SAP QM (Quality Management)
Learn about quality management actions such as quality planning, quality assurance, and quality control, product lifecycle, after production etc.Preview SAP QM (Quality Management) course
View Course Curriculum Price Match Guarantee Full Lifetime Access Access on any Device Technical Support Secure Checkout   Course Completion Certificate64% Started a new career BUY THIS COURSE (
USD 17 USD 41 )-
34% Got a pay increase and promotion
Students also bought -
-
- SAP PM (Plant Maintenance)
- 10 Hours
- USD 17
- 1780 Learners
-
- SAP MM (Materials Management)
- 30 Hours
- USD 17
- 2423 Learners
-
- Bundle Course - SAP Logistics (PM - PP - MM - QM - WM - SD - S4HANA Logistics)
- 200 Hours
- USD 31
- 1692 Learners
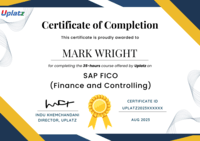
SAP QM (Quality Management) module is an integral part of logistics function and is used to perform quality management actions such as quality planning, quality assurance, and quality control at various stages of the product lifecycle such as incoming material stage, in-process manufacturing process stage, and after production.
Quality management is important to the warehouse, inspecting incoming material as it arrives at the facility, for manufacturing operations where the quality of in-process items are checked during the manufacturing process, and finished goods are inspected before they reach the warehouse. All these processes are handled in a very streamlined manner with SAP QM module.
SAP QM consists of tools for several interrelated activities:
1) Quality Planning (QM-PT) - lets you set up and manage quality inspection plans that define what goods are inspected, how the inspections take place, the characteristics of the goods to be inspected and the type of equipment used to perform the inspections.
2) Quality Inspection (QM-IM) - allows you to determine if a product meets the defined quality requirements and to record the results of inspections. QM-IM uses inspection specifications that are defined in Quality Planning.
3) Quality Certificates (QM-CA) - allows you to certify that goods have met defined quality requirements.
SAP QM is a part of the SAP R/3 system and is integrated with other SAP modules like SAP MM, PP, PM.
This SAP QM training by Uplatz will provide you with extensive knowledge of SAP QM module so that you get practical skills to become a successful SAP QM consultant. You will also get prepared to apply for SAP QM jobs.
Course/Topic 1 - SAP QM Introduction - all lectures
-
In this first video on the SAP QM course, you will get a brief introduction to SAP QM, starting with Master Data in QM, Organizational Overview, Material Master – Activation of QM View, Master Inspection Characteristics (MIC), Sampling Procedure, Codes, and Code Groups, Inspection Method and others.
Course/Topic 2 - Material Master and Sampling Procedure - all lectures
-
In this video, you will be working with the Master Data starting with creating Material Master which will be shown in a step-by-step procedure by the trainer in the SAP system. Further, you will be learning about the next Master Data which is the Sampling Procedure and the same will be shown in the SAP system.
Course/Topic 3 - MIC Sampling Scheme - Sampling Drawing Procedure - all lecutures
-
In this session, you will be learning about the concept of Master Inspection Characteristics which is commonly abbreviated as MIC. Starting with an understanding of the concept of MIC, creating MIC in the SAP system, and creating the Inspection Plan.
Course/Topic 4 - Code Group and Selected Set and Catalog - all lectures
-
In this video, you will learn about the Code Group, Selected Set, and the Catalog. You will get an introduction to each one of these and proceeding further, you will learn how to create a Code Group, Selected Set, and Catalog in the SAP system.
Course/Topic 5 - Catalog Profile and Quality Inspection Method Results - all lectures
-
In this session, you will learn about the Catalog Profile, how to create a Catalog Profile, Inspection Method, creating Inspection Method and the complete work process of these will be shown in the SAP system.
Course/Topic 6 - Results Recording and Usage Decision and Material Specification - all lectures
-
In this session, you will learn about the Results Recording in SAP QM which will be shown in the SAP system. Along with this, you will also learn about the Usage Decision and Stock Posting. Moreover, you will also learn about the Monitor Stock Overview, Monitor Display Inspection Lot, Material Specification, and the steps involved in creating a Material Specification.
Course/Topic 7 - QM in Procurement and Stock Transfer Inspection - all lectures
-
In this video, you will learn about Quality Management in Procurement with and without the PO process and the various configuration steps involved in it such as creating a Material Master and maintaining the Inspection Type, creating and maintaining MICs, Inspection Plan along with the Sampling Procedure and others. Further, you will also learn about the Stock Transfer procedure in SAP Quality Management Inventory Management and from Plant to Pant.
