SAP MM (Materials Management)
Lean SAP MM module - materials, supply chain management, procurement, inventory and warehouse management capabilities. Crack SAP MM Certification exam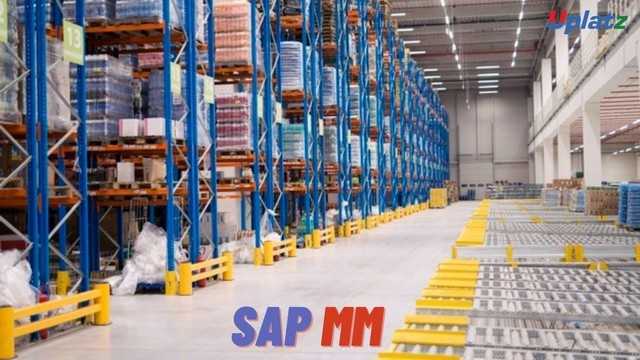
49% Started a new career BUY THIS COURSE (
USD 17 USD 41 )-
92% Got a pay increase and promotion
Students also bought -
-
- SAP PM (Plant Maintenance)
- 10 Hours
- USD 17
- 1780 Learners
-
- SAP PP (Production Planning)
- 10 Hours
- USD 17
- 1218 Learners
-
- SAP WM (basic to advanced)
- 15 Hours
- USD 17
- 3066 Learners
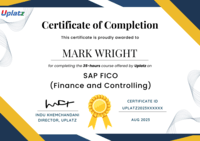
SAP MM (Materials Management) is a fundamental module of SAP ERP system that manages the material & logistics processes of an organization.
SAP MM is a core component of SAP ECC system and provides companies with materials, inventory, and warehouse management capabilities. The primary goal of SAP MM is to make sure that materials are kept in proper quantities without shortages or gaps thus optimizing the supply chain management of the organization. It also helps inventory managers, supply chain professionals and other SAP users complete the purchasing of goods in a timely and cost-effective way.
Key functions of SAP MM include material management, procurement process management or purchasing, master data management (material master and vendor master), inventory management, material requirements planning, goods setting, material shortage, consumption-based planning, and invoice verification. Transaction in SAP means processing of certain information in order to complete business process requirement. Master data is the core data that is used as a base for any transaction. Purchasing is a component of SAP MM module, and its process can be roughly depicted in below diagram. Inventory management is used to manage the inventory of the goods. Pricing procedure for MM module in SAP is a way to determine prices in purchasing documents.
Production and distribution of material, inventory, commodities have become a part of life to meet the ever-growing needs and demands of the mankind. The tasks involved in the whole supply chain are accounted for as planning, procuring, storing, and delivering them. Thus it becomes very important to make sure that the precise quantity of right quality is delivered to the concerned person in a stipulated time frame needs a level of security, system, and accuracy. This is what the SAP Materials Management application module provides. SAP MM is one of the most commonly used robust tools. The module is a combination of several components and sub-components such as procurement and managing orders, billing of orders, human resources management. All the modules work on live data.
The SAP MM module has two important master data - material and vendor. Broadly, the various levels that can be defined for a SAP MM implementation are: Client, Company Code, Plant, Storage Location and Purchase Organization. The most prominent and widely used components are Master Data, Purchasing, and Inventory.
SAP MM module strongly integrates with other SAP modules such as FI, CO, SD, QM, PM, PP, WM in a unified solution. SAP MM covers all tasks within the supply chain, including consumption-based planning, planning, vendor evaluation and invoice verification. It also includes inventory and warehouse management to manage stock until usage dictates the cycle should begin again. Electronic Kanban/Just-in-Time delivery is supported.
Uplatz offers SAP MM training videos with complete coverage of all concepts, features, configuration, implementation, and management of SAP MM software as a Consultant and/or End user. SAP MM offers a fantastic career option for individuals with experience in Supply Chain Management and Procurement, and can be tailored to a particular organization's requirements as needed. This SAP MM course curriculum will help you optimize processes such as purchasing, inventory management, invoice verification, external procurement, services, pricing, forecasting, reporting, cross applications, and customizations.
