SAP MM (basic to advanced)
Learn how to maintain source list in SAP, SAP buying process, create orders and contracts, Preparation of purchase reports. Become SAP MM Consultant.Preview SAP MM (basic to advanced) course
View Course Curriculum Price Match Guarantee Full Lifetime Access Access on any Device Technical Support Secure Checkout   Course Completion Certificate75% Started a new career BUY THIS COURSE (
USD 17 USD 41 )-
84% Got a pay increase and promotion
Students also bought -
-
- Bundle Combo - SAP MM (ECC and S/4HANA)
- 50 Hours
- USD 31
- 301 Learners
-
- Bundle Combo - SAP SD (ECC and S/4HANA)
- 50 Hours
- USD 31
- 277 Learners
-
- SAP MM (Materials Management)
- 30 Hours
- USD 17
- 2423 Learners
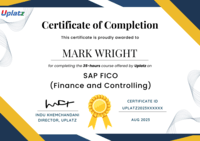
SAP MM (Materials Management) is an SAP module that deals with materials and inventory management, relating to the allocation process, master data (Master & Vendor Master), account determination and material valuation, inventory management, invoice verification, material requirements planning and many more. SAP MM is one of the important modules in SAP ERP software, and the MM application module supports the procurement and inventory functions occurring in day-to-day business operations.
SAP MM offers enterprise functions for materials, inventory and warehouse management. The main objective of SAP MM is to ensure that the material is always stored in suitable quantity and without any obstacles or gaps in the company's supply chain. In addition, supply chain experts and other SAP users can complete the purchase of goods in a timely and cost-effective manner and cope with the daily changes in this process.
This MM module contains many aspects such as purchasing, goods receiving, material storage, consumption-based planning, and inventory. SAP MM module is fully integrated with other modules in the SAP R/3 System such as Finance (FI), Controlling (CO), Sales and Distribution (SD), Quality Management (QM), Plant Maintenance (PM), Production Planning (PP), and Warehouse Management(WM).
Materials Management is also responsible for deciding the amount of material to be transported in the supply chain at each storage site, developing material replenishment plans, deciding the inventory levels to be kept for each category of product (raw material, finished goods) and transmitting material needs information within the extended supply. SAP MM covers all area within Supply Chain process including Material requirement, Source determination, Procurement process, Invoice verification and inventory usage. SAP MM is a part of Logistic Area which manage the purchase related activity of an organization.
SAP MM is used by many big or small manufacturing, retail and other organizations, for the efficient management of raw materials and consumables. Material Management as a process ensures no shortage of materials or any gaps in the supply chain process of the organization. SAP MM speeds up the procurement and material management activities, making the business run smoothly with complete time and cost efficiency. It deals with managing the materials (products and/or services) and resources of an organization with the aim of accelerating productivity and reducing costs. At the same time, SAP MM is quite versatile to accommodate changes that are frequent in any business environment.
List of important main application components coming under SAP Material management module:
MM-CBP : Consumption-Based Planning
MM-PUR : Purchasing
MM-SRV : External Services
MM-IM : Inventory Management
MM-IV : Invoice Verification
MM-IS : Information System
MM-EDI : Electronic Data Interchange
MM-FT : Foreign trade
With this SAP MM (basic to advanced) course by Uplatz, you will be able to learn how SAP MM is integrated into other modules and create and expansion of master records for material. You will also learn to maintain source list in SAP, SAP buying process, create orders and contracts, Preparation of purchase reports.
Course/Topic - SAP MM (basic to advanced) - all lectures
-
In this first video of the Introduction to ERP & SAP course, you will get a brief introduction to ERP like what is ERP, why it is used, what are the characteristics for a software product to be called as an ERP product, what is planning and resources and others. Further, you will get an introduction to SAP, the divisions of the basic product namely Functional, Technical and Administration.
-
This tutorial teaches a step-by-step approach to acquaint the readers with the SAP MM environment and how to make good use of its features. It will also help students to perform procurement of stock materials in SAP.
-
Organization structure is the framework of a company according to which business is conducted in every company.
-
Organization structure is also referred as enterprise structure. Enterprise structure is made up of many organizational units having relationship with one another.
-
Organization structure consists of many levels having direct or indirect relationship with one another.
-
This video will look at one of the company units, SAP Controlling Area, on a more detailed level. The intent is to help you understand how the Controlling Area organizes postings within the CO module and how it integrates with Financial Accounting (FI).
