Production Planning)
4.SAP SD (Sales and Distribution)
5.SAP WM (Warehouse Management)
6.SAP EWM (Extended Warehouse Management)
7.SAP S/4HANA MM, Sourcing & Procurement
8.SAP S/4HANA EWM (Extended Warehouse Management)
9.SAP S/4HANA TM (Transportation Management)
10.SAP S/4HANA Logistics
11.SAP S/4HANA SD (Sales and Distribution)
12.SAP Ariba Sourcing
13.SAP Ariba Procurement
Supply Chain Management (SCM) plays a crucial role in modern business operations, ensuring the efficient flow of goods, services, information, and funds from raw material suppliers to end customers. SAP SCM (Supply Chain Management) is a suite of software solutions designed to streamline, optimize, and manage various aspects of the supply chain process. In this article, we will delve into the key components of SAP SCM and its significance in today's competitive business landscape.
Key Components of SAP SCM
1.Demand Planning: SAP SCM offers demand planning tools that enable organizations to forecast customer demand accurately. These tools use historical data, market trends, and statistical algorithms to create demand forecasts, helping businesses optimize inventory levels and align production accordingly.
2.Supply Network Planning: This component focuses on optimizing the distribution of products across various locations within the supply chain network. It considers factors such as production capacities, transportation constraints, and lead times to ensure products reach customers efficiently.
3.Production Planning and Detailed Scheduling (PP/DS): PP/DS helps organizations manage production processes by creating detailed production schedules based on demand forecasts, inventory levels, and resource availability. It optimizes production plans to meet customer demands while minimizing costs and maximizing resource utilization.
4.Logistics Execution: This component handles the physical movement of goods through the supply chain. It includes functionalities such as transportation planning, warehouse management, and order fulfillment. SAP SCM ensures timely delivery of products to customers and efficient management of inventory in warehouses.
5.Global Available-to-Promise (Global ATP): Global ATP provides real-time information about product availability, considering current stock levels, incoming shipments, production orders, and customer orders. This helps sales and customer service teams provide accurate delivery promises to customers.
6.Supplier Network Collaboration (SNC): SNC allows organizations to collaborate with their suppliers to optimize procurement processes. It facilitates communication, demand visibility, and order management between organizations and their suppliers.
7.Integrated Business Planning (IBP): IBP brings together different aspects of the supply chain, including demand, supply, finance, and sales, to create a unified plan. It enables organizations to align their strategic, tactical, and operational plans to achieve their business goals.
8.Advanced Planning and Optimization (APO): APO is an older module within SAP SCM that focuses on advanced planning techniques like optimization, simulation, and scenario planning. However, SAP is transitioning its functionality to newer modules like SAP IBP.
Uplatz provides this bundle course covering each SAP SCM module in detail. You will learn the practical implementation, configuration, and management of the SAP modules involved in complete supply chain management processes within an organization.
Course/Topic 1 - SAP APO (DP and SNP) - all lectures
-
In this introductory lecture we learn about what is Supply Chain Management, how to do Advance Planning and Optimization (APO) in SAP SCM. And we will see different modules of APO.
-
In this lecture we learn about configuration part of the demand planning life cycle, and also its end-to-end implementation. And discuss about different topics such as planning area, storage and bucket, master forecast profile.
-
In this lecture we talk about the master planning part of MPOS.
-
In this lecture we talk about the part 2 of MPOS that is the characteristics of Object Planning.
-
In this session we will talk about the planning area of MPOS then designing of the Planning book.
-
In this lecture we will cover the creation of master forecast profile, Univariate profile, Multiple Linear Regression Profile in detail.
-
In this session we will talk about the important features of SAP APO that are Macros, Life cycle Planning, and Alert management. We will discuss Life cycle planning in detail.
-
In this lecture we will talk about the feature Macros in detail.
-
In this lecture we will talk about the feature Macros in detail.
-
In this session we will talk about the extended feature of Macros feature that is Alert management in detail.
-
In this lecture we will talk about the background jobs and mass processing of SAP DP.
-
In this lecture we talk about the topic proportional factors of SAP APO DP.
-
In this lecture we will learn how to pass final demands to SNP.
-
In this lecture we will study about the product and location split topic.
-
Here we will study about the infocube of the BW data.
-
In this lecture we will study in detail about the core Interface of the SNP.
-
In this lecture we will talk about the supply network planning and an overview of its administrative data.
-
In this lecture we study about the master data of SNP
-
In this lecture we study about the master data of SNP, product, location, resource etc of SNP.
-
In this lecture we will talk about the safety stock planning, and SNP planning run, Heuristic, optimization, and capable to match.
-
Here in this lecture we will learn about the feature optimizer of APO in detail.
-
In this lecture we will study about one of the MRP engine of APO that is CTM.
Course/Topic 2 - SAP MM (basic to advanced) - all lectures
-
In this first video of the Introduction to ERP & SAP course, you will get a brief introduction to ERP like what is ERP, why it is used, what are the characteristics for a software product to be called as an ERP product, what is planning and resources and others. Further, you will get an introduction to SAP, the divisions of the basic product namely Functional, Technical and Administration.
-
This tutorial teaches a step-by-step approach to acquaint the readers with the SAP MM environment and how to make good use of its features. It will also help students to perform procurement of stock materials in SAP.
-
Organization structure is the framework of a company according to which business is conducted in every company.
-
Organization structure is also referred as enterprise structure. Enterprise structure is made up of many organizational units having relationship with one another.
-
Organization structure consists of many levels having direct or indirect relationship with one another.
-
This video will look at one of the company units, SAP Controlling Area, on a more detailed level. The intent is to help you understand how the Controlling Area organizes postings within the CO module and how it integrates with Financial Accounting (FI).
-
This tutorial which is part of our SAP MM course talks about SAP MM Material Master in Materials Management. You will learn about material master records in SAP MM, their functions, and how to create a new material in SAP. We will mention the SAP transactions that are related to this process.
-
SAP MM Material Master is an important element of master data in SAP which is used by most of the departments in a company. SAP MM material master enables the company to store all the information about a particular material (or product).
-
This session includes material master and vendor master. Material and vendor master are separate data records for keeping information of materials and vendors from where material is procured. The combined information of material and vendor altogether is kept in a record that we call as purchase info record.
-
A particular material can be procured from different vendors depending upon the requirement. In this way, the total requirement of a material is distributed to different vendors, which is the quota is assigned to each source of supply.
-
SAP ERP was introduced so that procurement can be done efficiently in terms of time and cost. Procurement can be done for various types of goods and services. Procurement starts with creating a purchase order which is a formal document given to vendors and it includes a list of goods and materials that are to be procured.
-
This video shows the purchase orders can be created for different types of procurement.
-
This chapter describes some of the important configurations in SAP MM. SAP MM is flexible enough to allow its configurations to be modified in the background to suit the business requirements of an organization. Configurations help in making custom enhancements in the structure.
-
Vendor selection is an important process in the procurement cycle. Once requirements are gathered, we start looking for possible suppliers who can fulfil the requirements at the best possible price.
-
A contract is a longer-term agreement with a vendor (one of the two forms of “outline agreement” in the SAP system) to supply a material or provide a service for a certain period of time.
-
A contract is a long-term outline agreement between a vendor and an ordering party over a predefined material or service over a certain framework of time.
-
Scheduling agreements are defined and managed as documents in the system.
-
In this part, we will configure all things which is required for quota arrangement.
-
A purchasing document is an instrument used by Purchasing to procure materials or services.
-
It is an approval process for Purchasing requisition and external Purchasing documents.
-
Pricing procedure in MM module is a way to determine prices in purchasing documents. It gives us functionality to assign different calculation types for different needs
-
Service master record contains the details of all the services that can be procured from an external vendor within an organization. It contains the description of services along with their unit of measure.
-
Inventory management deals with placing and handling the stock received from the vendors in correct place within the company’s premises.
-
Procurement process starts with gathering requirements and ends with procuring goods from vendors. Once the goods are procured from a vendor, they need to be placed in the company’s premises in correct place so that they can be consumed when required.
-
Inventory management deals with the management of stock, either on value or quantity basis.
-
Considering you have basic understanding of the process as discussed above let us jump in to the functional and technical process of the same.
-
This component allows you to carry out a physical inventory of your company’s warehouse stocks for balance sheet purposes. Various procedures can be implemented for this.
-
Inventory for a company’s stock and for special stocks (such as consignment stock at customer, external consignment stock from vendor, or returnable packaging) must be taken separately (in different physical inventory documents),
-
This video will help you to learn about SAP MM Batch Management Process.