Course/Topic - SAP MM - all lectures
-
In this video, you will get a brief introduction to ERP, history, and other details associated with the ERP software.
-
This first video on ERP introduction will teach you about the basic’s concepts of ERP (Enterprise Resource Planning) and SAP, how ERP is used in organizations to optimize the resources, what are resources, what is meant by Planning etc. Also, you will get a brief introduction to SAP, its history, and its basics.
-
In this tutorial, you will be introduced to SAP. You will learn and understand what is SAP, where is it used, its benefits, different modules of SAP and their roles, the four different types of projects involved in SAP, the different types of Roles namely Functional, Technical, Administration and Techno-Functional, what is Implementation Partner, the three different tiers of SAP Architecture, System Landscape and lastly the Data Types in SAP. It also discusses the concepts on SAP projects, implementation, roll-out, upgrade, support & its roles and implementation partners. You will also learn about Architecture and its different layers, System Landscape, Data Types and its three types namely Configuration, Master and Transaction Data Type.
-
In this tutorial, you will learn how to login and navigate through an SAP system, the different initial screens, understand the concept of transaction codes and how to execute them while working in a real live project. You will also get a detailed understanding of what are the transaction lines and what is the work process to execute them. All these will be shown by the trainer in the SAP IMG screen.
-
This video is all about the knowledge on Projects and the roles associated with the ERP software. Starting with a detailed understanding of what is Project, along with its four different types and a brief explanation of each one of them.
-
In this tutorial, you will learn and understand about the SAP Enterprise Structure, the complete overview of the different elements like Company, Company Code, Plant, Storage Location, Purchasing Organization etc. All these will be shown with detailed demonstration by the tutor on the SAP system. You will also learn the theoretical concept of Posting Period in the tutorial.
-
This session is about the ASAP Methodology where you will start learning the five phases of its implementation process with a detailed explanation of each one of them.
-
This tutorial is about the Material Master and the Master Data, what are the different types of Master Data and what is Material Master. Along with this, you will also learn about the Material Number, Material Type and how to create Material Master in the SAP system. This video provides comprehensive explanation bout the Master Data and its different sets like Material Master, Vendor Master, Purchasing Info Record and Source Determination. You will get practical knowledge of how to work on Material Master and the Material Number in the SAP system.
-
This is a continuation of the previous video and in this SAP Material Master tutorial the trainer will be seen explaining the things associated with creating the Material Master in SAP system. Here you will get practical knowledge on how to create Material, schedule changing of material, display changes and finally flag material for deletion. All these will be shown by the trainer in the SAP system with real-time examples.
-
In this video, you will learn about the configuration of Material Master along with the concepts associated with it like the Screen Sequence, Creation of Screen Sequence and others. The trainer will be showing the configuration of Material Master in the SAP system. This video demonstrates how Material Master configuration is done in a step-by-step manner.
-
This is a continuation video to the configuration of Material Master where the trainer will be seen explaining the concept of Field Selection and displaying the practical implementation of Field Selection for Data Screen as well as its work process on the SAP system with industry scenarios.
-
In this video you will learn how to configure the Material Type Attributes in the SAP system. The trainer will be seen clearly explaining this with a practical demonstration on the system. You will learn the Material Types in the SAP system, difference between the valuated and non-valuated stock material, updating quantity/value in the SAP system and the material master. You will also understand how to create and configure the Material Groups in the SAP system.
-
This video will teach you the concept of vendor in the SAP system. Starting from the definition, you will have an in-depth knowledge of Vendor as far as SAP is concerned. In this tutorial, you will learn about the Vendor Master, the concept of vendor in terms of SAP, vendor master and assign vendor account groups. You will also be learning about the practical knowledge of how to create vendor master record, creating vendor, displaying vendor, block/unblock vendor, flag for deletion vendor and others.
-
In this video, you will learn about the Configuration of Vendor Master; how vendor master field selection is carried out, defining Screen Layout and Transaction-dependent and maintaining number ranges for Vendor Master Records. Along with this, you will also learn about defining industries. This tutorial is about the Configuration of Vendor Master along with providing practical examples in the SAP system on how to define field selection based on vendor account groups.