Course/Topic 8 - Quality Info Record and Controls in Procurement - all lectures
-
In this video, you will be learning about Controls in Procurement, starting with creating a Material Master and maintaining the settings in the QM view. Proceeding further, you will be creating a PO, a brief explanation on Quality Info Records and finally, all these steps will be shown by the trainer in the SAP system.
Course/Topic 9 - Target QM System and Certified Vendor and Qualified Vendor - all lectures
-
In this video, you will be learning about Target QM System, starting with maintaining Target QM System in Material Master, Quality Info Record, creating PO, GR, monitoring Stock Overview, and others. Proceeding further, you will be getting some in-depth knowledge on Certified and Qualified Vendors related to the work of SAP Quality Management.
Course/Topic 10 - Automatic Batch Valuation and Recurring Inspection in QM - all lectures
-
In this session, you will learn about the Quality Management with Batches and Automatic Batch Valuation with QM. Starting with maintaining results recording under MIC, characteristics, and class under MM and these will be shown in the SAP system. You will be learning about the different configuration steps like creating MIC, characteristics, class, Material Master, Manual Inspection Lot and others.
Course/Topic 11 - Quality Certificates in QM - all lectures
-
In this video, you will learn about Quality Certificates, starting with a brief introduction to Quality Certificate and the steps involved in performing Quality Certificate. You will also be learning about the Incoming Quality Certificate and its work process will be shown by the trainer in the system.
-
In this video, you will be learning about the complete work process of the Outgoing Quality Certificate in the SAP system. You will also be learning about the two modules integration which is Inprocess Inspection and GR Inspection and a detailed understanding of each of these.
Course/Topic 12 - QM in Production - all lectures
-
This is the first part of the session where you will learn about the complete work process of QM in Production along with the Process for Quantity Based Inspection and Time Based Inspection and these will be shown by the trainer in the SAP system.
-
In this video, you will learn about the Free Inspection and the steps involved in it to work in the SAP system like maintain settings in Routing, creating Production Order, Releasing Production Order and Performing QE51N for Results Recording. Along with this, you will also be learning about the GR Inspection after Production Order.
Course/Topic 13 - QM in SD - all lectures
-
In this session, you will be learning about the three business scenarios where the QM in SD takes place. You will be getting a detailed step-by step explanation of each one of these along with its work process in the SAP system.
-
This is the second part of the video where you will learn some more in-depth concepts related to QM in SD like Inspection for Delivery to customer w/o order before and after delivery and the work procedure of it in the SAP system.
Course/Topic 14 - Inspection with Physical Sample and Quality Notification - all lectures
-
In this session, you will learn about the three types of Inspection with physical samples which are Primary Samples, Pooled Samples and Reserved Samples and a detailed explanation of each one these in the system.
Course/Topic 15 - Stability Studies and Control Charts in QM - all lectures
-
In this video, you will get an overview on Stability Studies in QM with a detailed explanation using a real-life example. Further, you will be learning about the Process Flow for Stability Studies.
Course/Topic 16 - QM in PM - all lectures
-
In this video, you will learn about the Calibration Inspection Process and the different configuration steps involved in it to work on the SAP system.
Course/Topic 17 - Config Settings in QM - all lectures
-
In this last video of the SAP QM course, you will learn about the different configuration settings of SAP Quality Management and these settings will be shown by the trainer in the SAP system.
• Complete Understanding of SAP Quality Management module.
• SAP QM - quality management Training reference
• All modules of SAP Quality management
• Quality Inspection Training
• Quality Notifications
• Certificate Profiles
· Basic SAP GUI Navigation
· Integration of Quality Management in the supply chain – process
· Insight into QM Functions
· Potential for Introducing Quality Management in Companies
· Quality Planning and Inspection
· Managing QM-specific Basic Data
· Inspection Planning
· Quality Inspection Process
· Quality notification and SAP Business Workflow
· Quality Management in Logistics
· Quality Management in Discreet Manufacturing
· Quality Management in the Process Industry
· Quality Management in Sales & Distribution/Quality Certificates
This SAP QM training course is designed for clearing the SAP Certified Application Associate - Quality Management with SAP ERP 6.0 EhP5 exam.
