SAP PM (Plant Maintenance)
Become SAP PM Consultant with mastery over implementation & configuration of SAP PM module. Manage end-to-end cost & maintenance of Plant & Machinery.Preview SAP PM (Plant Maintenance) course
View Course Curriculum Price Match Guarantee Full Lifetime Access Access on any Device Technical Support Secure Checkout   Course Completion Certificate85% Started a new career BUY THIS COURSE (
USD 17 USD 41 )-
82% Got a pay increase and promotion
Students also bought -
-
- SAP MM (Materials Management)
- 30 Hours
- USD 17
- 2423 Learners
-
- SAP SD (Sales and Distribution)
- 25 Hours
- USD 17
- 195 Learners
-
- SAP FICO (Finance and Controlling)
- 30 Hours
- USD 17
- 5666 Learners
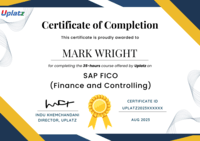
SAP PM (Plant Maintenance) is an SAP module that helps to manage all factory maintenance activities such as inspection, notifications, corrective and preventive maintenance, repairs, and other measures to maintain an ideal technical system.
SAP PM is the application component that provides an extensive software solution for all maintenance activities that are performed within a company, fully incorporating the data and functions of all maintenance procedures performed within a company.
The SAP Plant Maintenance (SAP PM) application segment enables an organization with a mechanism for all maintenance operations to be undertaken. Both maintenance tasks are closely intertwined, and thus this component is tightly integrated with other modules-Production Planning, Inventory Management, Sales, and Distribution. Utilizing SAP PM, you can execute automated improvements and make maintenance demands smoother for your business. It helps you report concerns in the SAP system, coordinate material and equipment operations, and monitor and address changes. You can recognize, track, resolve challenges, and mitigate corporate asset management for any company's essential capital.
SAP PM module allows you to manage maintenance requests and perform some repairs automatically. You can use it to record the problems in the ECC, plan labor and material activities, and record and settle costs.
SAP PM consists of three main activities that help companies to maintain their systems & equipments:
a) Inspection, which establishes the actual condition of the systems or equipment,
b) Preventive maintenance, which helps to maintain ideal conditions for the system or equipment,
c) Repair, for restoring the systems or equipment.
Integration of SAP PM with other ECC modules keeps the data current and automatically triggers processes for other functions when required. For example, a repair activity may trigger a purchase requisition for non-stock materials in MM or purchasing. Everything in SAP PM revolves around master data that is stored in centralized master data tables.
SAP PM and in general SAP's software is highly customizable, which is a cost when you're starting out – all that customizing and integrating takes time and money – but pays big dividends in operational efficiency. SAP Plant Maintenance is part of its ERP Central Component, or ECC, along with a cluster of other interrelated components. When the system is implemented, you set inspection schedules for your equipment at appropriate intervals, from hourly for critical equipment to monthly or quarterly for more durable machinery. The system creates work orders for these inspections, and technicians, in turn, log the results of each inspection into the system when it's completed. SAP PM manages the same three core activities as that hypothetical owner-operator:
Uplatz provides this comprehensive SAP PM training with self-paced videos covering extensively the concepts, application, configuration, implementation, and management of SAP PM module with practical industry scenarios and demonstrations.
Course/Topic - SAP PM - all lectures
-
In this first video lecture, you will get an overview on what is SAP PM module, what is its use, what are functional and technical modules in SAP and how Plant Maintenance module in SAP helps enterprises in getting their works done in a faster and efficient way.
-
In this tutorial, you will learn how to create Work Center in SAP PM module, a live demonstration on the same to understand the concept better through PM Studio. Also, you will understand what is the relation between Work Center and Planning Plant. Further, you will also learn how to create Equipment in this module.
-
In this video, you will understand what steps need to follow in creating a Functional Location in SAP PM, what is Functional Location Hierarchy, what is Structured Indicator and how to work on it using a live demonstration example.
-
In this tutorial, you will be learning how to set up the Structured Indicator, what is Site, Area and Asset Group in Functional Location Hierarchy and how to provide an edit mask in the Functional Location Hierarchy.
-
In this video tutorial, you will be learning some deep concepts on the Functional Location Structure and how to work on it. You will also learn to work on the ObjectInfo and how to get the list of the Functional Location. Further, it will be proceeded with some basic concepts on Class and Characteristics and how to create these in the SAP PM studio.