-
In this video, you will learn about the concept of End User Configuration - Purchasing Info Record (PIR), Info Category and also a detailed practical explanation on the system of how to create an Info Record in the SAP system.
-
In this tutorial, you will learn about the Source List and its detailed concept and how End User Configuration of the source list is done in the SAP system.
-
In this video, you will learn about the Purchasing Process, Purchasing Lifecycle and the Purchasing Requisition with detailed and practical demonstration by the user on the SAP system.
-
In this video, you will learn how to create Quantity Contract and Purchasing in the SAP system from an end user perspective. The trainer will be seen explaining each and every part of the document with detailed explanation in the system.
-
In this tutorial, you will learn about the Configuration of Purchasing part and how to carry out activities like defining number ranges, document types, release procedure, maintain screen layout and others. All these activities will be shown by the trainer in the SAP system taking real time examples.
-
This video will tell you about the Inventory Management which is also called as the Stock Management, the different types of stock like Unrestricted Stock, Quality Inspection Stock and the Blocked Stock. Proceeding further, you will also learn about the Goods Receipt and these all will be shown in the SAP system by the trainer.
-
This tutorial is about the Configuration of Inventory Management and how it is done. The complete configuration process will be shown on the IMG screen by the trainer throughout the video.
-
In this first part of the video, you will learn about the Special Procurement Types which is also called Special Stocks and under it what are the four different types of Special Stocks. You will be gaining practical knowledge on the Subcontract Process which is the first type of Special Stock and how it is done in the SAP system. The whole process will be shown by the trainer during the tutorial.
-
This video is a continuation video to the first part of the Special Stocks tutorial. Here you will see the trainer explaining the remaining types of Special Stocks. Along with this, you will also learn about the Stock Transfer Order and its complete work process in the SAP system.
-
In this video, you will learn about the Services associated with External Services Management along with what are the steps involved in creating a service. This will be shown by the trainer in the SAP system. You will also learn about the Service Conditions and the complete work process of it in the SAP system.
-
In this video, you will learn about the Output Determination, the configuration of Output Determination along with showing this process in the system. Further, you will also be learning about the Logistics Invoice Verification.
-
In this video, you will learn about Pricing Procedure, why it is used, what are the configuration steps involved in the Pricing Procedure, and showing the complete work process of the Pricing Procedure criteria in the system.
-
In this session, you will learn about the Split Valuation like what is Split Valuation, the configuration for Split Configuration, testing the configuration and this configuration will be shown with a detailed explanation by the trainer in the SAP system. Moreover, you will also learn about Batch Management and the configuration of the Batch Management.
-
In this session, you will learn about the MM Integration with FI/CO, its detailed overview along with the configuration for FI Integration. You will also learn about the elements like BSX, WRX, and the PRD.
-
This session will teach you about the MM Integration with PP. You will also learn about the configuration for PP Integration, MRP Controllers, Special Procurement and all these will be shown with a detailed explanation by the trainer in the SAP system. You will also be learning about Planning Run and the three different ways how it can be carried out. Further, you will learn about the Quota Arrangement.