In the SAP QM course the participants learn about the SAP QM ERP module. In the SAP QM course, the participants will learn about quality management contribution in business process such as procurement, production. This seems to be an essential learning for all SAP QM module users.
SAP QM Certification is an important benchmark in becoming a SAP QM Associate as the exam topic covers quality control, manufacturing, inspection and sales service. SAP QM tutorial helps the participants to learn about Quality management process and thus attaining a unique SAP certification. SAP QM course offers complete information about the organizational elements used in QM thus making the participant a skilled SAP QM Consultant.
Uplatz online training helps the participants to successfully pass the SAP QM Certification exam conducted by SAP. Uplatz provides appropriate teaching and expertise training to equip the participants with skills that they can use to implement the learnt concepts in an organization.
Course Completion Certificate will be awarded by Uplatz upon the completion of the SAP QM course.
The SAP QM certification exam verifies that the participants possess basic knowledge and can prove their skills in the area of SAP Quality Management. This SAP QM certification exam validates that the participant has an overall understanding about this consultant profile, and able to implement the knowledge practically in projects.
Below given are the certification details of SAP Certified Application Associate - Quality Management with SAP ERP 6.0 EhP5 exam:
· Certification Level: Associate
· Exam Name: SAP Certified Application Associate- Quality Management with SAP ERP 6.0 EhP5
· Exam Code: C_TPLM40_65
· Exam Mode: Online
· Total Number of Questions: 80
· Pass Score: 55%
· Time Duration: 180 Minutes
· Exam fee: $550
The SAP QM Consultant draws an average salary of $114,780 per year depending on the knowledge and hands-on experience. The SAP QM Consultant job roles are in high demand and make a rewarding career.
The SAP QM Consultants are recognized across the globe. The increased usage of the Quality management in many companies help the participants to find a job opportunity easily.
Leading companies hire SAP QM Consultants considering the efficiency to meet the business requirements for the purpose of quality management. The Learners earn most beneficial SAP QM certification through our expert training and course curriculum. Being SAP QM certified is definitely valuable credential and adds value to every organization.
The SAP QM certification is targeted to those who are beginners, managers , PLM and business consulting background and excel in Quality management area.
The following are the job titles:
· SAP QM Associate
· SAP QM Consultant
· SAP QM Developer
· SAP QM Functional Consultant
· SAP Quality Inspection Consultant
The SAP QM certification training program helps the participants to get placed in reputed MNCs and organizations.
Q.1. What is the use of SAP Quality Management system?
SAP Quality Management is part of SAP R/3 system and is integrated with other SAP modules like SAP Material Management MM, Production Planning PP and Plant Maintenance. QM is integral part of logistic management and is used to perform quality functions at incoming material, in process manufacturing process and raw material as well in the facility.
Q.2. What are the different functions in SAP Quality Management?
- Quality Planning
- Quality Notifications
- Quality Inspection
Quality planning allows to plan the inspection of goods from the vendor, raw material, work in process and final product.
Quality notification includes the defect identification and steps to be taken by quality department.
Q.3. What is an Inspection plan in QM process?
Inspection plan definition is an important part of the QM planning process. The inspection plan contains the number of characteristics of the item are to be inspected and list of tests to be performed for performing the inspection.
Q.4. What comes under Quality assurance process?
Under Quality assurance, it includes the quality inspection.
A Quality inspection involves someone from the quality department inspects an item as per defined points in inspection plan. You perform the inspection based on one or more inspection lots, where a lot is a request to inspect a specific item.
In SAP system, you can create Inspection lot either manually by a user or automatically in the system.
Q.5. What comes under Quality control process?
Under quality control, you have quality notifications, standard reports and Quality notification system. What actions has to be taken as per defect finding.
Q.6. What is Quality notification?
The quality notification process includes recording problem that is either identified by a customer for a product manufactured in an organization, or in a company against the product of a supplier/vendor.
Quality notification can be raised internally to raise an issue that has arisen on the production line. A quality notification can be assigned to an existing order or you can also create a new order as per the quality notification.
Q.7. What are different standard reports in SAP Quality Management System?
You can create reports in QM system to check how many times a product has been identified with a defect and improvement areas that your company has to implement. There are number of reports that can be generated in QM −
Material Defects report
It can be used to check the number of times an item has been identified with a defect status.
Vendor Defect report
This report is used to show the number of defected material supplied by a vendor.
