Overview Course - SAP PM
Learn about factory maintenance actions such as inspection, notifications, corrective and preventive maintenance.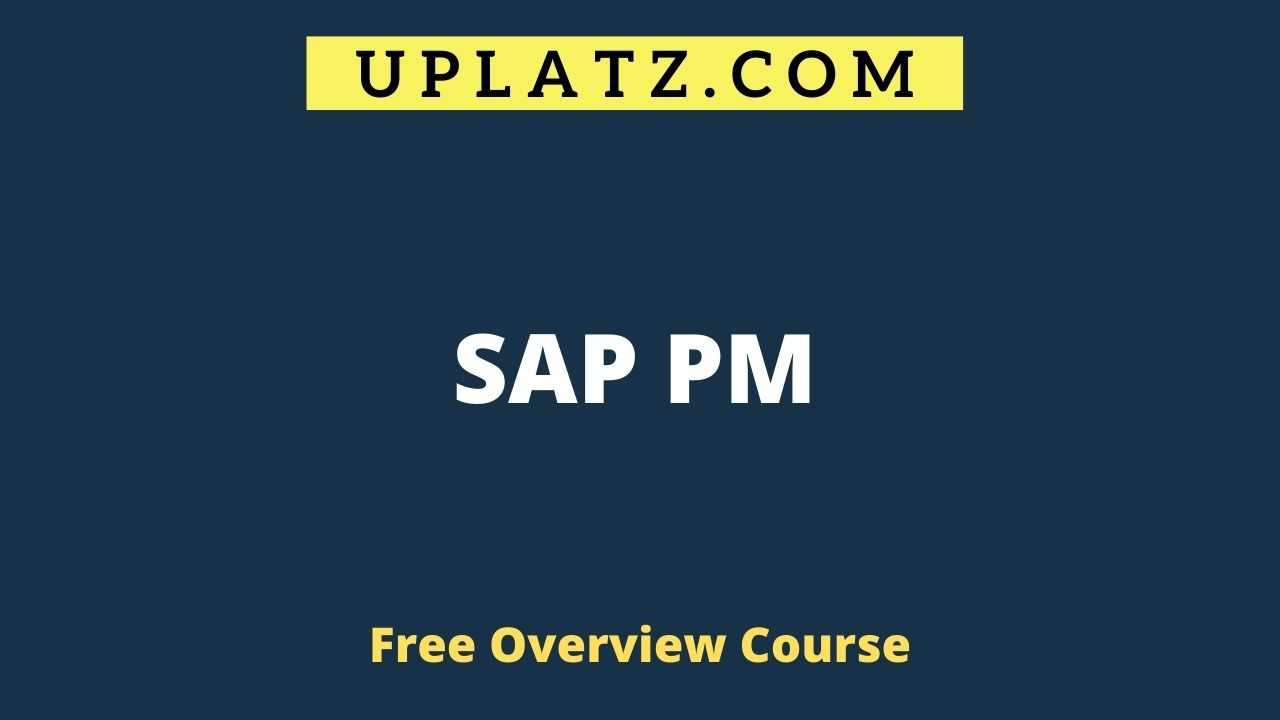
37% Started a new career Enroll Now
-
71% Got a pay increase and promotion
Students also bought -
-
- SAP PM (basic to advanced)
- 18 Hours
- USD 17
- 402 Learners
-
- SAP PM (comprehensive)
- 15 Hours
- USD 17
- 109 Learners
-
- SAP PM (Plant Maintenance)
- 10 Hours
- USD 17
- 1780 Learners
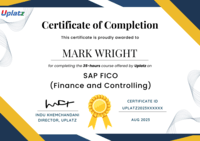
This is an overview course on SAP PM while the complete detailed-level SAP PM course is available at - https://training.uplatz.com/online-it-course.php?id=sap-pm-plant-maintenance-16. SAP Plant Maintenance (PM) is a module of the SAP ERP Central Component (ECC) that provides businesses with support on maintaining equipment and systems.
SAP PM helps in managing inspections, repairs and preventive activities. It can also record problems in planned material activities, labor, and record the cost. Also, if desired, SAP PM can control automatic repairs and maintenance requests.