• Acquire extensive knowledge about the Functions and Objectives of Material Management
• Get acquainted with the organizational structure of an enterprise in the SAP R/3 System
• Define various Document Types such as PR, PO, REQ, Contract, and more for Purchasing Documents
• Gain knowledge about the Release group, Release codes, Release Indicator, Release prerequisite, Release strategies
• Learn about the Schema Group, Calculation Schema, Schema Group Vendors, Schema Determination, and more
• Get Acquainted with the organization for service categories, number ranges for Service Entry Sheet, and more
• Create Physical Inventory Document and list of Inventory Differences
• Learn about Stock transport Order, Returnable Transport Packaging, Third Party Processing, and more
• Know extensively about Material Valuation, Split Valuation, Global Categories, and more
• Acquire knowledge about the Invoice Verification Procedure, Invoice for Purchase Order, Automatic Settlements (ERS), GR/IR Account Maintenance, and more
• Integrate MM with other Modules such as FI/CO, SD, PP
1. INTRODUCTION TO ERP
a. ERP Definition
b. Characteristics of ERP
c. Products of ERP
d. Benefits of using ERP
2. INTRODUCTION TO SAP
a. SAP History
b. SAP Product line
c. New Products of SAP
d. Relation of New SAP Products with the core product
e. Industry specific Products
f. Type of SAP Projects
g. Type of SAP Roles
h. Architecture of SAP
i. System Landscape
j. Types of data used in the SAP system
3. INITIAL SCREENS
a. How to login to the SAP system
b. SAP Client / GUI
c. SAP Session - What it is
d. How to open a new Session
e. Create new Sessions
f. Navigation between Sessions
g. Transactions and Activities
h. Shortcuts or Transaction Codes
i. SAP Easy Access screen
j. SAP IMG screen
k. Difference between Easy Access and IMG screens
4. ENTERPRISE STRUCTURE
i.What is Enterprise Structure
ii.The different types of Enterprise Structure
iii.Company structure in real time
iv.Company structure for each process
v.MM Structure against other process structure
vi.Enterprise Structure terms in real time against those used in the SAP system
vii.Definitions of the elements of enterprise structure
viii.Creation of Enterprise Structure elements in the SAP system
a.Group
b.Company
c.Plant
d.Store
e.Purchasing Department
f.Valuation Area
g.Controlling Area
ix.Assignment of the Enterprise Structure elements in the SAP system
a.Assign Company to Group
b.Assign Plant to Company
c.Assign Store to Plant
d.Assign Purchasing Departments
e.Assign Controlling Area
5. MASTER DATA
a. Basics of Master Data
b. Significance of Master Data
c. Usage of Master Data
I.Material Master
i.What is Material Master
ii.Views
iii.Subscreens
iv.Fields
v.Maintenance of material data in the SAP system
vi.Prerequisites for creation of Material Master Record
vii.Creation of Material Master Record
viii.Changes to Material Master Record
ix.Other end user activities in Material Master
x.Configuration of Material Master
a.Screen Sequence
What is Screen Sequence
Significance and usage of Screen Sequence
b.Screen Reference
What is Screen Reference
Creating and using Screen Reference
c.Field Selection
What is Field Selection
Criteria for defining field selection
d.Field Reference
What is Field reference
Creating and using field references
e.Material Type
What is Material Type
Usage of Material Type in the SAP system
Defining and using Material Types
f.Assign Number Range to Material Type
g.Material Number formatting
h.Material Groups
i.Purchasing Group
j.Purchase Value Key
k.Shipping Instruction
II.Vendor Master
i.Who is a Vendor
ii.What is Vendor Master Record
iii.Division of Vendor Master data
General Data
Company Code Data
Purchasing Data
iv.Vendor Classification
v.Types of Vendor
Regular Vendor
One-time Vendor
Accounting Vendor
Purchasing Vendor
Central Vendor
vi.Prerequisites for creating Vendor Master Record
vii.Vendor Account Group and its significance
viii.Creation of Vendor Master Record
ix.Changing the Vendor Master Record
x.Other End user activities of Vendor Master
xi.Configuration of Vendor Master
a.Vendor Field Selection
What is Vendor field selection
Significance of vendor field selection
Criteria for maintaining vendor field selection
b.Assignment of Number Ranges
c.Screen selection for Vendor Master records
d.Vendor Industries
e.Terms of Payment
III.Purchasing Info Record
i.Basics of Purchasing Info Record
What is Purchasing Info Record