This can be checked by examining the inspection lots for goods receipts, a quality department can highlight vendors who are material which are failing in inspection.
Customer Defect report
This report is used to show the defects that were found on inspections for outbound deliveries. This helps organization to improve the quality of goods delivered and hence raise the customer satisfaction.
Q.8. Which all modules SAP quality Management QM process is integrated with?
- SAP Material Management
- SAP Production Planning
- SAP Sales and Distribution
- SAP Controlling
Q.9. What activities of SAP Material Management are integrated with Quality Management process?
· You manage the quality details for materials, vendors and suppliers.
· You manage the releases for vendors and manufacturers and also monitor QM systems for suppliers.
· You manage the release status of delivery from vendor.
· You can maintain quality agreements and RFP details when you request for a quotations and purchase orders is raised for vendors.
· You can manage quality certificates for vendors.
· Using SAP QM process, you can also initiate an inspection at supplier site before there is delivery due from the supplier.
Q.10. What activities of SAP Sales and Distribution are integrated with Quality Management process?
You can integrate SAP QM with Sales and Distribution to perform the following activities −
You can manage quality information related to customer for sales and distribution process.
In SAP QM system, you can initiate an inspection when a delivery is created against a purchase order.
You can manage quality in sales & distribution by performing quality notifications and RCA’s and by processing customer complaints to improve customer satisfaction.
What activities of Production Planning is integrated with Quality Management process?
· You can integrate SAP QM with PP to perform the inspection planning and work scheduling in SAP system.
· As part of SAP quality management process, you handle inspection characteristics and also define characteristics for the operation.
· You can manage quality inspections for manufacturing orders.
· Using SAP QM, you can set up the final inspection from the goods receipt after production process is complete.
· You can use QM process to manage partial lots of a material during production which are different in quality.
· You can confirm the quality information as per manufacturing orders.
· Using SAP QM, you can monitor the production quality with the help of control charts and reports in Production planning.
Q.11. What activities of Controlling is integrated with Quality Management process?
You can integrate SAP QM with controlling process to manage the costs for defect control and non-confirmative costs in production process.
Q.12. What are Quantitative specifications under Master Inspection charactertics?
You can directly get the results for quantitative specifications from inspection while doing result recording. You can set limits like minimum and maximum value for each parameter at master level. You can also attach the inspection method to inspection specification level.
Q.13. What are Qualitative specifications under Master Inspection charactertics?
These specifications can take values like true/false or OK/Not OK.
Q.14. How do you create an inspection method? An Inspection method can be created in one plant can be used in other plant?
You can use inspection method to perform the inspection. An inspection method can be assigned to master inspection charactertics or directly to an inspection charactertics in an inspection plan.
An Inspection method can be created in one plant same method can be used in other plant.
Creating an Inspection method
To create an inspection method, use T-code: QS31.
Q.15. What do you understand by Sampling Procedure?
Sampling procedure in QM is used to determine the size of inspection lot to be used in inspection plan under Quality planning. You can define a sampling procedure as fixed sample, percentage or other sample.
Q.16. What is a Sampling scheme?
A collection of sampling plans. You use a sampling scheme if you want to −
Determine the sample size on the basis of the lot size, inspection severity, or combination of inspection severity and AQL (actual quality level)
Store how a decision is made to accept or reject a characteristic.
Determine the number of physical samples, based on the lot size, or the number of containers in an inspection lot in sample management.
Q.17. What is the use of Sampling Type?
The sampling type defines how a sample is calculated (for example, fixed sample, 100% inspection, use sampling scheme, percentage sample). Together with the valuation mode, the sampling type defines the parameters for sample determination.
Using the sampling type, the system proposes a list of rules for sample determination. If there is only one rule available, this is automatically chosen.
Q.18. What is Valuation mode in Sampling Procedure?
The valuation mode defines the rules for accepting or rejecting a characteristic or sample. The sampling type and the valuation mode specify which parameters the system uses to determine a sample size.
Q.19. How do you set Inspection point in an Inspection lot?
If you want to use inspection points in the sampling procedure, you need to set an indicator for the corresponding application area. This indicator specifies how many inspection points are to be created for each inspection lot.
Q.20. What is the use of Quality Control Chart type? What does it specify?
If you want to use quality control charts in a sampling procedure, you must enter a quality control chart type. The control chart type specifies −
- The characteristics for which the control chart is suited
- The control variables a chart contains
- How the control limits are calculated
Q.21. Where do you use Sampling Procedures?