-
In this video, we will learn about invoice verification in sap mm.
-
This video is about SAP FI MM integration flow. Learn the integration of SAP MM with SAP FI in depth.
-
In this video, we describe the major aspects of SAP MM integration with SAP PP module.
-
In this session, you get detailed knowledge of integration of SAP MM with SAP SD module.
-
This last video will help to provide a detailed process of integration of SAP MM and SAP WM modules.
Course/Topic 3 - SAP PP course - all lectures
-
Lecture 1 - SAP PP Introduction
-
Lecture 2 - Master Data in PP
-
Lecture 3 - Configuration Settings for Master Data - part 1
-
Lecture 4 - Configuration Settings for Master Data - part 2
-
Lecture 5 - Material Master - part 1
-
Lecture 6 - Material Master - part 2
-
Lecture 7 - BOM in PP
-
Lecture 8 - Work Center in PP
-
Lecture 9 - PRT and Routing
-
Lecture 10 - Production Version and Different Types of Scrap
-
Lecture 11 - Scraps - Assembly and Component and Operation
-
Lecture 12 - MRP Planning and Consumption-based Planning
-
Lecture 13 - Forecast-based Planning and Time-phased Planning
-
Lecture 14 - Automatic Reorder Point (ROP) Planning and Manual ROP Planning
-
Lecture 15 - Internal Procurement Process - part 1
-
Lecture 16 - Internal Procurement Process - part 2
-
Lecture 17 - Internal Procurement Process - part 3
-
Lecture 18 - Internal Procurement Process - part 4
-
Lecture 19 - Batch Management in PP
-
Lecture 20 - Serial Number Management in PP
-
Lecture 21 - Sales and Operations Planning - SOP
-
Lecture 22 - Strategy Group for MTS and MTO Process
-
Lecture 23 - Strategy Group 25 - MTO Configurable Material or Variant Configuration
-
Lecture 24 - SAP PP integration with SAP QM
-
Lecture 25 - Availability Check in MRP and Introduction to MPS
-
Lecture 26 - Master Production Schedule (MPS)
-
Lecture 27 - Repetitive Manufacturing Process
-
Lecture 28 - SAP PP integration with SAP PI
-
Lecture 29 - SAP PP integration with SAP FI
-
Lecture 30 - Creating Order Types and Production Scheduling Profile
Course/Topic 4 - SAP SD (end-to-end) - all lectures
-
In this session, we learn about SAP System Landscape, types of SAP users and OTC.
-
In this session, we learn about defining Company, Company Code and Sales Organisation.
-
In this session, we learn about defining Distribution Channel, Division, Sales Office and Sales Group.
-
In this session, we learn about defining plant, Storage location, Shipping point and assignment of Sales Organisation to Company Code.
-
In this session, we learn about assign Distribution Channel to Sales Organisation, assign Division to Sales Organisation, Set up Sales Area and assign Sales Office to Sales Area.
-
In this session, we learn about assign Sales Group to Sales Office, assign Plant to Company Code, assign Sales Organisation and Distribution Channel to Plant, Common Distribution Channels and Common divisions.
-
In this session, we learn about assign sales Area to Sales Document type, assign Shipping point to plant, assign warehouse to plant and Storage location and Shipping point determination.
-
In this session, we learn about activate accounts receivable pledging procedure, Set Company code to Productive, assign Company Code to Financial Management Area, Global Company Code,assign Company Code to Fiscal year Variant, Chart of Accounts and Field Status Variant, materials management view on Accounting and Stochastic Block Values.
-
In this session, we learn about assign Chart of Depreciation and Work-Flow Variant to Company Code and allocate company Code to Non-Taxable Transactions.
-
In this session, we learn about cost of Sales accounting, Maximum Exchange Rate and Credit Control area.
-
In this session, we learn about assigning Controlling Area and Profit Centre to Company Code.
-
In this session, we learn about MRP Controller for plant, Scheduling Margin Key, Material type Quntity/value updating,assign Plant and Division to Business area, assign Plant to valuation Grouping Code and Plant Parameters.
-
In this session, we learn about assign Sales Area to Credit Control Area and assign Maintenance Planning Plant to Maintenance plant.
-
In this session, we learn about different fields in General Data Screen in Customer Master.
-
In this session, we learrn about different fields in Company Code Data and Sales Area Data screen.
-
In this session, we learrn about next part of different fields in Sales Area Data screen.
-
In this session, we learrn about further part of different fields in Sales Area Data screen.
-
In this session, we learn about further part of fields in Sales Area Data Screen
-
In this session, we learn about remaining part of fields in sales Area data screen.
-
In this session, we learn about Customer account Group and create number ranges for Customer Account group.
-
In this session, we learn about create Partner Functions for Customer account Group.
-
In this session, we learn about creating a new Customer.
-
In this session, we learn about different fields in Basic Data 1 and Sales. Sales Org 1 Screens.
-
In this session, we learn about different fields in Saes. Sales Org 2 Screen.
-
In this session, we learn about different fields in Sales. General/Plant Screen, MRP 1 Screens.
-
In this session, we learn about Different fields in MRP 2, MRP 3, General Plant/Storage, warehouse Management 1 and Accounting 1 Screens.
-
In this session, we learn about Creating a new Material, Initial uploading of Stock and Display of Stock in Plant/Storage Location.
-
In this session, we learn about Condition Technique, Condition records, Condition Table, Access Sequence.
-
In this session, we learn about different fields in Condition Type.
-
In this session, we learn about next part of different fields in Condition Type.
-
In this session, we llearn about remaining part of Condition Type and different fields in Pricing Procedure
-
In this session, we learn about remaining fields in Pricing Procedure and creation of Pricing Procedure.
-
In this session, we learn about remaining part of creation of Pricing Procedure, Pricing Determination, Condition Master and Material Listing.
-
In this session, we learn about different fields in General Control tab.
-
In this session, we learn about next fields in General Control tab.
-
In this session, we learn about further fields in General Control tab.
-
in this session, we learn about remaining fields in General Control tab and fields in Transaction Flow tab.
-
In this session, we learn about remaining fields in Transaction Flow tab, fields in Scheduling Agreement and Shipping tab.
-
In this session, we learn about remaing fields in Shipping tab, fields in Billing tab and Requested Delivery date tab.
-
In this session, we learn about fields in Business Data tab.
-
In this session, we learn about remaining fields in Business data tab.
-
In this session, we learn about fields in General Control tab, Transaction Flow tab and Bill of Materials/Configuration tab and Schedule Line Categories.
-
In this session, we learn about Inquiry, Quotation and Sales Order.
-
In this session, We learn about Return Process, Credit Memo Request and Debit Memo Request.
-
In this session, we learn about Rush Order, Cash Sales and Free of Charge Delivery.
-
In this session, we learn about Quantity Contract, Scheduling Agreement and Consignment Fill Up.
-
In this session, we learn about Consignment issue, Consignment Pick Up and Consignment Return
-
In this session, we learn about Delivery, Transfer Order, Post Goods Issue, Invoice and Invoice Correction Request.
-
In this session, we learn about configuration of Inter Company Sales.
-
In this session, we learn about Configuration of Cross Selling.
-
In this session, we learn about Configuration of Free Goods.
-
In this session, we learn about Configuration of Third Party sales.
-
In this session, we learn about Configuration of Credit Management.
-
In this session, we learn about ASAP Methodology for Implementation Project.
-
In this session, we learn about next part of ASAP Methodology for Implementation Project.
-
In this session, we learn about remaining part of ASAP Methodology for Implementation Project and Support Project.
-
In this session, we learn about remaining part of ASAP Methodology for Support Project.
Course/Topic 5 - SAP WM course - all lectures
-
In this first lecture session of SAP WM ( Warehouse Management) we learn about basics of SAP WM and also cover the significance of WM.
-
In this lecture session of SAP WM we give an introduction of SAP WM and a basic overview of SAP WM.
-
In this lecture session we talk about SAP Warehouse and management WM structural elements SAP and hands on.
-
In this lecture session we learn about organization object warehouse number and also talk about system demo.
-
In this lecture session we talk about SAP WM storage bins as warehouse management master data.
-
In this lecture session we talk about the interface between IM and WM and also talk about the basic difference between IM and WM.
-
In this lecture session we learn about material master influence in SAP and also talk about the master data.
-
In this lecture session we introduce you to the stock category and also talk about different types of stock categories in SAP.
-
In this lecture session we talk about putaway picking strategies and also overview the basic strategies of SAP.