Significance of Purchasing Info Record
ii.Types of Purchasing Info Record
iii.Prerequisites for Purchasing Info Record
iv.Creation of Purchasing Info Record
v.Changing the Purchasing Info Record
vi.Other End User activities for Purchasing Info Record
vii.Configuration
Defining Number Ranges for Purchasing Info Record
Screen Selection for Purchasing Info Record
IV.Source Determination
i.Basics of Source Determination
What is Source Determination
Source Determination options in the SAP system
ii.Source List
1.Basics of Source List
What is Source List
Significance and usage of Source List
2.Creation of Source List
3.Changing the Source List
4.Other End User activities for Source List
5.Configuration
iii.Quota Arrangement
1.Basics of Quota Arrangement
What is Quota Arrangement
Significance and usage of Quota Arrangement
2.Prerequisites for creating Quota Arrangement
3.Creation of Quota Arrangement
4.Changing the Quota Arrangement
5.Other End User activities of Quota Arrangement
6.Configuration
6. Purchasing
I.Basics of Purchasing
What is Purchasing
Difference Between Purchasing and Procurement
II.Purchasing Cycle
III.Purchasing Documents
Different types of Purchasing documents used
Division of Purchasing Document in the SAP system
Type of data maintained in each division of the purchase document
IV.Purchase Requisition
i.Basics of Purchase Requisition
ii.Creation of Purchase Requisition
iii.Other End User activities of Purchase Requisition
V.Request for Quotation (RFQ)
i.Basics of RFQ
ii.Creation of RFQ
iii.Other End User activities of RFQ
VI.Quotation
i.Basics of Quotation
ii.Creation of Quotation
iii.Other End User activities of Quotation
VII.Comparison
i.What is comparison
ii.Criteria for comparison in the real time and in the SAP system
iii.The comparison process
VIII.Purchase Order
i.What is a Purchase Order
ii.Creation of Purchase Order with reference
iii.Creation of Purchase Order without reference
IX.Release Procedure
i.Basics of Release Procedure
ii.Release Procedure and Approval process
iii.Release Characteristics
iv.Release Classes
v.Release Groups
vi.Release Codes
vii.Release Indicators
viii.Release Strategies
ix.Releasing the Purchase Order through Release Procedure
X.Optimization of Purchasing
i.Concepts of Purchase Optimization
ii.Prerequisites for creating a Purchase Order automatically
iii.Creation of Purchase Order automatically
XI.Outline Agreements
i.Basics
ii.Contracts
1.Concepts
2.Quantity Contract
3.Value Contract
4.Creation of a Contract
5.Other End User activities of Contract
iii.Scheduling Agreements
1.Concepts
2.Creation of Scheduling Agreement
3.Other End User activities of Scheduling Agreement
4.Creation of Delivery Schedule
XII.Configuration of Purchasing
i.Document Types configuration
ii.Assigning Number Ranges to Document Types
iii.Screen Selection for the Document Types
iv.Text Types and Copying Rules
v.Tolerances for Archiving documents
7. Inventory Management
I.Basics of Inventory Management
II.Stock Types
III.Movement Types
IV.Process of Goods Receipt
V.Process of Goods Issue
VI.Stock Transfers
i.What is Stock Transfer
ii.Types of Stock Transfer
iii.Transfer between Plants
iv.Transfer between Storage Locations
v.Transfer between Stock types
vi.Transfer using Stock Transport Order
VII.Return to vendor
i.Conditions under material returned to vendor
ii.Prerequisites for return to vendor
VIII.Cancellation
IX.Initial Stock
X.Reservations
XI.Physical Inventory
XII.Configuration
i.Plant Parameters
ii.Number Range assignment
iii.Screen Selection
iv.End User Restrictions for Inventory Management activities
v.Movement Types and its attributes
vi.Individual transaction configuration
8. Special Procurement Process / Special Stocks
I.Basics of Special Procurement Process / Special Stocks
II.Subcontracting
i.What is the Subcontracting process
ii.Where used
iii.Steps defining the subcontracting process
iv.Configuration for subcontract process
III.Consignment
i.What is the Consignment process
ii.Where used
iii.Steps defining the Consignment process
iv.Configuration for Consignment process
IV.Pipeline
i.What is the Pipeline process
ii.Where used
iii.Steps defining the Pipeline process
iv.Configuration for Consignment process
9. External Services Management
I.Basics of External Services Management
II.Service Master
III.Service Conditions
IV.Service Purchase Order
V.Service Entry Sheet
VI.Configuration of External Services Management
10. Valuation and Account Determination