Sampling procedures can be referenced in task lists, material specifications and in the inspection setup. The where-used list displays the task lists, material specifications and inspection setup, in which a sampling procedure is used.
Q.22. What do you understand by Actual Quality Level value AQL?
Maximum fraction of nonconforming units (as a percentage) or maximum number of defects per 100 units permitted for a lot to be accepted. The AQL (Acceptable Quality Level) is the quality level that represents the upper limit of a satisfactory average quality level for an acceptance sampling inspection.
Q.23. What do you define in an Inspection plan?
· Materials to be inspected.
· How the inspection of materials need to be taken place.
· What characteristics to be inspected, work center and inspection specifications.
· In the inspection plan, you have to define the sequence of inspection steps to be performed and the range of specifications as per master inspection characteristics MIC, sampling procedure to calculate the sample size for inspection, inspection method, etc.
Q.24. How do you manage defects in the material supplied by vendor/supplier?
Quality info records are used to manage the supplier relation in an organization. When there is continuous defect in the material supplied by a vendor, you can use quality info records to block a vendor.
When you create a purchase order, SAP system performs a check to find if a Quality info record is required and is available for combination of material and vendor.
Quality information record has to be maintained when you use the source inspection functionality that means a material has to undergo an inspection prior to the material reaches the plant for Goods Receipt.
You can set under Quality Info record that inspection is required when it is procured from vendor A and is not required if you procure from Vendor B.
Q.25. What are different valuation parameters, and how sampling plan depend on valuation parameter?
You can create sampling schemes −
· For attributive inspections
· For variable inspections based on the s-method
· Without valuation parameters, if you use the sampling scheme in a sample-drawing procedure or in a sampling procedure that calls for a sample calculation without a task list
Depending on the valuation parameter used, the sampling plan consists of −
- The sample size, acceptance number, and rejection number for attributive inspections.
- The sample size and K-factor for variable inspections.
- The sample size if without valuation parameters was specified.
Q.26. What do you understand by lot inspection?
In SAP system, you can perform the incoming inspection for different material like raw material inspection, in progress material inspection or final goods inspection. Good receipt is generated as part of purchasing or against a scheduling agreement.
For each good receipt, SAP system creates a one inspection lot which contains details- vendor, date or purchase, etc.
Q.27. What is result recording in QM process?
You can do the result recording for the inspection lot created at the time of Goods Receipt.
To perform the Result recording, go to T-code: QA32
What is usage decision again Inspection lot?
Usage decision is used to decide whether you want to accept or reject the goods in the inspection lot based on the results of the inspection. As per inspection results the process is marked as completed.
Q.28. Explain Quality Management specific data that you can maintain in material master to control the Inspection Plan?
To control QM activities, you can, for example, define the following −
- Procurement data
- Procurement control key
- Certificate type
- Requirements for the vendor's QM system
- Technical delivery terms
Display inspection setup −
- Inspection type
- Use of a task list or material specification
- Results recording for characteristics
- Quality score procedure
- Sample determination
Q.29. How do you activate/deactivate Inspection type?
Go to Logistics → Quality management → Quality planning → Logistics master data → Material → Inspection setup.
Choose "Activate insp. type" or "Deactivate insp. Type.
Is it possible to run the quality process for intermediate or finished product during the production process in SAP system?
Yes, Example: Inspection in each shift, etc.
Q.30. What is the inspection type for in process Inspection?
The in process inspection has a reference to a production order in SAP system. You generate an Inspection lot at the time of production order release and inspection type for in-process inspection is 03 in the system. When there is a production order release, inspection lot will be automatically created in the system.
Q.31. When the final inspection is performed in QM process?
You perform final inspection of goods after production goods receipt in SAP system. Inspection lot is created after goods receipt for a production order.
Q.32. What is the inspection type for final inspection?
Inspection lot type is 4 for final inspection.
Q.33. What is the difference between Inspection Method and Inspection Plan?
Inspection plan in SAP is normally a task list based high level object describing details about what characteristics must be tested in order to ensure the quality of the product.
Inspection method is detailed info describing how to carry out inspection. It is a separate object and can be assigned to either characteristic or in the plan directly.
Q.34. What is the difference between Good Receipts Inspection and Source Inspection?