-
In this lecture session we talk about inbound processes in SAP WM and also talk about put away in SAP WM.
-
In this lecture session we talk about simple inbound processes in SAP WM and also talk about inbound and outbound processes.
-
In this lecture session we talk about simple outbound processes in SAP WM and also talk about basic differences between inbound and outbound processes of SAP WM.
-
In these lecture sessions we learn about basic understanding of material master WM1 & WM2.
-
In this lecture session we learn about transfer requirements and transfer order in SAP WM and also talk about warehouse management views.
-
In this lecture session we learn about WM structural elements and customizing.
-
In this lecture session we learn about automatic creation of storage bins.
-
In this lecture session we talk about Fixed bin strategy for picking and also cover best techniques for picking the data.
-
In this lecture session we talk about fixed bin strategy for stock putaway in SAP WM and also cover basic difference between picking and stock putaway.
-
In this lecture session we learn about putaway for inbound delivery in SAP WM.
-
In this lecture session we learn about bin to bin movement in SAP WM and also talk about movement of stocks and putaway.
-
In this lecture session we learn about IM and WM linkage and also cover the difference between IM and WM.
-
In this lecture session we learn about Stock placement control in SAP WM and also talk about control in master data.
-
In this lecture session we talk about stock removal control in SAP WM and also talk about the basic difference between placement control and removal control.
-
In this lecture session we learn about batch determination and also cover types of batches in SAP WM.
-
In this lecture session we learn about WM driven operation and also cover basic operations of SAP WM.
-
In this lecture session we learn about WM movement types and also talk about different types of movement present in SAP WM.
-
In this lecture session we learn about physical inventory difference in SAP WM and also cover the master data.
-
In this lecture session we learn about how we change the posting process in SAP WM and also talk about the best techniques of posting the changes.
-
In this lecture session we learn about capacity check control in SAP WM and also cover the best way of checking the capacity control in SAP WM.
-
In this lecture session we learn about warehouse implementation and blueprinting of SAP WM and also overview the blueprint of implementation of SAP WM.
Course/Topic 6 - SAP EWM - all lectures
-
In this video, you will be presented with a basic understanding of what is a logical system, RFC connection and their respective configuration. You will be introduced to Plant, how to assign plant in company code and about storage location. Further, you will be preceded with warehouse known as intermittent between plant storage and EWM warehouse.
-
In the session, you will learn how to define business system and assignment of the same in logical system. You will have an understanding of EWM warehouse and its customizing. Further, you will be preceded with a mapping warehouse and pushing plant from ECC to EWM.
-
In this video, you will learn about the supply chain, supply chain unit and how the supply chain unit is mapped to the warehouse. You will also learn how to check the entire connectivity of ERP – SAP EWM configuration.
-
In the session, you will have an in-depth understanding of how the material is created in ECC, its configuration and then shifted to EWM. You will also run how to check the material in SAP EWM and configuration of extending or creating warehouse data for cuffing the material in SAP EWM system.
-
In this video, you will learn about how to CIF the vendor to SAP EWM from ECC using two transactions- CMF1 & CMF2. Further, you will be preceded by how to check whether the vendor has CIF to SAP EWM or not along with the configuration.
-
In this video, you will have a deeper knowledge of warehouse structure from warehouse number, storage type, storage section, storage bin and quantity. You will also learn the four types of storage type and their configuration. Further, you will be preceded with the creation of Storage Section and Storage Bin.
-
In the session, you will learn how to define an activity, assignment of the storage bin to new activity area. You will also learn sorting sequence for an activity area followed by Bin sorting along with the configuration of each step.
-
In the session, you will be explained in a detailed what is work center, where it can be used in the processing and its use. You will also learn the configuration of the work center for all warehouses.
-
This video serves as a break so as to allow you time to revise all previous lectures of SAP EWM.
-
In the session, you will learn about the warehouse process type and why we need this in the system. You will know how to define warehouse process type and control indicators. Further, you will be preceded with a configuration of assigning control indicators to warehouse process type.
-
In this lecture, you will be presented with the deeper understanding of what is availability group and stock type. Further, you will be preceded with how to define an availability group, configuration of stock type, assigning it to stock type and mapping location from ERP system to EWM.
-
In the session, you will learn about the storage type search location and its assignment. You will also learn how to define put away control indicators and specify storage type. Further, you will be preceded with a configuration of storage location and how to create storage section indicators.
-
In the session, you will be presented with the configuration of material and vendor to EWM followed by the configuration of purchase order in ECC, creation of inbound delivery for a purchase order in ECC and finally goods receipt in SAP EWM.
-
In the session, you will be presented with the flowchart of the entire previous lecture and a brief explanation of all topics that had been covered till now.
-
In the session, you will two processes, first how to block the bins or unblock the bins and the second process is how to do mass changes of bins followed by several steps and their respective configuration.
-
In this video, you will learn how to put the stock in the particular bin. What are the settings and configuration is required in a system from creating a new storage type to run the inbound process for a material?
-
In this video, you will have a deeper knowledge of how to scrap or block goods followed by several steps from how to define new storage type to creating warehouse to move the material into scrap bin along with their respective configuration.
-
In the session, you will learn how outbound delivery will flow from the ERP system to the SAP EWM system. Further, you will be preceded with a configuration of each ERP setting, EWM settings and integration of EWM ERP. You will also have an idea of when system is ready for the distribution of outbound delivery from ECC to EWM.
-
In the session, you will be presented with the path on how to set up ECC in organisation followed by several steps and their respective configuration and assignment.
-
In this video, you will learn how to create customer, how to create a sale order for a customer & outbound delivery for sale order. You will also learn the distribution of outbound delivery to the EWM system along with the configuration of each step.
-
In the session, you will be explained in a detailed how goods issued once the sale order created and outbound delivery in SAP EWM. You will learn how goods will be picked from EWM, how the testing will be done in the system and the use of stock removal strategy to pick the goods from the bin along with their configuration.
-
In this lecture, you will learn how goods will be picked automatically from the bin. There are different stock removals strategies, in this video; you will see how removal strategy is defined. Further, you will be preceded with standard strategy of stock removal - FIFO & LIFO along with the configuration.
-
In this video, you will learn how goods are issued directly for consumption to cost centre for partner or for internal people. You will also learn how it will be directly done in EWM and how to set up cost centre followed by pre-request and configuration of several steps and process to have direct consumption to cost centre.
-
In the session, you will have a deeper knowledge of physical inventory, where one cross check the stock to make sure physical stock is present in the system. You will also learn about the two types of it and the three types of inventory procedure to carry this process. Further, you will be preceded by steps to follow the configuration of physical inventory setting in a warehouse.
-
In the session, you will be presented with the process to carry the physical inventory in the warehouse. There are 5 steps from creating a physical inventory to checking inventory in ECC along with their respective configuration.
-
In this video, you will learn about posting changes. You will also learn about the two methods of posting changes: one in EWM and the other in ERP. Further, you will be preceded with settings and configuration of EWM and in ECC respectively.
-
This video is a continuation of the previous lecture, where you will learn the process of posting changes in ERP and EWM followed by several steps and their respective configuration.
-
In the session, you will learn about replenishment, i.e. the movement of goods from warehouse to shipment location. There are three common fields for replenishment. You will also learn about the types of replenishment and configuration of how to create replenishment followed by several steps.
-
This video is a continuation of the previous lecture, where you will learn about three types of replenishment process in detail along with their configuration and assignment.
-
In the session, you will be explained in a detailed what is cross-docking, where it can be used, types of cross-docking and configuration set up required for EWM cross-docking followed by several steps.
-
In this video, you will learn about the cross-docking process in detail. There are 8 steps in the process from creating a sale order in ECC to check purchase order & sale order in ECC followed by their respective configuration.
-
In the session, you will learn about what is slotting, what are the four types of parameters in slotting and condition techniques in slotting. Further, you will be preceded with the configuration set up required in the process to determine slotting.
-
In the session, you will learn how the slotting process will run in the real-time. The process is consisting of five steps from creating material in ECC to check material again in detail with their respective configuration.
-
In the session, you will learn about post process framework, its use as a tool for scheduling, starting and monitoring actions. You will also learn about the structure of PPF. Further, you will be preceded with PPF configuration set up in detail in three steps.
-
In the session, you will be presented with how the PPF will perform in inbound delivery. You will also learn about the PPF process in detail followed by four steps from creating a purchase order in ECC to goods receipt and print GR slip, along with their respective configuration.