I.Valuation Types
II.Split Valuation
i.What is Split Valuation
ii.Usage and Significance of Split Valuation
iii.Global Types
iv.Global Categories
v.Assignment
11. Logistics Invoice Verification
I.Concepts
II.Planned Costs
III.Unplanned Costs
IV.Entry of Invoice
V.Blocking of Invoice
VI.Releasing the blocked invoice
VII.Holding / Parking the invoice
VIII.Releasing the parked invoice
12. Pricing Procedure
I.Condition Table
II.Access Sequence
III.Condition Types
IV.Calculation Schema
V.Schema Group
VI.Schema Determination
VII.Condition Records
VIII.Execution of Pricing Procedure
13. Batch Management
I.Basics of Batch Management
II.Configuration of Batch Management process in the SAP system
III.Creation of Batch Master Record
IV.End User activities of Batch Management
V.Batch Management with Classification
14. Output Determination
I.Access Sequences
II.Message Types
III.Message Determination Schema
IV.Partner Roles per Message Type
V.Assign Output Devices to Purchasing Groups
15. Integration with FI/CO
I.Concepts
II.Valuation Grouping Code
III.Valuation Class
IV.Account Category Reference
V.Automatic Postings
VI.Modifiers
16. Integration with PP (Materials Requirement Planning)
I.Concepts
II.MRP Methods / Types
III.MRP Group
IV.MRP Controller
V.MRP Area
VI.MRP Configuration
17. ASAP Methodology
<span
The SAP MM (Materials Management) Certification ensures you know planning, production and measurement techniques needed to stand out from the competition.
SAP MM( Material Management ) is one of the important modules in SAP ERPsoftware and MM application module supports the procurement and inventory functions occurring in day-to-day business operations. This MM module contains many aspects such as purchasing, goods receiving, material storage, consumption-based planning, and inventory.
SAP MM meaning: SAP Material Management module is a SAP ERP component that helps organizations with material management, inventory management, and warehouse management in the supply chain process.
SAP MM is used by many big or small manufacturing, retail and other organizations, for the efficient management of raw materials and consumables. The certification exam verifies that the candidate has the fundamental knowledge required in the area of Material Management.
There is a global demand for SAP MM consultants. That much said a serious commitment and dedication is required to meet the prevailing standards. Although certification is seldom mentioned on job postings, it will go a long way to establish your worth. We urge our students to aim for certification within one month of completing the training.
Uplatz online training guarantees the participants to successfully go through the SAP MM (Materials Management) UtilitiesCertification provided by Uplatz. Uplatz provides appropriate teaching and expertise training to equip the participants for implementing the learnt concepts in an organization.
Course Completion Certificate will be awarded by Uplatz upon successful completion of the SAP MM (Materials Management) Utilities Online course.
The SAP MM (Materials Management) Utilities Draws an average salary of $134,000 per year depending on their knowledge and hands-on experience.
SAP MM (Materials Management) is a module in SAP ERP Central Component (ECC) that provides companies with materials, inventory and warehouse management capabilities.
SAP MM Demand In India. The SAP technology is going to stay in the market for at least the subsequent thirty years at the current state and it is still growing. Among the various modules, it's the functional modules like mm, SD, etc which are in great demand.
SAP Implementations 90% are business people and 10 % are developers who code in the system. The job you will be trained in is going to be SAP System Administration which does not involve coding. It involves system analysis.
Note that salaries are generally higher at large companies rather than small ones. Your salary will also differ based on the market you work in.
SAP MM - Materials Management-Consultant.
SAP MM Materials Management Application Designer.
SAP MM Materials Management Application Designer.
1. What is SAP MM and what do you know about it?
It is one of the modules in SAP that deals with the management of materials and procurement process. It also includes master data, account determination, material valuation, inventory management, invoice verification, material requirement planning, etc.