-
In this lecture, you will learn what is Measuring Point and Measuring Document in SAP PM module, how to create measuring point and what is the process involved in creating the Measuring Document and what are the T-Codes involved in creating these two in SAP PM.
-
This is a short video where the tutor will be seen asking about some doubt clarification from his end. It ends up with the question on What is Class and Characteristics in SAP PM?
-
In this video, you will be learning on how to configure and work on a new planning plant, location creation, creating data for plant section and plant group. All these will be learnt by a live demo session on the system.
-
In this video tutorial, you will get a deeper understanding on a live demo session on how to create equipment in a SAP PM system.
-
In this tutorial, you will be learning on how to configure a new order type for setting up a new plant in the SAP PM system. This will be proceeded with a live demo session for the same.
-
In this video tutorial, you will be learning what is costing refers to in SAP PM module, what are the different types of costing involved in the process and a detailed demonstration on how a cost is implemented in the SAP PM module system.
-
In this tutorial, you will be able to understand what is a permit in work order in the SAP PM module, what exactly is a permit, what is the T-Code for Permits, how we can access this in the studio etc. You will also get to learn what is a Notification in SAP PM and how to create a Work Order using Notification.
-
In this video tutorial, you will be learning how to assign Order Types to Maintenance Plants, use of control key, how to create activity type, use of scheduling in work order and how to work on the scheduling in the SAP PM studio.
-
In this video tutorial, you will be learning how to assign Order Types to Maintenance Plants, use of control key, how to create activity type, use of scheduling in work order and how to work on the scheduling in the SAP PM studio. Also it will further proceeded with the Preventive Process and an overview on it.
-
The first part of this tutorial is a kind of revision to the main points in the SAP PM course where the instructor will be seen explaining all the important topics related to the PM module. It will be further proceeded with the category which is an important part in working with the work center in the SAP PM module and later it will be continued with a detailed demonstration on the Capacity in the SAP module.
-
In this tutorial, you will be learning what is a reference functional location and how to work on it in the SAP PM studio with a detailed demonstration from the instructor. Also, you will be learning some more concepts on Functional Location.
-
In this lecture, you will be learning a detailed concept on BOM and how to create and work on it in the SAP PM module. You will also be learning the creation and classification of the maintenance order in a detailed demonstration from the Instructor.
-
In this final video tutorial, you will be learning on how to work with changing the maintenance order in the SAP PM module with a detailed demonstration from the Instructor. You will also be learning how to change the activity type or the price planning. It will be further proceeded with an overview on the Settlement Rule.
• This course introduces the central business processes in Enterprise Asset Management as well as the most important integration aspects with other SAP applications.
• Furthermore the course includes an overview of the topics user interfaces and user experience - showing different client types and UI technologies.
• This course shows in detail the setup of technical asset structures which will be used as the basis and the backbone for maintenance processing.
• This course also contains all relevant customizing settings (IMG) for technical objects.
• This course shows in detail the processes and functions of preventive maintenance and service.
• In a first step the creation of task lists is shown together with the relevant customizing settings.
• The focus is on creating and scheduling time-based and performance- based maintenance plans
• This course shows all relevant customizing settings (IMG) for maintenance processing with a special focus on defining new notification types and new order types.
• A separate unit shows the process and parameters for order costing and order settlement.
• Describe key elements of reporting in Enterprise Asset Management
• Run technical and controlling-specific reports relevant to Enterprise Asset Management
· Overview of SAP PM
· Logon to SAP PM module
· Organizational Structure in PM
· Functional Location
· Work Center
· Equipment
· Bill of Material (BOM)
· Characteristics and Class
· Permits
· Revision
· Measuring Point and Measuring Counter
· Refurbishment for Spare Parts
· Calibration Inspection
· Maintenance Task Lists
· Corrective or Regular Maintenance
· Breakdown Maintenance
· Preventive Maintenance
SAP PM course curriculum
1. PM Overview and Organizational Structure
PM Overview
· Process Overview
· Overview - Integration & Interaction with other modules
PM Organization Structure
· Plant
· Planning Plant
· Maintenance Planning Plant
· Relationship between organization Units
2. Technical Objects in PM
PM Master Data (Technical Objects)
· Functional Locations
· Equipment
· Material Master
· Bills of Material
· Functional Location BoM
· Equipment BoM
· Material BoM
· Work Centers
· Task Lists
· Measuring Points
· Warranties
· Permits
· Maintenance Items / Plans
3. Notifications and Maintenance Orders
Notifications
· Notification Types
· Create, Change & Display
Maintenance Orders
· Order Types
· Create, Change & Display
Order completion
· Technical Completion of the order
· Closing order and notification
· Cost Settlement
Order Status
4. Maintenance Planning (Scheduling) and Reporting
Preventative Maintenance (Maintenance Planning)
· Preventative Maintenance Process
· Task List
· Scheduling Plans
Reporting in SAP PM
· Reporting at Document Level
· Reporting with the Logistics Information System
5. Configuration & Integration
· Configuration in PM
· Integration with other modules
· Case Study
This SAP PM training course is designed for clearing the SAP SAP Certified Application Associate - SAP Maintenance and Repair exam.