Course/Topic 7 - SAP S/4HANA MM Sourcing and Procurement - all lectures
-
In this lecture session we learn about SAP S4HANA MM. In this we give you a basic introduction about SAP S4 HANA and also talk about basic functions and factors of SAP S4HANA MM 1909.
-
In this lecture session we learn about SAP S4 HANA split valuation and OBYC and also talk about how we run SAP S4 HANA and what is transaction in split valuation.
-
In this tutorial we learn about SAP S/4HANA Cloud is a next-generation, intelligent ERP business suite designed specifically for in-memory computing and also talk about different essential functions of SAP S4HANA.
-
In this lecture session we learn about The SAP S4 Hana system provides standard BP Roles and BP role categories for customers to meet the business requirements. We can define new BP roles by copying from standard BP Roles.
-
In this lecture session we learn about SAP S4HANA stock material procurement process in SAP S4HANA and also talk about basic understanding of stock material procurement process in SAP S4 HANA.
-
In this lecture session we learn about SAP S4HANA consumable material procurement process and also talk about features and function of SAP S4HANA.
-
In this lecture session we learn about SAP S4HANA enterprise structure configuration and master and also talk about Each SAP Business Role is matched by a security/authorizations role in your SAP S/4HANA system that can be assigned to the users who perform that business.
-
In this lecture session we learn about basic understanding of SAP S4 HANA material planning and also talk about features and function of material planning.
-
In this lecture session we learn about SAP S/4HANA Supply Chain The SAP S/4HANA Supply Chain LoB focuses on overall business planning activities, from pre-planning production runs to dispatching products to purchasers.
-
In this lecture session we learn about Gain in-depth purchasing insights, streamline operational purchasing, automate sourcing and contract management, centralize procurement processes, manage commodity procurement, effectively reduce supply chain risk, and more with the help of SAP S/4HANA.
-
In this lecture session we learn about With S/4HANA central procurement, S/4HANA on-premise system acts as a central hub, connect to the regional SAP ERP, S/4HANA cloud as well as S/4HANA on-premise. Minimum system requirement for the connected SAP ERP is 6.0 EHP 6.0.
-
In this lecture session we learn about This course offers a comprehensive overview and in-depth knowledge about inventory management and physical inventory in SAP S/4HANA. After attending this course, you will understand the major business processes, functions and configuration.
-
In this lecture session we learn about SAP ERP Logistics Invoice Verification is part of Materials Management (MM). You use it to enter invoices and credit memos and check them for arithmetical correctness, and to make sure that you have been charged the right price for the right material or service.
-
In this lecture session we learn about SAP S4HANA physical inventory management and also talk about This course offers a comprehensive overview and in-depth knowledge about inventory management and physical inventory in SAP S/4HANA. After attending this course, you will understand the major business processes, functions and configuration.
-
In this lecture session we learn about n the earlier versions of SAP ECC, ‘material master’ used to have the indicator batch management to maintain the materials in multiple lots or batches. However, now S/4HANA has an additional indicator called ‘batch management in the plant.
Course/Topic 8 - SAP S/4HANA EWM 1909 - all lectures
-
In this first video on the SAP S/4HANA EWM course, you will get a briefing on the course contents, the objective of the training, and some basic terminologies associated with the Embedded Extended Warehouse Management system.
-
In this video, you will learn about Supply Chain Management starting with a diagrammatic representation of the high-level process of SCM, the definition of EWM, the business functions of EWM, a brief explanation on the De-Centralised EWM, EWM Master Data Distribution, the transaction data flow of De-Centralized EWM, the data transfer process between S4HANA and EWM, Warehouse Layout & many others.
-
This video is a complete practical session on Warehouse Product Maintenance and the complete work process of it will be shown by the trainer in the SAP system.
-
In this video, you will learn about the different terminologies associated with SAP Warehouse Management, whether be it the S/4HANA or EWM. Along with this, you will also learn about the different reasons for deploying Embedded EWM in SAP S/4HANA 1909 instead of Decentralized SCM EWM. Furthermore, you will also learn about the mapping process of S/4HANA Document Type to EWM Document Type.
-
In this video, you will learn about the different processes associated with the Extended Warehouse Management starting with an overview on the Inbound Process; its roles and the process flow, the Outbound Process, the 5 specific warehouse areas, WM Complex Processes, U Flow Layout Design, Slotting & Rearrangement, the difference between WM and S/4HANA EWM and many more.
-
In this session, you will learn about the Slotting & Rearrangement process in S/4HANA Embedded EWM along with the Internal Warehouse Process, Transfer Posting in EWM, Goods Receipt Process in EWM, S/4HANA EWM Master Data, and others.
-
In this video, you will learn about the different stock removal strategies such as FIFO, Stringent FIFO, LIFO, Partial Quantities & others with a detailed explanation of each of them. You will also learn about the complete work process of Storage Control.
-
This is a complete practical session on how to work on the process of Purchase Order and maintaining the Inbound Delivery in the SAP system. The trainer will be showing a step-by-step process of the complete procedure in the SAP system.
-
In this session, you will learn the configuration steps involved in the storage control of POSC with a detailed work process of it being shown in the SAP system.
-
This session will teach you on the work process of Document Flow and other in case of Storage Control in the SAP system.
-
In this video, you will learn about the Process-Oriented Storage Control in Inbound Process with an example and a diagrammatic explanation along with the Material Flow System which will be shown by the trainer in the SAP system.
-
The first part of this video is a revision of the previous sessions being held on various topics. The latter half of the session is for the Activities to be done in EWM like defining availability group, defining non-location-dependent stock type, configuration stock type, and assigning availability group to storage type. All these 4 activities will be shown by the trainer in the SAP system.
-
In this session, you will get practical lessons on the Packaging work procedure for the SAP Extended Warehouse Management system.
-
In this video, you will learn about the Post Processing Framework, commonly abbreviated as PPF, and the configuration of the Work Center in the SAP system.
-
This is the second part of the Post Processing Framework video where you will get some theoretical concepts on PPF like understanding the concept of PPF, the structure of Post Processing Framework, how PPF is used in connection with delivery processing in EWM, the configuration steps for connecting PPF to delivery processing and others.
-
This video is a practical session on Product Description and Wave Management where you will learn the complete work process in the SAP system. The trainer will be showing each and every step in the SAP system.
-
In this video, the trainer will be showing the work procedure of the physical inventory system along with the other tasks associated with it in the SAP system.
-
In this video, you will learn the Inbound and Outbound Processing associated with SAP S/4HANA EWM and its work process in the system.
-
This is a practical session where you will learn and implement the concept of the Putaway Control Indicator in the SAP system.
-
In this video, you will learn about the work procedure of Inbound Delivery associated with the Warehouse Management in the SAP system.
-
This video is a refresh session summary on the topics and agenda already covered throughout the whole course.
-
In this video, you will get a brief overview of the Warehouse Management Complex Processes along with the Warehouse Material U Flow Layout Design, High-Level Process of Supply Chain Management, and the Process Flow in SCM.
-
In this video, you will get a detailed explanation of the SAP EWM Organizational Structure, the terminologies related to the Org Structure such as Warehouse Number, Storage Type, Storage Section, Storage Bin, and Quant.
-
In this last video of the SAP S/4HANA course, you will learn about the maintenance procedure of SCM in the SAP system along with a detailed explanation on Master Data which will be shown with a detailed step-by-step procedure in the SAP system.
Course/Topic 9 - SAP S/4HANA TM - all lectures
-
In this first video of the SAP S/4HANA TM course, you will get a brief overview on the course contents, starting with a graphical representation of the whole S/4HANA TM structure, explaining each and every part of it along and the definitions of terminologies related to the HANA TM module.
-
In this video, you will get a detailed understanding on the Global Supply Chain of the Transportation Management along with the history of Transportation Management and the key benefits of the same.
-
In this video, you will learn about the Organizational Units along with its concepts like Organizational Function, Integration which will be explained by the trainer in the SAP system.
-
In this video, you will learn about the objectives of the S/4HANA Transportation Management with the Process View and Technical Component, Order Management, Package Building, Transportation Planning, Freight Planning Capabilities, Visual Load Planning and the Driver Management.
-
In this video, you will learn about the implementation of Logical Systems in the SAP S/4HANA Transportation Management with a detailed explanation of each and every part in the SAP system.
-
In this session, you will get a detailed understanding of the Personal Object Worklist or commonly abbreviated as POWL along with a diagrammatic explanation of Transportation Management UI on FPM combining app views. Furthermore, you will also learn about the Master Data requirements in SAP TM.
-
In this video, you will learn about the complete end-to-end work process of the Transportation Management along with the TM Landscape, explaining every component in it. Further, you will also learn about the Software Component of Transportation Management.