-
This tutorial which is part of our SAP MM course talks about SAP MM Material Master in Materials Management. You will learn about material master records in SAP MM, their functions, and how to create a new material in SAP. We will mention the SAP transactions that are related to this process.
-
SAP MM Material Master is an important element of master data in SAP which is used by most of the departments in a company. SAP MM material master enables the company to store all the information about a particular material (or product).
-
This session includes material master and vendor master. Material and vendor master are separate data records for keeping information of materials and vendors from where material is procured. The combined information of material and vendor altogether is kept in a record that we call as purchase info record.
-
A particular material can be procured from different vendors depending upon the requirement. In this way, the total requirement of a material is distributed to different vendors, which is the quota is assigned to each source of supply.
-
SAP ERP was introduced so that procurement can be done efficiently in terms of time and cost. Procurement can be done for various types of goods and services. Procurement starts with creating a purchase order which is a formal document given to vendors and it includes a list of goods and materials that are to be procured.
-
This video shows the purchase orders can be created for different types of procurement.
-
This chapter describes some of the important configurations in SAP MM. SAP MM is flexible enough to allow its configurations to be modified in the background to suit the business requirements of an organization. Configurations help in making custom enhancements in the structure.
-
Vendor selection is an important process in the procurement cycle. Once requirements are gathered, we start looking for possible suppliers who can fulfil the requirements at the best possible price.
-
A contract is a longer-term agreement with a vendor (one of the two forms of “outline agreement” in the SAP system) to supply a material or provide a service for a certain period of time.
-
A contract is a long-term outline agreement between a vendor and an ordering party over a predefined material or service over a certain framework of time.
-
Scheduling agreements are defined and managed as documents in the system.
-
In this part, we will configure all things which is required for quota arrangement.
-
A purchasing document is an instrument used by Purchasing to procure materials or services.
-
It is an approval process for Purchasing requisition and external Purchasing documents.
-
Pricing procedure in MM module is a way to determine prices in purchasing documents. It gives us functionality to assign different calculation types for different needs
-
Service master record contains the details of all the services that can be procured from an external vendor within an organization. It contains the description of services along with their unit of measure.
-
Inventory management deals with placing and handling the stock received from the vendors in correct place within the company’s premises.
-
Procurement process starts with gathering requirements and ends with procuring goods from vendors. Once the goods are procured from a vendor, they need to be placed in the company’s premises in correct place so that they can be consumed when required.
-
Inventory management deals with the management of stock, either on value or quantity basis.
-
Considering you have basic understanding of the process as discussed above let us jump in to the functional and technical process of the same.
-
This component allows you to carry out a physical inventory of your company’s warehouse stocks for balance sheet purposes. Various procedures can be implemented for this.
-
Inventory for a company’s stock and for special stocks (such as consignment stock at customer, external consignment stock from vendor, or returnable packaging) must be taken separately (in different physical inventory documents),
-
This video will help you to learn about SAP MM Batch Management Process.
-
In this video, we will learn about invoice verification in sap mm.
-
This video is about SAP FI MM integration flow. Learn the integration of SAP MM with SAP FI in depth.
-
In this video, we describe the major aspects of SAP MM integration with SAP PP module.
-
In this session, you get detailed knowledge of integration of SAP MM with SAP SD module.
-
This last video will help to provide a detailed process of integration of SAP MM and SAP WM modules.