In SAP PM Course module the participants will learn to manage the key activities such as inspections, notifications, maintenance and repairs. In the SAP PM course, the participants will learn the most commonly end operator PM functions, transactions and reports used for master plant maintenance. This seems to be an essential learning for all SAP PM module users.
SAP PM Certification is an important benchmark in becoming an expert PM Consultant as the course covers plant maintenance overview, master data creation, maintenance reports. SAP PM tutorial helps the participants to learn all the key concepts of SAP PM thus attaining a unique SAP certification. SAP PM course offers complete information about SAP PM functionality thus making the participant an expert SAP PM Consultant.
Uplatz online training helps the participants to successfully prepare and crack the SAP PM certification conducted by SAP. Uplatz provides appropriate teaching and expert training to equip the participants with necessary skills to implement the learnt concepts in an organization.
Course Completion Certificate will be awarded by Uplatz upon the completion of the SAP PM course training.
The SAP PM certification exam verifies that the participants possess basic knowledge and can prove their skills in the area of SAP PM. This SAP PM certification exam validates that the participant has an overall understanding about this consultant profile, and able to implement the knowledge practically in projects.
Below given are the certification details of SAP Certified Application Associate -SAP Maintenance and Repair exam:
· Certification Level: Associate
· Exam Name: SAP Certified Application Associate-SAP Maintenance and Repair
· Exam Code: C_PM_71
· Exam Mode: Online
· Total Number of Questions: 80
· Pass Score: 61%
· Time Duration: 180 Minutes
· Exam Price: $500
The SAP PM Consultant draws an average salary of $130,162 per year depending on the knowledge and hands-on experience. The SAP PM Consultant job roles are in high demand and make a rewarding career.
SAP PM Consultants are recognized across the globe. The increased usage of the SAP PM concepts in many companies help the participants to find a job opportunity easily. The leading companies hire SAP PM Consultant considering the skill of managing plant maintenance in an organization.
The learners earn most beneficial SAP PM certification through our expert training and course curriculum. Being SAP PM certified is definitely valuable credential and adds value to every organization.
The SAP PM certification is targeted to those participants who are from SAP solution management and business background and wish to excel as SAP PM consultant.
The following are the job titles in SAP PM domain:
· SAP PM Expert
· SAP PM Associate
· SAP PM Administrator
· SAP Project Manager
· SAP PM Consultant
The course content and the overall certification program helps the participants to get placed in reputed MNCs and organizations.
Q.1. What is SAP PM?
The R/3 Plant Maintenance (PM) application component provides you with a comprehensive software solution for all maintenance activities that are performed within a company. The uniform, graphical user interface is particularly user-friendly and quickly meets with acceptance, thanks to the numerous possibilities that are available for tailoring it to meet individual requirements.
The data and functions of all maintenance procedures performed within a company can be fully interconnected.
The openness of the R/3 System enables you to use external systems that are integrated with the PM component, such as geographical information systems (GIS), computer-aided design (CAD) systems and supervisory control and data acquisition (SCADA) systems.
Q.2. Is the functional location structure indicator unique across the system?
Across clients but not systems.
Q.3. What must you do if you have assets (functional locations) with the same number in several plants?
You must use the plant reference number as the first level of the functional location structure.
Q.4. What is the menu path for displaying the structure of a functional location in list form and as a graphic?
plant maintenance>technical objects>functional location>structural display
Give five examples of functional location structures.
Chemical Process, Energy (power station), Property Management, Transport, Steelworks, Production line.
Q.5. What steps must be defined in customizing for alternative labeling?
Activate alternative labeling and indicators for primary label. Create a new structure indicator, define labeling system.
Q.6. How do you define an own view for alternative label?