-
: In this video, you will get a complete overview of SAP NetWeaver Business Client with a detailed understanding of each and every part of it. Along with this, you will also learn about the Transportation Management “Search” option and the uses associated with it.
-
In this video, you will get a detailed understanding on the Transportation Execution along with the TM Freight Costing and the TM Document Flow. You will get a detailed understanding on each of these by the trainer throughout the session.
-
In this session, you will learn the different TM related Master Data with a detailed understanding on Geocoding, Transshipment Location, Transportation zones and Transportation lanes which will be shown by the trainer in the SAP system.
-
In this video, you will learn about the Mater Data Integration starting with an understanding on the Integration Model, Activation of the Integration Model, defining the Location Type in TM, Business Partner in TM and the Transportation Requests for SAP TM.
-
: This session will teach you on the Incompatibility Validity concept associated with the SAP TM along with the Incompatibility Types, understanding of Integration of SAP EHS with TM, the Incoterm, Segment Scheduling and the Transit Time.
-
In this video, you will learn about the Organizational Management and its complete step-by-step procedure in the SAP system.
-
In this video, you will learn about some more details related to the S/4HANA TM – its key benefits, the Order Management of TM, the BI Warehouse Content with Transportation Management, the details on the Transportation Management Software Component and the SAP NWBC for Desktop.
-
In this video, you will get a detailed understanding on the Personal Object Worklist or POWL, along with an overview of TM UI and the Master Data Requirements in SAP TM. You will also learn about the Transportation Resources, the Distance-Duration calculation in TM Master Data requirement, an understanding on the Organization Structure Evaluation and others.
-
In this video, you will learn the process flow between the Shipper and the Carrier for the Transportation Management. You will also learn about the Shipping Condition and the work process of it along with the Order Management.
-
: In this video, you will learn about the concept of Freight Unit along with its different parameters, FUBR, the Consolidation and these will be shown by the trainer with every detail in the SAP system.
-
In this session, the trainer will be seen teaching the Transportation Cockpit and its complete work process in the SAP system.
-
In this video, you will learn to create a selection profile and working on the Transportation Cockpit which will be shown by the trainer in the SAP system with every detail.
-
Transportation Cockpit Description: In this video, you will learn about the Selection Profile being used in the SAP Transportation Management and how to work on it in the SAP system.
-
This is a continuation video to Transportation Cockpit where you will learn about the time related selection attributes and planning and how to work on it in the SAP system for the Transportation Management.
-
In this video, you will learn about the Freight Order Management with its detailed concepts associated with it like Structure of Freight Order, Freight Order Types, Freight Order Type Determination and others which will be shown by the trainer in the SAP system.
-
In this session, you will learn about the work process of a new Carrier Selection Setting and its implementation in the SAP Transport Management.
-
In this video, you will learn about the implementation steps associated with the Freight Order Forwarding along with working with the Freight Unit Types in the system.
-
In this video, you will learn about the concept of Tendering in the Transportation Management module along with other details such as peer-to-peer and freight order with Subcontracting. These will be clearly shown by the trainer in the SAP system.
-
In this video, you will see the different work processes being used in the Transportation Management with transferring the Carrier and working with the Integration Model.
-
In this last session on the SAP S/4HANA TM course, you will learn about the concept of Transportation Charge Management along with a detailed explanation on LSP, Business Requirement, Master Data in Charge Management, Scale Base and the details of Scale Template in the SAP system.
Course/Topic 10 - SAP S/4HANA Logistics course - all lectures
-
In this video, you will be introduced to SAP S/4HANA, where it started and where it is now. You will be also introduced to what was the sudden need for SAP to look at the new product launch and how data plays an important role in that. You will also learn the challenges faced by the IT & businesses and what were the pain points.
-
In the session, you will have a deeper knowledge of the evolution of S/4HANA from 1973 to till now. You will be introduced to four sets of services offered in SAP S/4HANA. Further, you will be preceded with what are the differences in old and new way data analytics technology. You will also learn about the user experience.
-
In this video, you will be introduced to SAP Fiori Apps types, core functions of SAP S/4HANA and its business scope. You will also learn about the new improved functionality of S/4 HANA, i.e. system data module and user experience. Further, you will be preceded with principles of S/4 HANA.
-
In this video, you will learn about the direct path of SAP S/4HANA master data, how SAP S/4HANA handles material requirement planning and material shortage. You will also learn about sourcing and procurement business scenario with and without HANA. Further, you will be preceded with supply chain management integrated with SAP S/4HANA.
-
In the session, you will be presented with the detailed explanation of, in which cases; any customer would like to go for conversion or implementation. In the SAP S/4HANA, there are two types of implementation, about which you will be explained in detail along with their framework. You will also learn about the evolution of customer code checks.
-
In this video, you will learn how SAP started functioning using ASAP methodology and its five cases. You will also learn about the innovation adoption framework for SAP S/4HANA and how to deploy it with SAP activate. Further, you will be preceded with best practices for SAP S/4HANA followed by some examples.
-
This session covers all the basics that had been covered till now. You will be presented with the basic of SAP S/4HANA and a detailed explanation of the path that HANA has covered from 1973 to 2015.
-
In this video, you will learn how SAP S/4HANA is different from ECC and the changes that have been done in SAP S/4HANA. Further, you will be preceded by a detailed explanation of SAP S/4HANA material and operations management. You will also be introduced to the basics of business partner and SAP EWM.
-
In this video, you will learn about Hana Modeler, what are the views, analytics, etc. You will also learn how it is used to create all info views on schemas & tables on HANA database. Further, you will be introduced to dimensions & measures, Schemas, snow flex schema, galaxy schema and data modelling. You will also learn about the licensing of HANA and its two types.
-
In the session, you will have a deeper knowledge of SAP Fiori - an integral part of SAP S/4HANA. You will also learn how it has been aligned to all the businesses and what Fiori apps library is. Further, you will be preceded with the architecture in which Fiori works, SAP net weaver gateway and how they do configuration for the set up.
-
In this video, you will be presented with a detailed explanation of SAP HANA architecture, what are the CDS views, how the architecture is structured and analytics part of it. You will also learn about, what the things that additional are helping in and how the entire set up brought in to front in.
-
In this video, you will learn about the business partner and how they are able to centrally manage data. You will also learn about what were the limitations in tradition system. Further, you will be preceded with different categories of business partner and how to create it followed by their respective configuration.
-
In this video, you will have a deeper knowledge of the configuration of a business partner, where you’ll have a customer, vendor and you will also learn how the customer gets triggered in term of the business partner. Further, you will have an understanding of how business partners work and configuration behind the contact person.
-
In this video, you will be presented with steps to determine address type, how to maintain the tax number categories in the business partner and where will it be stored. Further, you will have a detailed explanation on why we create a master data governance and how it will be implemented in an SAP S/4HANA.
-
In this video, you will learn about how credit management actually works. How it is managed by the credit control area, what are credit checks and its types? Further, you will also learn how a business partner is aligned to credit management in SAP S/4HANA set up. You will also learn the configuration of credit management.
-
In this video, you will learn about the three types of sales document: Header, Item, Schedule. You will be presented with what are the configurations behind item category, schedule category and sales document types.
-
This video is in continuation with the previous lecture on how to determine all the delivery date and confirm the quantity with the help of delivery schedules. You will be introduced to pick/pack time, i.e. shipping point followed by its configuration. Further, you will be introduced to loading time, transportation time and transit time in delivery schedule.
-
In this video, you will learn about product allocation and its configuration, how to activate product allocation and the three different set up for the product allocation. Further, you will be preceded with the configuration of product allocation object. You will also learn about the AATP system, AATP back order processing.
-
In this video, you will learn what rebate agreement is and its configuration path in ECC set up and about the 3 processes where rebate activation takes place along with their configuration. You will also learn about transaction WCOCO where you can create a conditional contract.
-
In this video, you will be presented with the configuration of rebate settlement in SAP S/4HANA followed by several steps. You will also learn the configuration of condition contract types, settlement process types, settlement doc type and many more.
-
This video is all about the questions put up by students and clearing the doubts on the SAP S/4HANA module.
-
In this video, you will learn what BRFplus is, how it is managed and who operates it. You will also learn about the types of a business rule is and how rules are represented in a system. Further, you will be preceded by how to create a business rule set up based on BRFplus followed by the configuration.
-
In this video, questions are put up by students regarding what Form templates is, how it gets assigned to the output type and the application and steps to follow the configuration. You will also learn about the combination required for a system to show the output.