•1) Understand the objectives, functions, and cycle of MM
•2) Maintain proper record of material and vendor along with source determination
•3) Complete the purchase cycle by defining requisition, placing order, outlining agreements, and more
•4) Create Service Master, Service PO, and Service Entry Sheet
•5) Illustrate Inventory Management (IM) skills by maintaining goods movement/receipt/issues and creating/updating physical inventory document
•6) Define valuation and account determination on both local and global categories
•7) Manage complete Logistics invoice verification including all planned/unplanned delivery costs, blocking/releasing invoices, automatic settlements (ERS), and tax/discount calculations
•8) Integration with other modules SD and PP
SAP MM (Basic to Advanced) – Course Syllabus
Module 1: Getting Started with SAP MM
Tutorial 1.1: SAP MM Overview
Tutorial 1.2: SAP MM Organizational Structure
Tutorial 1.3: SAP Procure to Pay Process
Tutorial 1.4: SAP Stock Transfer Order and Stock Transfer Process
Tutorial 1.5: Subcontracting Process in SAP
Tutorial 1.6: Vendor Consignment Process in SAP
Tutorial 1.7: SAP Movement Types
Module 2: SAP MM Master Data
Tutorial 2.1: SAP Vendor Master Data
Tutorial 2.2: SAP MM Material Master
Tutorial 2.3: SAP Purchasing Info Record
Tutorial 2.4: SAP MM Pricing Conditions
Tutorial 2.5: SAP Mass Maintenance (MASS Transaction)
Module 3: Procurement Process
Tutorial 3.1: SAP Purchase Requisition
Tutorial 3.2: SAP Request for Quotation (RFQ)
Tutorial 3.3: Convert Purchase Requisition to Purchase Order in SAP
Tutorial 3.4: SAP Purchase Order (with Reference to RFQ)
Tutorial 3.5: SAP Purchase Order Acknowledgement
Tutorial 3.6: SAP Material Valuation
Tutorial 3.7: SAP Inventory Valuation
Tutorial 3.8: SAP Goods Receipt for Consumable Material
Tutorial 3.9: SAP Goods Receipt for Stock Material
Tutorial 3.10: SAP Stock Types
Tutorial 3.11: SAP Invoice Verification
Tutorial 3.12: SAP MMBE Stock Overview
Tutorial 3.13: SAP Blanket Purchase Order
Tutorial 3.14: SAP Source List
Tutorial 3.15: SAP Evaluated Receipt Settlement
Module 4: Procurement of External Services
Tutorial 4.1: SAP Service Master
Tutorial 4.2: SAP Service Conditions
Tutorial 4.3: SAP Service Entry Sheet
Tutorial 4.4: SAP Service Invoice Verification
Module 5: Reporting
Tutorial 5.1: SAP Purchase Order Report
Tutorial 5.2: SAP Purchase Requisition Report
Tutorial 5.3: SAP Vendor Invoice Report
Tutorial 5.4: SAP Logistics Information System
Tutorial 5.5: SAP MM Info Structure
Module 6: Material Requirements Planning
Tutorial 6.1: SAP MRP Process
Tutorial 6.2: SAP MRP vs CBP
Tutorial 6.3: SAP MRP Procedures
Tutorial 6.4: SAP MRP Types
Tutorial 6.5: SAP MRP Profile
Tutorial 6.6: SAP Material Status
Tutorial 6.7: SAP Reorder Point Planning
Module 7: Integration with Other Modules
Tutorial 7.1: SAP MM FI Integration
The SAP MM (basic to advanced) Certification ensures you know planning, production and measurement techniques needed to stand out from the competition.
SAP MM can be divided into five major components. These are: materials management, plant maintenance, quality management, production planning and control, and a project management system. Each is divided into a number of sub-components.
SAP MM's functions include material management, procurement process management, master data management (material and vendor master), inventory management, material requirements planning and invoice verification. All of these MM submodules have functions that perform specific business processes for those modules.
SAP MM job requires a bachelor's degree from an accredited institution with a computer science/business background. It will also be best to have a piece of strong knowledge from designing with SAP data targets and SAP methodology and experience in customization of SAP MM business processes.
SAP MM is the most excellent certification specifically in the manufacturing and trading industries. So, if you are looking forward to a career with SAP then Material Management is one of the best choices. The different work sectors for SAP MM holders are: SAP MM consultants.
Uplatz online training guarantees the participants to successfully go through the SAP MM (basic to advanced) Certification provided by Uplatz. Uplatz provides appropriate teaching and expertise training to equip the participants for implementing the learnt concepts in an organization.
Course Completion Certificate will be awarded by Uplatz upon successful completion of the SAP MM (basic to advanced) online course.
The SAP MM (basic to advanced) draws an average salary of $115,000 per year depending on their knowledge and hands-on experience.
SAP ERP has SAP MM (C_TSCM52_67) as the most excellent Certificate, especially in Manufacturing & Trading Industries. If you are looking forward to a career with SAP MM, then it has a proper scope in delivery firms and manufacturing firms which implement SAP MM modules.
An SAP MM job requires a bachelor's degree from an accredited institution with a computer science/business background. It will also be best to have a piece of strong knowledge from designing with SAP data targets and SAP methodology and experience in customization of SAP MM business processes.
Note that salaries are generally higher at large companies rather than small ones. Your salary will also differ based on the market you work in.
Senior Associate - SAP MM – RDC.
Manager-SAP MM-TC.
SAP MM Consultants.