Activate alternative labeling, define labeling systems for functional locations, enter label internal view.
Q.7. What level of functional locations should be changed for alternative labeling?
Second level functional locations are to be changed, in changing master records extras>alternative labels>overview, change label ‘internal view’ choose structure indicator and press refresh.
Q.8. What is the menu path for creating a user profile?
Plant maintenance>technical objects>functional location>labels>user profile.
Q.9. What functions are determined by the category of the functional location?
Change documents, status profile, asset, object information key, partner determination, measuring point category.
Q.10. What are activities of a SAP PM?
The ‘SAP Plant Maintenance’ comprises of the following activities such as inspection, to measures and establish the actual condition of a technical system, preventive maintenance to measures and maintain the ideal condition of a technical system, repair to measures and restore the ideal condition of a technical system and other measures that need to be taken using the maintenance organization.
SAP PM is closely integrated with other modules (for example, Materials Management, Production, Sales and Distribution, Personnel Management, and Controlling) the data is always kept current and processes that are necessary for Plant Maintenance and Customer Service are automatically triggered in other areas (for example, a purchase requisition for non-stock material in the Materials Management/Purchasing area).
Q.11. Explain the meaning of equipment master.
Equipment Master pertains to one of the master data elements within the domain of Operations & Maintenance i.e. The SAP Plant Maintenance Module.
The business object “Equipment” is an individual, physical object that is to be maintained independently. It can be installed in a technical system or part of a technical system.
You can manage all types of device as pieces of equipment (for example, production utilities, transportation utilities, test equipment, production resources/tools, buildings, PCs).
Since many of these physical objects are managed as “assets” in Asset Management, the term “piece of equipment” was chosen for objects defined from a technical perspective, in order to avoid confusion with the activated tangible assets.
You define and manage each piece of equipment in the Plant Maintenance (PM) System in a separate master record and can set up an individual maintenance history for each one.
Q.12. For an equipment master record what fields need to be filled in?
Depends upon the Equipment. Normally, the fields which used to maintain in an Equipment master are:
Equipment Category, Constr.type (serialized), Planning Plant, Work center, Plant, Maintenance plant, Location. You can attach an equipment to another using superior Equipment filed.
Q.13. How to configure system to allow notification type change?
You can define in SPRO the “Allowed change of notification type”. Please follow the below path:
Maintenance and Service Processing –> Maintenance and Service Notification –> Notification Creation –> Notification types –> Allowed change of notification type
Q.14. Why change data not display in order?
Please check if the check box for change documents is checked or not in Customizing
PATH:- Plant Maintenance & customer service –> Maintenance & service processing –> Maintenance & service Orders –>Functions & settings for order types –> Define Change Docs,Collective Pur.Req.Indicator,Operation No.Interval
Q.15. How overheades are calculated and from where the formula is picked?
My client has default setting of 10% overhead and now they want to change.
Plant Maintenance and Customer Service–> Maintenance and Service Processing–> Maintenance and Service Orders–> Functions and Settings for Order Types–>Costing Data for Maintenance–> and Service Orders–> Maintain Costing Sheet
Select the costing sheet that you are using and push costing sheet rows, next see the column overhead rate, select the row and push overhead rate.
consumer number, check your maintenance item or plan details.
Q.16. Do we need to run this transaction code IP30 for all the maintenance plans which are scheduled on regularly daily basis or weekly basis so that if any scheduled object exists then it will get converted into the service order?
It needs to be run as per business requirements.
There are two ways to do so.
One way manually as & when you run this transaction for required PM Plans say weekly or monthly with your scheduling parameter you will get the maintenance objects.
Another way you create one variant. Now with this variant create one background job as per your need give the time period every day, every week, month & system will generate maintenance calls for you at that specified duration.
Is it necessary to run the IP Transaction code for each maintenance plan that we have scheduled ?
Yes, if it is needed that the plan should generate orders it needs to be scheduled either in background job or needs manually executed.
Q.17. Can a service order be generated automatically without running IP30 if we have scheduled a maintenance plan?
Yes, you can get a service order (PM Order) against this plant maintenance order with control key as PM03 you can get PR from PR. You can get service order again here MM integration if the auto PO concept used then auto PO (service order) gets generated.
But if you want to avoid lengthy process you can use IP10.