-
In this video, you will learn about what was the need for SAP S/4HANA to come out with changes in sourcing and procurement. You will also learn about Ariba integration and what supply life cycle management is and its code deployment. Further, you will be preceded by how to create purchase requisitions followed by several steps along with their respective configuration.
-
In the session, you will learn about the changes that have been done in master data in the SAP S/4HANA system. You will be introduced to four types of master data and changes that took place in a business partner. Further, you will be preceded with the steps to follow partner determination.
-
In this video, you will be presented with the configuration on the procurement side required from the logistics consultant perspective. You will also learn what material type is, things that are determined through material type and its configuration. Further, you will be preceded with a detailed explanation on the quality/value updating, valuation class and many more. You will also learn about the configuration of purchase requisition, RFQ and master data set up.
-
In this video, you will learn about the purchase order set up and the different types of procurement type in the purchase order. Further, you will be preceded by the steps to follow the configuration of a purchase order from setting a tolerance limit to the release process. You will also learn the inventory base configuration as well.
-
In the session, you will learn how automatically create storage location, screen layout, etc. you will also learn about the account determination and the steps to follow the configuration, i.e. valuation class, valuation group code, valuation area, company code and many more. Further, you will have an understanding of the differences between stock transfer and transfer posting.
-
In this video, you will have a deeper knowledge of what material ledger is, why it has been not used in ECC system and what changes have been introduced in a material ledger in SAP S/4HANA. You will have a detailed explanation of three functionalities of material ledger, i.e., multiple currencies, multiple valuations and actual costing.
-
This video is a continuation of the first part where you will have a deeper understanding of benefits of using the Actual costing in an SAP S/4HANA. Further, you will be preceded by steps to customize material ledger and how splits the cost of goods.
-
In the session, you will be introduced to Material Requirements Planning (MRP), why it is required and its importance in SAP S/4HANA. You will learn about the dependent and independent demand, lot sizing and how MRP runs in the system. Further, you will be preceded with master data and three different types of MRP procedure. You will also learn the configuration of the above mentioned process.
-
In this video, you will learn how to activate MRP & planning file entries in the SAP S/4HANA system. You will also learn about the factors that influence MRP. Further, you will be preceded by a detailed explanation of what are planned order, production order and process order along with their respective configuration.
-
In the session, you will be presented with the configuration of production planning for process industries and how MRP and PPPI are integrated into a system.
-
In this video, you will have deeper knowledge of five parameters on which MRP logic works, i.e. material calculation, lot sizing, production type, scheduling & BOM explosion. You will also learn how product version has become mandatory in SAP S/4HANA and the changes that have been done in the new system.
Course/Topic 11 - SAP S/4HANA SD (Sales and Distribution) - all lectures
-
In this session, we learn about how SAP S/4HANA SD is different from SAP SD on ECC.
-
In this session, we learn about defining Company, Company Code, Sales Organization, Distribution Channel, Division, Sales Office and Sales Group.
-
In this session, we learn about defining Plant, Storage Location, Shipping Point and assignments of Organizational Units.
-
In this session, we learn about remaining assignments of Organizational Units.
-
In this session we learn assigning Company Code to Fiscal Year Variant, Chart of Accounts and Field Status Variant, Materials Management View on Accounting, Stochoistic Block Values, set Company Code Productive, Financial Management Area, Global Company Code, Cost of Sales Accounting, Taxes, Credit Control Area, Controlling Area and Profit Center.
-
In this session, we learn about Credit Segment, Company Code groups, FM account assignment derivation, Settings for Company Code, Material Ledger and Quantity and Value Updating.
-
In this session, we learn about Business Area, Valuation Grouping Code, Inventory Management, Plant Parameters and Maintenance Planning Plant.
-
In this session, we learn about different views of Material Master like Basic Data 1, Sales org1, Sales: General Plant, Purchasing, MRP 1, MRP 2, MRP 3, MRP 4 and Accounting 1.
-
In this session , we learn about creation of Material Master, Initial entry of Material Stock and Display of Material Stock.
-
In this session, we learn about General Data, Company Code Data, Sales Area Data and Customer account group.
-
In this session, we learn about creation of grouping, Partner Functions and Creation of Customer Master.
-
In this session, we learn about Access Sequence, Condition Type and Pricing Procedure.
-
In this session, we learn about Pricing Determination and creation of Condition Master.
-
In this session, we learn about various fields in Sales Document Type.
-
In this session, we learn about Inquiry, Quotation, Sales Order, Delivery, Transfer Order, PGI, Invoice, Credit Memo Request, Debit Memo Request, Rush Order, Cash Sales, Quantity Contract, Scheduling Agreement, Consignment Fill Up, Consignment Issue, Consignment Pick Up and Consignment Return.
-
Episode 16 - Item Category Type
-
In this session, we learn about Configuration of Cross Selling.
-
In this session, we learn about Configuration of Free Goods.
-
In this session, we learn about Configuration of Third Party Sales.
-
In this session, we learn about Copy Control, Product Proposal, Material Exclusion, Material Determination, Picking and Confirmation, Billing Document types, Creation of Billing Documents, Billing Methods, Billing Plan, Types of Billing Plan, Revenue Account Determination, Credit Management, Output Determination Process and Partner Determination.
-
In this session, we learn about ASAP Methodology for Implementation Project and Support Project.
Course/Topic 12 - SAP Ariba Sourcing - all lectures
-
Watch this SAP Ariba Sourcing introduction video to see how you can create and execute comprehensive sourcing events on Ariba Network.
-
This video is for SAP Ariba sourcing which help you in project templates. All projects must be created from a project template.
-
By watching this video, you will get to know about depending on the type of information you want to collect and your sourcing solution, you can create the types of events using SAP Ariba Sourcing.
-
SAP Ariba enables you to import sourcing event data from and export data to Microsoft Excel spreadsheets. This feature helps you enter a large volume of data quickly or save event information outside of SAP Ariba or to collaborate with colleagues.
-
Content provided by the supplier in the Profile Questionnaire can be graded as part of the supplier onboarding and profile approval process. Users with Supplier/Customer Manager permission can confirm automatic grades (for quantitative responses) and grade qualitative responses.
-
The goal of this video is to provide your organization and end users with a powerful tool in SAP Ariba Sourcing to evaluate supplier’s bids and improve your decision-making process to approach the best offer to award an Event.
-
In SAP Ariba solutions, the project types for “request”— such as Sourcing Request and Contract Request— provide many benefits. In this session, we’ll discuss the different request types, the template configuration, and the process from request to official project.
-
This is the overview of the auctions functionalities within the SAP-Ariba strategic sourcing tool.
Course/Topic 13 - SAP Ariba Procurement - all lectures
-
In this lecture session we learn that Procurement is the process of acquiring goods and services by purchasing, renting, or leasing. The procurement process includes preparing specifications and solicitations. The procurement process also includes evaluating bids and proposals, awarding contracts, and contract administration.
-
In this tutorial we learn about The requisition life cycle begins with a request for goods or services from someone in your organization. A requester must then enter the requisition and forward the requisition to the person or persons responsible for approving the accounting distribution and amounts. However, requisition approval is optional.
-
In this tutorial we learn about Invoice approval, also called check authorization, is a document that lists the steps and documents required before an invoice can be paid. In other words, this is the approval process that the accounting department must perform before it is allowed to cut a check for the purchase of goods.
-
In this lecture session we learn about A demand aggregation contract that was established to combine purchases of common goods and services to yield better value for money through economies of scale. In an organization where common goods and services are not consolidated, the procurers are unaware of what the others are purchasing.
-
In this lecture session we learn that Catalog is a tool for creating living style guides for digital products. It combines design documentation and assets with real, live components in one single place.
-
In this lecture session we learn about A catalog is a grouping of codes that belong together content-wise with which qualitative subjects written in text form can be encrypted in a form that can be processed automatically. You use catalogs in Warranty Processing when you enter items for a version.
-
In this lecture session we learn that Receive is defined as to take, accept, experience or welcome. An example of receiving is getting a letter in the mail. An example of receiving is someone being given a gift.
-
In this tutorial we learn about Invoice payment terms are an integral part of any bills issued by a business to its customers. These terms state the date by which the invoice is to be paid and any discounts that may apply to an early payment.
-
In this lecture session we learn that Contract compliance refers to observance of the norms and procedures outlined in a contract. Often, this involves periodic reviews of an existing contract to determine adherence to compliance mandates and protocols and check for deviations.
-
In this tutorial we learn about A document created by the magistrate describing the conditions under which the Defendant will be released from custody or held until trial. This can be related to multiple cases, but some counties require a one-to-one relationship with the initiating process.