2. List out the essential components of material management.
· Determine requirements
· Source determination
· Vendor Selection
· Order Processing
· Order follow up
· Goods receipts and Inventory management
· Invoice Verification
3. What are the benefits or uses of material management?
· Material valuation
· Multi-location inventory
· Bin management
· The lot and serial traceability
· Product life cycle management
· Inventory replenishment
· Scheduling and resourcing
4. What are the features of material management?
· Purchasing
· Production and material control
· Non-production stores
· Transportation
· Material handling
· Receiving
5. What is material requirement planning (MRP)?
It is a module in SAP enterprise resource planning. It is a type of planning tool to help production and procurement planners to create feasible and realistic plans which helps to quickly initiate procurement and production process.
6. What is consumption-based planning (CBP)?
It is based on past consumption values which makes use of the forecast or other statistical procedures to determine future requirements. It is triggered when the stock level falls below a predefined reorder point or by forecast requirements calculated using past consumption values.
7. What is the difference between MRP and CBP?
In material requirement planning, the prediction of material requirement is based on sales and operations planning while in, consumption-based planning the prediction of material requirement is made, based on historical demand for materials.
8. What is Master Production Schedule (MSP)?
It is a plan for individual commodities to be produced in each time period such as staffing, production, etc. It is mostly linked with manufacturing in which the plan denotes when and how much of each product will be demanded.
9. What is a planned order in material management?
A planned order is sent to an industry and is a material requirement planning request for the procurement of a particular material at a determined time. It specifies when the internal material movement needs to be made and the amount of material that is demanded.
10. What is production order and purchase order?
A production order determines which material is to be prepared, at which location, and at what time and how much quantity is required. It also defines which components and sequence of operations are to be used and how the order costs are to be resolved.
A purchase order is a formal request or guidance from a purchasing organization to a vendor or a factory to supply or provide a certain quantity of goods or services at or by a certain point in time.
11. What is the process order?
Process Orders (PP-PI-POR) are the central component used for the accurate planning and execution of process manufacturing. A process order represents the production of batches (materials) in a production run or the rendering of services.
12. What is a transaction code in material management?
A transaction code (or t–code) consists of letters, numbers, or both, and is entered in the command field at the top of any SAP GUI screen. Each function in SAP ERP has an SAP transaction code associated with it. You can directly access any function in SAP using t-codes.
13. What are contracts in material management?
A contract is a long-term agreement with a vendor to supply a material or provide a service for a certain period of time. These are specified consequently in release orders issued against the contract when the customer requires them.
14. Define purchase requisition.
A purchase requisition is a primary document which is used as part of the accounting method to launch a merchandise or supply purchase. By processing a purchase order, suitable controls can monitor the legitimacy of purchase, as well as identify the business requirement for the products.
15. How do you create and release purchase requisition in SAP material management?
Purchase requisition creation can be done in T-code ME51N and is a straightforward process:
1) Execute ME51N transaction
2) Purchase requisition document type: NB – standard
3) Source determination: ON or OFF
4) Header note
5) Material: material number
6) Quantity and UoM
7) Storage location: in which the material is stored
8) Vendor: automatically determined by using source determination – field number
9) Tracking number: covered in previous topics, a desired value can be entered manually
10) Valuation price: copied from material master data if maintained there, if not must be entered manually (if this field is not set as optional)
11) After entering the desired information in the fields, we can save transaction data.
16. What is a special stock in material management?
Special Stocks are the stocks which belong to a company code. These are not placed in any storage location & no physical inventory is performed.
17. Mention the different types of stocks.
A. Valuated Stock
1) Unrestricted Stock
2) Quality Inspection Stock
3) Blocked Stock
B. Non-Valuated Stock
C. Special Stock
1) Subcontracting
2) Consignment
3) Stock Transport Order
4) Third Party Processing
5) Returnable Transport Packaging
6) Pipeline Handling
18. Define consignment stock.
During the consignment process, when a vendor provides material or goods, the company stores it in their stores. The vendor remains the owner of the material until a customer takes it. The liability arises as soon as the material is removed from the stores.