During each IP10 run if call falls within the date you will get maintenance call object that is PM order – ——> PR —–> PO PM Order —–> FO (Frame Work Order) PM Order —–> Service Contract ——> Value / Qty (These tab you will get in PM order operation header general data)
Q.18. Where to get the table which is having user status with Notification number. (not the system status).
From table QMEL get OBJNR(object number) using the QMNUM (notification number).
Using this OBJNR get STSMA( Status Profile) from table JSTO.
Using the OBJNR get STAT(object status) from table JEST. You may/ may not get multiple object status for an Object number.
System status number will start from E. User status number will start from I.
To get the text of the status, use the status number (STAT) and STSMA to get the status text from table TJ30T.
Q.19. How do you distinguish, in a simple manner, between Equipment that is being charged and not charged for service?
Define different equipment categories. Standard equipment reference categories for ‘Internal Machines’ and ‘Customer Equipment’ exist.
Q.20. How do you distinguish between company and customer owned equipment? Equipment on land owned by the company and land leased by the company?
Same as Q1. Explore combinations of equip. category and equipment types to achieve the design objective.
Q.21. How do you define equipment/material loaned/leased to a customer?
Read documentation on ‘Structuring Technical Systems’ in ‘Plant Maintenance / Service management’ modules. You need to define sales area (sales org/dist channel/division) for an equipment with equipment category being one for which the equipment reference category is ‘Customer Equipment’.
Q.22. How can we block service to a customer ? It has to be done through the FL, since most of the Equipment belongs to the company and is loaned to the customer.
Deactivate the FL. This allows no further creation of transaction data (service orders, etc.). However, the existing orders can be processed and closed. The deactivation can be reversed at a later date.
Q.23. Where is a Service Contract assigned to a piece of equipment?
Service contract is assigned to a material. Material is assigned to the equipment in the equipment master. This functionality is not intended for managing equipment bought from vendors (where we are getting service rather than providing service).
Q.24. Is purchasing information (Vendor, date of purchase, etc.) copied from MM to the equipment when it is being created?
Not in the standard system. But it can be done with ABAP batch jobs.
Q.25. When you maintain an assembly in a piece of equipment, is it possible to get maintenance history of the assembly? Do you have to create it as a piece of equipment?
As maintenance orders are created for FL/equipment only, maintenance history can only be tracked at that level, not at assembly level. Assemblies are mere structuring devices to have spare parts linked to equipment in a structured manner. However, in PM orders, you can mention the assembly along with the FL/Eq. Depending on your reporting needs; an ABAPer could use the ‘PM Assembly’ field in PM orders.
Q.26. What is the use of the field “Standing order”? What kind of order is it?
Standing orders are used to carry out on-going maintenance jobs and settle them at month end rather than creating a fresh PM order every time. Using order hierarchies, you could attach sub-orders to the standing order and settle them to the standing order to provide you with more precise recording of maint costs at sub-order level as well as a budget monitoring at the standing order level.
Q.27. Explain the integration points between PM and MM/FICO during the PM configuration.
Below are some integration aspects:
Integration with MM:
1. Material master record for Batch Managed material as Equipment
2. Reservations and Goods Issue for Maintenance Order
3. Material valuation class/types for refurbishment materials as equipment
4. Triggering PR from Maintenance Order
Integration with FICO:
1. Asset/Sub-Asset numbering in Equipment Master Data
2. Activity based costing for Operations performed through Maintenance Order
3. Settlement of accrued costs in Maintenance Order to G/L Account,Cost Center, Asset etc.
Q.28. What is the integration between PM and QM in SAP?
There are many interwoven activities.
Let us consider one practical issue of Spare Parts purchase.
We prefer to inspect incoming material for compliance of our requirement.
While creation of material master, tick the ‘Post to insp. stock’ box in the Purchasing Tab.
If we do not want a task list / Result recording oriented inspection, in Quality tab, choose appropriate selections,
When that Spare is received, it will go to Quality Stock.
Maint. person can check it and transfer the stock to “Unrestricted Stock” through MB1B via 261 movement, giving a reason as Accepted after Inspection or Rejected.
Above procedure is a practical example of PM QM integration.
Q.29. How to configure the integration of PP and PM, where it is being done in SPRO, what are the pre-requisite and what are the steps.
In SPRO – Under Maintenance and Service order —> general data —-> “Create System Conditions or Operating Conditions” –> check the box for PM Reservation.
In the equipment Master,
Under the Location tab, mention the PP work center and
In the Order Header data,
Give the system condition as “0” ie M/C not in operation.