PM module ensures that all machines are kept in optimal condition – without interruption. Continual support also makes sure that a plant's equipment is always ready for use by minimizing unanticipated production interruptions from an undiscovered state since the cost of a significant breakdown in your plant can be staggering. SAP PM helps avoid equipment breakdown and the loss of productivity.
In SAP ERP, maintenance function is covered with SAP PM module which is implemented for smooth and systematic running of plant maintenance function and to capture different reports. These reports are generated by automated integration of information related to equipment history, maintenance works, labor cost, material consumption, and so on. Ideally these reports will be useful in tracking consumption of material, manpower, and costs. Having this real-time data that can be monitored consistently significantly reduces the maintenance cost or material consumption wherever possible and in turn increases the company profits.
This is an overview course on SAP PM by Uplatz. The complete SAP PM training will provide you comprehensive knowledge of all components of SAP PM, their configuration and implementation steps with practical industry examples.
Course/Topic - SAP PM overview - all lectures
-
Lecture 5 - Functional Location - part 1
-
Lecture 11 - Equipment - part 2
-
Lecture 17 - Measuring Point and Measuring Counter
•Maintenance Processing (Operational functions)
•Analytics in Enterprise Asset Management,
•Further advanced features.
•Business Processes in Plant Maintenance,
•Managing Technical Objects, Maintenance
•Service Processing (Preventive)
This SAP PM Overview training course is designed for mastering the SAP Plant maintenance solution. The course content details thePM processesand able to implement while working on any project.
This SAP PMOverview training course is designed for clearing the SAP Certified Application Associate-SAP Maintenance and Repairexam.
The SAP PM Overview Course module covers the core activities such as managing inspections, notifications, maintenance and repairs.
In this SAP PM Overview course, the participants earn an opportunity to explore the SAP PM module with business support solution in handling equipment and systems.
The SAP PM Overview course details about plant maintenance, master data maintenanceand maintenance reports.
Uplatz online training guarantees the participants to successfully go through the SAP PM certification provided by SAP. Uplatz provides appropriate teaching and expertise training to equip the participants for implementing the learnt concepts in an organization.
Uplatz Course Completion Certificate will be awarded upon the completion of the SAP PM Overview course training.
The SAP PM certification exam verifies that the participants possess strong knowledge and can prove their competencies and able to implement the knowledge practically in projects.
Below given are the certification Details of SAP Certified Application Associate-SAP Maintenance and Repair
• Certification Level: Associate
• Exam Name: SAP Certified Application Associate-SAP Maintenance and Repair
• Exam Code: C_PM_71
• Exam Mode: Online
• Total Number of Questions: 80
• Pass Score: 61%
• Time Duration: 180 Minutes
• Exam Price: $500
The SAP PM Consultant draws an average salary of $130,162 per year depending on the knowledge and hands-on experience. The SAP PM Consultant job roles are in high demand and make a rewarding career.
SAP PM Consultants are recognized across the globe. The SAP PM Consultantsis responsible for managing plant maintenance in an organization. The SAP PM certification adds value to the participants professional career.
The SAP PM certification is ideal for learners who are from SAP solution management and business background and excel as SAP PM consultant
The following are the job titles:
• SAP PM Expert
• SAP PM Associate
• SAP PM Administrator
• SAP Project Manager
• SAP PM Consultant
The SAP PM Overview online course provides you with an opportunity to explore career opportunities as an SAP PM Consultant.
Q.1. What is Cost Centres and Cost Elements in SAP PM?
If the cost of maintenance is of even the slightest interest, cost centers and cost elements must be defined from the CO (Controlling) module. Costs incurred by work orders may be settled to cost centers. Cost centers are also used to determine the rate at which people are charged to work orders.
Q.2. What is Bills of Material?
Before bills of material can be defined for any module, the materials that make up the bill of materials must first be defined, typically from the MM (Materials Management) module. Work with those responsible for the maintenance of material records to define materials required for BOM use.
Q.3. Explain about Work Centers
Plant Maintenance Work Centers are based on the same functionality as Production Planning Work Centers in the R/3 system. That is, an entity with a finite capacity for work can be defined as a Work Center, whether it is a person or a machine.