19. What is meant by master data?
Master Data is basically created centrally and is valid for almost all the applications. It remains constant over time but it is required to update it on a regular basis. For example, the Vendor is a type of master data and he is used for creating purchase orders.
20. What is master data management?
Master data management is a comprehensive method of enabling an enterprise to link all of its critical data to a common point of reference. When properly done, MDM improves data quality, while streamlining data sharing across personnel and departments. In addition, MDM can facilitate computing in multiple system architectures, platforms, and applications.
21. What is inventory management?
Inventory management is used to manage the inventory for the goods. It is based on several key processes. Definition of movement types, reservations, goods issue, and goods receipt.
22. What is movement type and mention a few standard movement types?
Movement types are used as indicators of what is the purpose of the goods movement (e.g. from the storage location to a storage location, receipt from the purchase order, issue for the delivery, receipt from production).
23. Define stock population.
Stock population is the total of all stock management units included in an inventory sampling. These stock management units are uniquely defined through the allocation of the stock management levels to a given inventory sampling. As a result, the stock population is also defined when you allocate stock management levels.
24. What is returnable transport packaging (RTP)?
Returnable transport packaging (RTP) is a multi-trip packaging medium in which goods can be transported more than once between retailers and customers.
25. What are quotations in SAP material management?
Quotations in SAP MM are certain requests for vendors which provides us with some information about their best prices, terms and conditions, schedules of deliveries and other information in order to select the best source for our procurement needs.
26. What is a request for quotation (RFQ) document?
RFQ or Request for Quotation also known as Invitation for Bid is a document which an organization submits to one or more potential suppliers to invite them for the bidding process for a product or service.
27. Mention the RFQ process.
For creating a request for quotation RFQ :
· Enter the transaction code or t-code as ME41 (This will lead you to ‘create RFQ’ screen)
· Enter RFQ type as ‘AN’
· Enter the quotation deadline i.e the last date by which a vendor must submit their quotation.
· Enter Purch organization and purchasing group
· Enter the delivery date and Plant
· Click on Enter
· Next, you’ll see a new screen wherein you need to fill the item codes.
· After entering the item codes, enter the vendor details
You can create more requests with different vendor details.
28. What is a request for proposal (RFP)?
RFP or Request for Proposal is a document which requests a proposal, which is generally made through a bidding process by an agency or a company for the acquisition of some commodity, asset, or service to any potential suppliers to submit business proposals.
29. What is a request for information (RFI)?
A request for information or RFI is a basic business process which collects written information about the capabilities of suppliers. It generally follows a format which can be used for comparative purposes.
30. What is the difference between RFQ, RFP, and RFI?
RFI |
RFP |
RFQ |
|
What is invoice processing? |
Gathers vendors information |
Creates the best project |
Gets the best price for a project |
Status of Solution |
Not clearly defined |
The overview is understood, yet the details need to be defined |
Project and details are clearly identified |
Key deliverables |
Provides information about the vendors |
Statement of work for a project |
Pricing details |
31. What is invoice processing?
Invoice processing is a process a company’s account payable uses to manage supplier invoices. It begins when you accept an invoice and ends when payment has been made and reported in the general ledger.
32. What is movement in goods out (MIGO)?
MIGO or Movement in Goods Out is used for goods movement such as goods issue, goods receipt, plant to plant transfer, storage location to storage location transfer, etc. Basically, MIGO is booked by the logistics department where the goods are actually received.
33. What is movement in receipt out (MIRO)?
MIRO or Movement in Receipt Out deals with invoice verification activities for bills raised from the vendors end. So, basically, MIRO is booked by the finance department.
34. What do you mean by goods receipt and post goods receipt?
Goods receipt is the physical inbound transfer for goods or material into the warehouse. It is the transfer of goods which is used to post goods received from external vendors or from in-plant production. All goods receipts result in an increase in stock in the warehouse.
Post-Goods Receipt is used to post the receipt of goods with reference to the purchase order with which the goods were ordered. If the material is delivered for some purchase order, it is important for all of the departments involved that the goods receipt entry in the system references this purchase order.