Goods Receipt Inspection −
- Performed after receiving the goods
- Performed at receivers/customers place
- Goods receipt for purchase order triggers the inspection lot creation
- Inspection lot is created after receiving the goods
Source Inspection −
· Performed before receiving the goods
· Performed generally at suppliers place with customers participation
· Quality info record triggers the inspection lot creation. To trigger the lot open purchase order required for the Material, Plant and vendor combination.
· Inspection lot created before receiving the goods based on the lead time in Quality Info record. There is also option to create inspection lot after goods receipt.
Q.35. Explain the different steps that are involved in Final inspection process?
Final inspection process consists of the following steps −
- Creation and Confirmation of Production order
- Listing Inspection lot
- Attaching and releasing inspection lot
- Sampling
- Result recording
- Usage decision
- Posting the stock
Q.36. What do you understand by defect recording in Quality Management process?
In SAP QM, you can capture different types of record which are identified at the time of inspection. SAP Quality notification can be used to analyze the defects identified and perform root cause analysis.
Q.37. What are the different types of defect that can be processed under defect recording?
Complaints filed by customers
This includes the defects identified in goods that are delivered to customers. You can use standard SAP Quality notification Q1 to record customer complaint and take action against problem reported by customer.
Complaints identified in vendor delivered goods
This includes the defect identified with quality of goods delivered from supplier/vendor. You use standard SAP QM notification type Q2 to record a complaint against vendor and take action for the incoming material.
Internal Defects
This includes recording internal problems which are identified at the time of in process quality inspection. You use standard SAP QM notification type Q3 to deal with problems identified in goods manufactured in a company.
Q.38. What is Quality Notification?
Quality notification you can record different type of problems occurred due to poor quality of goods. Quality notifications can be created for the following internal and external problems −
- Defect Analysis
- Customer Complaint
- Complaint against vendor
Q.39. How do you get Inspection lot certificates?
Use QC21- Quality Certificate
Q.40. What are the different partner functions in SAP MM module?
- Ordering Address OA
- Vendor VA
- Invoicing Party PI
Q.41. How many Quality Principles are there? Could you name few?
Eight
- Customer Focus
- Leadership
- Process Approach
- Involvement of People
- System Approach to Management
- Continual Improvement
- Factual approach to decision making
- Mutually beneficial supplier relationship
Q.42. Explain difference between Requirement class and Requirement type?
Requirement type and requirement class are assign with planning strategy. Requirement type is only description but it is contend of requirement classes they control the creation and execution of PIR, Sale Order & Stock consumption.
Q.43. What are the advantages of using SAP QM process?
· SAP Quality management integration with other modules is one of the key aspect of quality management. You can implement the quality process in Material Management, Production planning and other SAP modules.
· You can access to data maintained in the system related to customer, vendor and supplier master.
· Using SAP QM, a standardize process can be implemented.
· SAP Quality management process helps you to incorporate the improvement process - by monitoring the processes, defect identification and quality notifications.
· You can perform automation of information flow by which inspection lot gets created automatically when you release the production order or goods receipt.
· Using SAP quality management process, you can perform the quality compliance of raw materials when it is first delivered by vendors/suppliers and in process manufacturing and also after the production process is completed.
· SAP QM also responsible to perform the compliance with customer’s quality specifications you ship the goods to customer as per Purchase order.
Q.44. What is ISO standards for Quality Management?
The ISO 9000 family of quality management systems standards is designed to help organizations ensure that they meet the needs of customers and other stakeholders while meeting statutory and regulatory requirements related to a product.
Q.45. What is difference between vendor defect report and customer defect report?
Vendor Defect report
This report is used to show the number of defected material supplied by a vendor.
This can be checked by examining the inspection lots for goods receipts, a quality department can highlight vendors who are material which are failing in inspection.
Customer Defect report
This report is used to show the defects that were found on inspections for outbound deliveries. This helps organization to improve the quality of goods delivered and hence raise the customer satisfaction.
Q.46. What are different search criteria you can use in Quality Management system?
- Material
- Inspection lot creation date
- Batch
- Vendor
- Inspection dates
- Plant
- Inspection type
Q.47. Name few common tables and their description in QM system?
- QPAM Inspection catalog selected sets
- QPMK Inspection characteristic master
- QPMT Master Inspection Characteristics Texts
- QPMZ Master Inspection charactertics MIC
- QMAT Inspection type for material parameters
- QMHU shows QM link in Inspection lot and handling unit Item
- QMTB Inspection method master record
- QMTT Inspection Method texts
- QPAC Inspection catalog codes