Q.4. What is Plants?
One or more plants appropriate for a company’s operations must be defined. In the SAP PM module, these plants are often referred to as Maintenance Plants. It is best to work with those configuring other modules to determine what plants must be defined in R/3.
Q.5. How to explain Planning Plants in SAP PM?
In the Plant Maintenance module, these plants may also be referred to as Maintenance Planning Plants. Planning Plants are “chosen” from the list of Plants defined previously as a plant where maintenance planning is carried out. If maintenance planning, including materials planning, is performed at every plant, then every plant will be also be defined as a Planning Plant.
Q.6. Assignment of Planning Plants – what it means?
Once the plants and planning plants have been defined, the assignment of maintenance plants to planning plants must be done. Beside each maintenance plant listed in the configuration step in the IMG, the appropriate planning plant is entered or chosen.
Q.7. How to assign Internal Number Range?
An internal number range is numeric only, characters are not permitted, starting from a specific number and ending at a specific number. Internal numbers, when used, are assigned to an item automatically by the system. The next available number is always used and no selection of numbers is possible by the system users.
Q.8. What is External Number Range?
An external number range can be numeric, alphabetic, alphanumeric, and may contain certain special characters (consult the SAP documentation). This can be useful in cases where specific values need to be assigned to items.
Q.9. What is Permits?
Within the Implementation Guide, only permit categories and permit groups are defined. The actual permit definitions themselves are defined as master data, outside of the IMG, to more easily accommodate definitions and changes.
One or more permits can be associated with an object such as a functional location or a piece of equipment.
Q.10. How to define Permit Categories?
A permit category is simply a logical grouping of permits. For example, permits related to safety could belong to the Permit Category “Safety.”
Q.11. How to define Permit Groups?
Defining Permit Groups allows the use of the classification system for permits. If permits are not to be classified further than grouping them into categories in the previous configuration step, this step need not be performed.
Q.12. Explain about Warranty Counters.
A characteristic may be supplied here to provide a warranty-related counter. The characteristic must have already been defined in the Classification system. The counter may be used to represent, for example, operating hours. Another counter may be used to represent, for example, time. The counters can be checked each time that a piece of equipment breaks down in order to determine whether the equipment is still within its warranty period.
Q.13. How to define Partners?
A partner, from a Plant Maintenance perspective, is a person or other entity that has anything to do with a work order (or other object), for example. Work order-related partners include, but are not limited to, person responsible, department responsible,vendor, and so on.
Q.14. What is Functional Locations in SAP PM?
A functional location can be used to organize equipment or other functional locations into logical groups usually based on function and/or geographic location.
Q.15. What is Measuring Points?
A measuring point, simply stated, defines a place on a piece of equipment at which some type of measurement is taken. The measurement may be pressure, cycles, miles, or one of many other types of measurements. Measuring points may also be defined for functional locations, if appropriate.
Q.16. Define Consumable Types.
Fleet equipment may consume certain materials, such as gasoline (petrol), lubricating oil, and engine oil. Those consumables may be defined here.
Q.17. How to define Usage Types for Fleet Objects?
The purpose of fleet objects may be defined here. An example of a usage for a fleet object might be “Company Business Only.” Define Engine Types for Fleet Objects Engine types, such as gasoline, diesel, electric, etc. may be defined here.
Q.18. Define Object Types.
Additional categories relevant to object linking may be defined here.
Q.19. How to define Media for Object Links?
The “medium”, as discussed previously, may be defined here to provide a common linkage between objects. Two media that may be provided by default are “H2O” and “220v.” Other media can be added as required.
Q.20. Define Checking Rules.
There is a default checking rule for PM provided with the system. Unless additional checking rules will be required, no changes are required here.
Q.21. What is External Scheduling?
The settings in this configuration section are only relevant if scheduling will be performed by an external program and the dates passed to the SAP R/3 system. The settings may depend on the functionality of the external program.
The above are the top SAP PM Interview Questions that are mostly asked in an interview these interview questions are more helpful for beginners and professionals.