-
In this lecture session we learn about The creation of a purchase order is the first step in a business transaction, it is issued by the buyer and authorizes a seller to provide a product or service at a specified price. The invoice is a bill issued by the seller when that product has been delivered or the service has been completed.
-
In this tutorial we learn about A Purchase Invoice is a bill you receive from your Suppliers against which you need to make the payment. Purchase Invoice is the exact opposite of your Sales Invoice. Here you accrue expenses to your Supplier. Making a Purchase Invoice is very similar to making a Purchase Order.
The main intentions of learning Bundled Course - SAP SCM are:
a) To learn the Supply Chain Management processes
b) To understand the fundamentals of Supply chain
c) To get introduced to SAP SCM Modules
d) To improve the quality of customer experience using SCM
This course provides a comprehensive understanding of SAP Supply Chain Management (SCM). Participants will explore key processes, tools, and best practices to optimize supply chain operations and enhance efficiency across the organization.
Week 1: Introduction to Supply Chain Management
a) Overview of Supply Chain Management concepts
b) Importance of SCM in business strategy
c) Key components of SAP SCM
d) Introduction to the SAP SCM architecture
Week 2: SAP SCM Fundamentals
a) Overview of key modules: SAP APO, SAP EWM, SAP TM, and SAP IBP
b) Understanding the integration of SCM with other SAP modules
c) SAP SCM architecture and landscape
d) Hands-on exercise: Navigating the SAP SCM interface
Week 3: SAP Advanced Planning and Optimization (APO)
a) Introduction to SAP APO and its components
b) Demand planning: Forecasting techniques and best practices
c) Supply network planning: Strategies for effective planning
d) Hands-on exercise: Creating a demand plan in SAP APO
Week 4: SAP Production Planning (PP)
a) Overview of Production Planning within SCM
b) Key processes: MRP (Material Requirements Planning), capacity planning
c) Integration of PP with SCM processes
d) Hands-on exercise: Executing a production planning scenario
Week 5: SAP Extended Warehouse Management (EWM)
a) Introduction to SAP EWM and its features
b) Key processes: Warehouse structure, inventory management, and order fulfillment
c) Hands-on exercise: Managing warehouse operations with SAP EWM
Week 6: SAP Transportation Management (TM)
a) Overview of SAP Transportation Management
b) Key components: Transportation planning, execution, and monitoring
c) Managing freight costs and optimizing routes
d) Hands-on exercise: Planning and executing a transportation scenario
Week 7: SAP Integrated Business Planning (IBP)
a) Introduction to SAP IBP and its capabilities
b) Key processes: Sales and operations planning, inventory optimization
c) Leveraging analytics and insights in IBP
d) Hands-on exercise: Creating a supply chain plan in SAP IBP
Week 8: Supply Chain Collaboration and Visibility
a) Importance of collaboration in supply chain management
b) Tools for enhancing visibility: SAP Cloud Platform and SAP Business Network
c) Best practices for supplier and customer collaboration
d) Hands-on exercise: Implementing a collaboration scenario
Week 9: Analytics and Reporting in SAP SCM
a) Overview of reporting tools in SAP SCM
b) Key metrics and KPIs for supply chain performance
c) Creating custom reports and dashboards
d) Hands-on exercise: Generating supply chain reports in SAP
Week 10: Capstone Project
a) Overview of capstone project objectives
b) Participants will design an integrated supply chain solution using SAP SCM
c) Presenting a complete supply chain workflow incorporating APO, EWM, TM, and IBP
d) Presenting the final project to the class
Recommended Resources:
1)Textbooks:
"SAP SCM: Applications and Modeling for Supply Chain Management" by Daniel J. H. P. R. C. P. E. H. L. K. L. J. C. M. R. M. T. G.
"Supply Chain Management with SAP ERP: Making a Case for a Process-Oriented Approach" by Mary L. Schmidt
2) Online Resources:
SAP Learning Hub, openSAP for module-specific tutorials
3)Tools:
Access to SAP SCM environment for hands-on practice
4)Assessment:
a).Weekly quizzes and assignments
b).Mid-term project focusing on a specific SCM component
c).Final capstone project showcasing an integrated supply chain solution
The SAP SCM certification exam tests the participantsproficiency in the area of Supply Chain Performance, SAP WM, SAP EWM, SAP S/4 HANA TM, EWM and Logistics to become a skilled SAP Supply Chain Consultant.
The Course completion certificate will be awarded by Uplatz upon the completion of the Bundle Course – SAP SCM training.
Below given are the Certification details of individual SAP Modules:
1)-SAP Certified Application Associate-Logistics Execution and Warehouse Management with SAP ERP 6.0 EhP6
a).Certification Level: Associate
b).Exam Name: SAP Certified Application Associate- Logistics Execution and Warehouse Management with SAP ERP 6.0 EhP6
c).Exam Code: C_TSCM66_66
d).Exam Mode: Online
e).Total Number of Questions: 80
2)-SAP Certified Application Associate-SAP Extended Warehouse Management 9.5
a).Certification Level: Associate
b).Exam Name: SAP Certified Application Associate- SAP Extended Warehouse Management 9.5
c).Exam Code: C_EWM_95
d).Exam Mode: Online
e).Total Number of Questions: 80
3)-SAP Certified Application Associate-SAP Extended Warehouse Management with S/4 HANA
a).Certification Level: Associate
b).Exam Name: SAP Certified Application Associate- SAP Extended Warehouse Management with S/4 HANA
c).Exam Code: C_S4EWM_1909
d).Exam Mode: Online
e).Total Number of Questions: 80
4)-SAP Certified Application Associate-SAP Transportation Management 9.5
a).Certification Level: Associate
b).Exam Name: SAP Certified Application Associate- SAP Transportation Management 9.5
c).Exam Code: C_TM_95
d).Exam Mode: Online
e).Total Number of Questions: 80
5)-SAP Certified Application Associate- SAP S/4 HANA Sourcing and Procurement
a).Certification Level: Associate
b).Exam Name: SAP Certified Application Associate- SAP S/4 HANA Sourcing and Procurement
c).Exam Code: C_TS450_1709
d).Exam Mode: Online
The SAP SCM Consultants have a good job future. The SCM consultants is one of the most-sought after professionals because of its scope and demand in industries and enterprises. The Supply Chain field is so vast, there are many speciality areas within supply chain and there are different SAP Products and applications which cater each of these areas.
The SAP SCM Consultant draw an average salary of $157,563. The other job-titles are
a).SAP SCM Consultant
b).SAP Senior SCM consultant
c).SAP S4 HANA TM Consultant
d).SAP S4 HANA EWMAssociate
e).SAP Functional Consultant
f).SAP EWM Consultant
g).SAP EWM Functional Consultant
h).SAP Consultant
The SAP SCM Suite has very good demand in the market and promises a rewarding career.
More about all SAP SCM modules:
1.SAP Advanced Planner and Optimizer (APO)
SAP APO (Advanced Planning and Optimization) is a set of applications for managing supply chains of companies. It is one of the key components of SAP SCM (Supply Chain Management) solution. Besides SAP APO, SAP SCM includes components such as SAP Transportation Management (TM), SAP Extended Warehouse Management (EWM), and others.SAP APO is a robust tool designed to enable your organization to achieve the inconsistency between aspects or parts of a whole goal of improving customer service while reducing costs. By enabling visibility for and access to all stakeholders involved in generating a single, organization wide demand plan, the demand planning capability of SAP APO projects the needs of your organization’s customers.
2.SAP Materials Management (MM)
SAP MM is an important module of the SAP ERP CC. It offers warehouse and inventory management facilities. These activities are important to any company. This is because materials management is a key function needed to sustain their supply chain. The main aim of this software is to ensure that the supply chain has no gaps. Plus, the software assists employees to make sure that the materials are available in appropriate quantities.
The Materials Management (MM) module is the business process area that handles daily activities of a business such as Procurement, Inventory Management, Materials Requirement Planning, Master data (Material and Vendor), Material Valuation, Vendor Evaluation, Invoice Verification and so on.
3.SAP Warehouse Management (WM)
SAP WM aims to control the movement and storage of materials within a warehouse with greater traceability. In SAP WM, material goods movement and storage is managed in efficient way.
When you implement the Warehouse Management System (WMS) in a plant, you define the Individual warehouses as storage types within a warehouse complex and group them together under a warehouse number. As a rule, it is not necessary to define several storage locations for a plant since you assign the WMS warehouse number to a storage location from Inventory Management (IM).