Q1. What is SAP MM and what do you know about it?
Ans-It is one of the modules in SAP that deals with the management of materials and procurement process. It also includes master data, account determination, material valuation, inventory management, invoice verification, material requirement planning, etc.
Q2. List out the essential components of material management.
Ans-
· Determine requirements
· Source determination
· Vendor Selection
· Order Processing
· Order follow up
· Goods receipts and Inventory management
· Invoice Verification
Q3. What are the benefits or uses of material management?
Ans-
· Material valuation
· Multi-location inventory
· Bin management
· The lot and serial traceability
· Product life cycle management
· Inventory replenishment
· Scheduling and resourcing
Q4. What are the features of material management?
Ans-
· Purchasing
· Production and material control
· Non-production stores
· Transportation
· Material handling
· Receiving
Q5. What is material requirement planning (MRP)?
It is a module in SAP enterprise resource planning. It is a type of planning tool to help production and procurement planners to create feasible and realistic plans which helps to quickly initiate procurement and production process.
Q6. What is consumption-based planning (CBP)?
Ans-It is based on past consumption values which makes use of the forecast or other statistical procedures to determine future requirements. It is triggered when the stock level falls below a predefined reorder point or by forecast requirements calculated using past consumption values.
Q7. What is the difference between MRP and CBP?
Ans-In material requirement planning, the prediction of material requirement is based on sales and operations planning while in, consumption-based planning the prediction of material requirement is made, based on historical demand for materials.
Q8. What is Master Production Schedule (MSP)?
Ans-It is a plan for individual commodities to be produced in each time period such as staffing, production, etc. It is mostly linked with manufacturing in which the plan denotes when and how much of each product will be demanded.
Q9. What is a planned order in material management?
Ans-A planned order is sent to an industry and is a material requirement planning request for the procurement of a particular material at a determined time. It specifies when the internal material movement needs to be made and the amount of material that is demanded.
Q10. What is production order and purchase order?
Ans-A production order determines which material is to be prepared, at which location, and at what time and how much quantity is required. It also defines which components and sequence of operations are to be used and how the order costs are to be resolved.
A purchase order is a formal request or guidance from a purchasing organization to a vendor or a factory to supply or provide a certain quantity of goods or services at or by a certain point in time.
Q11. What is the process order?
Ans-Process Orders (PP-PI-POR) are the central component used for the accurate planning and execution of process manufacturing. A process order represents the production of batches (materials) in a production run or the rendering of services.
Q12. What is a transaction code in material management?
Ans-A transaction code (or t–code) consists of letters, numbers, or both, and is entered in the command field at the top of any SAP GUI screen. Each function in SAP ERP has an SAP transaction code associated with it. You can directly access any function in SAP using t-codes.
Q13. What are contracts in material management?
Ans-A contract is a long-term agreement with a vendor to supply a material or provide a service for a certain period of time. These are specified consequently in release orders issued against the contract when the customer requires them.
Q14. Define purchase requisition.
Ans-A purchase requisition is a primary document which is used as part of the accounting method to launch a merchandise or supply purchase. By processing a purchase order, suitable controls can monitor the legitimacy of purchase, as well as identify the business requirement for the products.
Q15. How do you create and release purchase requisition in SAP material management?
Ans-Purchase requisition creation can be done in T-code ME51N and is a straightforward process:
1) Execute ME51N transaction
2) Purchase requisition document type: NB – standard
3) Source determination: ON or OFF
4) Header note
5) Material: material number
6) Quantity and UoM
7) Storage location: in which the material is stored
8) Vendor: automatically determined by using source determination – field number
9) Tracking number: covered in previous topics, a desired value can be entered manually
10) Valuation price: copied from material master data if maintained there, if not must be entered manually (if this field is not set as optional)
11) After entering the desired information in the fields, we can save transaction data.
Q16. What is a special stock in material management?
Ans-Special Stocks are the stocks which belong to a company code. These are not placed in any storage location & no physical inventory is performed.
Q17. Mention the different types of stocks.
Ans-A. Valuated Stock
1) Unrestricted Stock
2) Quality Inspection Stock
3) Blocked Stock
B. Non-Valuated Stock
C. Special Stock
1) Subcontracting
2) Consignment
3) Stock Transport Order
4) Third Party Processing
5) Returnable Transport Packaging
6) Pipeline Handling
18. Define consignment stock.
During the consignment process, when a vendor provides material or goods, the company stores it in their stores. The vendor remains the owner of the material until a customer takes it. The liability arises as soon as the material is removed from the stores.
Q19. What is meant by master data?
Ans-Master Data is basically created centrally and is valid for almost all the applications. It remains constant over time but it is required to update it on a regular basis. For example, the Vendor is a type of master data and he is used for creating purchase orders.
Q20. What is master data management?
Ans-Master data management is a comprehensive method of enabling an enterprise to link all of its critical data to a common point of reference. When properly done, MDM improves data quality, while streamlining data sharing across personnel and departments. In addition, MDM can facilitate computing in multiple system architectures, platforms, and applications.
Q21. What is inventory management?
Ans-Inventory management is used to manage the inventory for the goods. It is based on several key processes. Definition of movement types, reservations, goods issue, and goods receipt.
Q-22. What is movement type and mention a few standard movement types?
Ans-Movement types are used as indicators of what is the purpose of the goods movement (e.g. from the storage location to a storage location, receipt from the purchase order, issue for the delivery, receipt from production).
Q23. Define stock population.
Ans-Stock population is the total of all stock management units included in an inventory sampling. These stock management units are uniquely defined through the allocation of the stock management levels to a given inventory sampling. As a result, the stock population is also defined when you allocate stock management levels.
Q24. What is returnable transport packaging (RTP)?
Ans-Returnable transport packaging (RTP) is a multi-trip packaging medium in which goods can be transported more than once between retailers and customers.
Q25. What are quotations in SAP material management?
Ans-Quotations in SAP MM are certain requests for vendors which provides us with some information about their best prices, terms and conditions, schedules of deliveries and other information in order to select the best source for our procurement needs.
Q26. What is a request for quotation (RFQ) document?
Ans-RFQ or Request for Quotation also known as Invitation for Bid is a document which an organization submits to one or more potential suppliers to invite them for the bidding process for a product or service.
Q27. Mention the RFQ process.
Ans-For creating a request for quotation RFQ :
· Enter the transaction code or t-code as ME41 (This will lead you to ‘create RFQ’ screen)
· Enter RFQ type as ‘AN’
· Enter the quotation deadline i.e the last date by which a vendor must submit their quotation.
· Enter Purch organization and purchasing group
· Enter the delivery date and Plant
· Click on Enter
· Next, you’ll see a new screen wherein you need to fill the item codes.
· After entering the item codes, enter the vendor details
You can create more requests with different vendor details.
Q28. What is a request for proposal (RFP)?
Ans-RFP or Request for Proposal is a document which requests a proposal, which is generally made through a bidding process by an agency or a company for the acquisition of some commodity, asset, or service to any potential suppliers to submit business proposals.
Q29. What is a request for information (RFI)?
Ans-A request for information or RFI is a basic business process which collects written information about the capabilities of suppliers. It generally follows a format which can be used for comparative purposes.
Q30. What is the difference between RFQ, RFP, and RFI?
RFI |
RFP |
RFQ |
|
What is invoice processing? |
Gathers vendors information |
Creates the best project |
Gets the best price for a project |
Status of Solution |
Not clearly defined |
The overview is understood, yet the details need to be defined |
Project and details are clearly identified |
Key deliverables |
Provides information about the vendors |
Statement of work for a project |
Pricing details |
Q31. What is invoice processing?
Ans-Invoice processing is a process a company’s account payable uses to manage supplier invoices. It begins when you accept an invoice and ends when payment has been made and reported in the general ledger.
Q32. What is movement in goods out (MIGO)?
Ans-MIGO or Movement in Goods Out is used for goods movement such as goods issue, goods receipt, plant to plant transfer, storage location to storage location transfer, etc. Basically, MIGO is booked by the logistics department where the goods are actually received.
Q33. What is movement in receipt out (MIRO)?
Ans-MIRO or Movement in Receipt Out deals with invoice verification activities for bills raised from the vendors end. So, basically, MIRO is booked by the finance department.
Q34. What do you mean by goods receipt and post goods receipt?
Ans-Goods receipt is the physical inbound transfer for goods or material into the warehouse. It is the transfer of goods which is used to post goods received from external vendors or from in-plant production. All goods receipts result in an increase in stock in the warehouse.
Post-Goods Receipt is used to post the receipt of goods with reference to the purchase order with which the goods were ordered. If the material is delivered for some purchase order, it is important for all of the departments involved that the goods receipt entry in the system references this purchase order.