4.SAP Extended Warehouse Management (EWM)
SAP Extended Warehouse Management (SAP EWM) forms part of SAP Supply Chain Management (SAP SCM) and provides end-to-end support for supply chain processes.(SAP Extended Warehouse Management) SAP EWM brings together maximum functionality and comprehensive process support for all types of warehouses, and is thus one of the most powerful software suites for warehouse management and control worldwide.
The principal components within SAP EWM (SAP Extended Warehouse Management) include warehouse management (SAP Extended Warehouse Management) and material flow control (SAP Material Flow System). SAP EWM (SAP Extended Warehouse Management) provides comprehensive functionality for warehouse processes, for which companies were previously forced to use specialised, standalone niche applications. An example of this functionality is offered by new distribution procedures, with which you can significantly reduce inventory costs while improving service quality.
5.SAP S/4HANA MM, Sourcing & Procurement
The SAP MM (S/4HANA for Sourcing) certification course verifies that the candidate possesses knowledge and skills in the area of SAP Procurement to satisfy the requirements for the consultant profile so that the candidate can implement this knowledge practically in projects.On completion of course the candidate will have good overall understanding of fundamentals of SAP MM (S/4HANA Sourcing) and can implement this knowledge practically in their projects.
The user experience of operational purchasing within SAP S/4HANA is fully supported by SAP Fiori apps (see picture below), so that everyone can independently search for and request goods or services or even order directly. SAP S/4HANA also supports cross catalog search, whereby all catalogs can be searched simultaneously. Catalog content can be loaded directly into SAP S/4HANA. SAP S/4HANA also contains the Central Procurement functionality, whereby SAP S/4HANA can be centrally positioned above multiple back-end systems. This actually replaces the SAP SRM positioning, where SAP SRM provides this functionality.
6.SAP S/4HANA EWM
SAP EWM (Extended Warehouse Management) is the NEW functionality that SAP offers for the management of stock in specific bins inside the new release S/4 HANA.It is a functionality every logistics consultant or practitioner should be aware of it.
SAP EWM allows to subdivide SAP Inventory Management Storage Locations in different specific bins and at the same time it offers all related functionality for the placement in Warehouses (Putaway processes) and the removal from them (Stock Removal processes).
The EWM landscape by exploring key warehouse functionality, from inbound, outbound, and internal processing to advanced features for cross docking, yard management, and more. Preview integration and implementation get your project started!
7.SAP S/4HANA Transportation Management (TM)
SAP Transportation Management (SAP TM) as a component of the Supply Chain Execution Platform (SAP SCE) is currently the most advanced transport management software solution on the market. It helps companies to handle goods traffic efficiently, quickly, and accurately. SAP TM addresses the requirements of logistics service providers, carriers, and shippers. SAP Transportation Management supports all transport processes, from planning, consolidation and optimization up to execution and invoicing in an cross-industry, holistic solution.
8.SAP S/4HANA Logistics
SAP Simple Logistics is also called SAP S/4 HANA Enterprise Management. It consists of all the key modules under SAP ERP Business Suite – Material Management, Supply Chain, Demand Planning, Sourcing and Procurement, Contract Management, and Manufacturing.
SAP S/4HANA logistics on HANA 1909 is the latest iteration of the HANA in-memory technology. A technology that has already improved analytics and reporting significantly. Until now, HANA has only been available as an “add-on” to existing business suites. SAP S/4HANA Logistics uses the data processing ability of S/4HANA to provide simpler, faster and more efficient approaches to logistics and supply chain problems. The trainees will gain knowledge and hands-on experience in one of the most sought-after exceptional features of SAP S/4HANA Logistics 1909.
9.SAP Ariba Sourcing
With the SAP Ariba Strategic Sourcing solution portfolio, you can manage your entire sourcing, contracting, and spend analysis processes for all types of spend – direct and indirect materials as well as services – all in one place.
SAP Ariba Start Sourcing is a free, intuitive, web based RFX management tool that empowers you to create, execute, and manage sourcing events right from your desktop. This cloud-based software-as-a-service (SaaS) technology is delivered on demand and requires no subscription fee.
10.SAP Ariba Procurement
In todays globalized, digitalized economy, cost pressure is ramping up exponentially – especially for SMEs. Procurement is increasingly becoming the determining factor in generating higher margins and boosting companies’ competitiveness. What used to be simply a matter of procuring the right components is increasingly turning into a need to cultivate lasting business relationships.
SAP Ariba Network is the backbone of SAP Ariba that facilitates the interaction between purchasing departments or regular buyers and suppliers. It transcends the local firewall that protects your local ERP systems and IT infrastructure. It allows you to communicate with your suppliers in the cloud through a secure web interface.
Q1.Define the Supply Chain Management Process?
Ans-The SAP Supply Chain Management is a key module in SAP which is eful in controlling production, planning, business forecasting and demand planning.
Q2. What is the use for SCM?
Ans-The SCM is used to help an organization or enterprise to manage their supply chain process in a dynamic environment.
Q3.Mention the different stake holders in supply chain?
Ans-The SAP SCM suite process helps suppliers, customers, manufactures, business partners and retailers to get connected with each other in order to manage supply chain process.
Q4.Name the different applications that are used as part of supply chain process?
Ans-The primary applications are SAP General areas, SAP Supply Network Collaboration, SNC, SAP Extended Warehouse management, Advanced Planning and Optimization, Forecasting and replenishment and SAP Transportation management.
Q5. What are the different components under SAP SCM Process?
Ans-The components are:
a).Forecasting
b).Supply Network Planning
c).Production Planning and Detailed Scheduling
Q6.How to perform Forecasting?
Ans-The demand planning and forecasting can be performed by linking to customer relationship management or CRM to fetch data related to customer campaigns
Q7.Define the use of Supply Network Planning?
Ans-The Supply Network Planning functionality allows to view the organization as a network of locations and to check stock projections and stock keeping criteria.
Q8.What is the functionality of Production planning and detailed scheduling?
Ans-This functionality checks the dependent requirements from locations within the supply network. This option is linked with material requirement planning in production planning which determines the inbound material to complete a production order.
Q9.Define Bonded Warehouse?
Ans-The Bonded Warehouse refers to some dedicated portion of a facility where the imported products or goods are stored before the custom taxes are paid.
Q10.Mention the types of stocks?
Ans-The stock types are:
a).Valuated stock
b).Non-valuated stock
c).Special Stock
Q11.What are the document types which enables cost distribution in SAP TM?
Ans-The document types are:
a) Freight Order
b) Freight Settlement Document
Q12.What are the options used to create freight bookings?
Ans-The options are:
a) A report based on a schedule
b) The freight order user interface
Q13.Define SAP EWM?
Ans-SAP EWM product is useful for processing goods movements and inventory management in a warehouse.
Q14.Define Storage Bin in EWM?
Ans-The physical location of the storage area represents the storage bin where the products are stored in the warehouse.
Q15.List down the different warehouse process types in SAP EWM system?
Ans-The processes are:
a).Stock Removal
b).Putaway
c).Internal Movement
d).Physical Inventory
e).Cross Line Putaway
f).Goods Issue Posting
Significance of SAP SCM
1.Enhanced Visibility: SAP SCM provides real-time visibility into various stages of the supply chain, allowing organizations to monitor inventory levels, production progress, transportation status, and order fulfillment.
2.Improved Efficiency: By automating and optimizing supply chain processes, organizations can reduce lead times, lower costs, minimize excess inventory, and enhance overall operational efficiency.
3.Effective Demand Forecasting: Accurate demand forecasts generated by SAP SCM help organizations make informed decisions about production, inventory management, and resource allocation.
4.Optimized Production: With SAP SCM, production schedules can be adjusted based on real-time demand fluctuations and resource availability, leading to optimized production processes.
5.Responsive Planning: SAP SCM enables organizations to respond swiftly to changes in demand or supply, helping them adapt to market dynamics and capitalize on emerging opportunities.
6.Collaboration: The collaborative features of SAP SCM allow organizations to establish better communication and coordination with suppliers, ensuring timely deliveries and reducing supply chain disruptions.
7.Strategic Decision-making: The insights and analytics provided by SAP SCM enable organizations to make data-driven decisions that align with their long-term strategic goals.
In the complex and interconnected world of supply chain management, SAP SCM serves as a powerful tool to orchestrate and optimize processes. By providing end-to-end visibility, improving efficiency, and enabling collaboration, SAP SCM empowers organizations to meet customer demands, reduce costs, and stay competitive in a rapidly evolving business landscape.