Overview Course - SAP MM
You can learn inventory and warehouse management, about tasks within the supply chain, including consumption-based planning, evaluation of vendor.
17% Started a new career Enroll Now
-
57% Got a pay increase and promotion
Students also bought -
-
- SAP MM (basic to advanced)
- 20 Hours
- GBP 12
- 161 Learners
-
- SAP MM (comprehensive)
- 35 Hours
- GBP 12
- 636 Learners
-
- SAP MM (Materials Management)
- 30 Hours
- GBP 12
- 2423 Learners
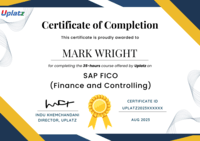
This is an overview course on SAP MM while the complete detailed-level SAP MM course is available at - https://training.uplatz.com/online-it-course.php?id=sap-mm-materials-management-4. SAP MM (Materials Management) is a module of the SAP Enterprise Resource Planning (ERP) package that is used for Procurement Handling and Inventory Management, it forms the basis for all other modules of SAP Logistics area.
MM includes all the necessary tasks in the supply chain like purchasing, planning on the basis of consumption, evaluation of vendors and verification of the invoice sent by vendors, etc.
Further, it covers inventory, planning, production, and warehouse management. The SAP MM application module allows the user to manage and procure the data in a very organized manner.
SAP MM is implemented in the majority of the SAP installations due to its effectiveness in the work. The primary work field of this module is the logistics department. In addition to that, it can also be used by enterprises to manage and maintain their purchase and manufacturing processes.
SAP MM integrates well with other SAP modules such as CO, FI, SD, PM, QM, WM, PP.
This is an overview course on SAP MM module by Uplatz whilst the full SAP MM training covers all topics comprehensively, some of them are: Material Planning, Purchasing, Inventory Management, Vendor Valuation, Invoice Verification, Statutory Requirements.
SAP MM training will help you to understand and comprehend the software in a thorough form. Many manufacturing, retail, and other such organizations use SAP MM module in order to manage raw material and consumables which has led to numerous job creation in this field. With SAP MM certification, you will be easily able to apply for SAP MM jobs in numerous companies.
Course/Topic - SAP MM overview - all lectures
-
In this tutorial, you will learn how to login and navigate through an SAP system, the different initial screens, understand the concept of transaction codes and how to execute them while working in a real live project. You will also get a detailed understanding of what are the transaction lines and what is the work process to execute them. All these will be shown by the trainer in the SAP IMG screen.
-
In this video, you will learn about the Configuration of Vendor Master; how vendor master field selection is carried out, defining Screen Layout and Transaction-dependent and maintaining number ranges for Vendor Master Records. Along with this, you will also learn about defining industries. This tutorial is about the Configuration of Vendor Master along with providing practical examples in the SAP system on how to define field selection based on vendor account groups.
-
In this tutorial, you will learn about the Source List and its detailed concept and how End User Configuration of the source list is done in the SAP system.
-
This video is a continuation video to the first part of the Special Stocks tutorial. Here you will see the trainer explaining the remaining types of Special Stocks. Along with this, you will also learn about the Stock Transfer Order and its complete work process in the SAP system.
This SAP MM Overview training course is designed for mastering the SAP MM ERP solution. The course content details theSAP MM processesand able to implement while working on any project.
This SAP MM Overview training course is meant for clearing theSAP Certified Application Associate- Procurement with SAP ERP 6.0 EhP7exam.
The SAP MM is a core part of logistics area and is useful to manage any procurement activity in an organization. The SAP MM ERP software is designed to manage the procurement processes and provide solution in various channel.
In SAP MM Overview Course module details purchasing, goods receiving, material storage and planning, inventory management. The SAP MM Overview comprises, sales, service, procurement and other core concepts.
The SAP MM Overview course covers the key functionalities such as purchase optimization, material planning and logistic verification.
Uplatz provides appropriate teaching and expertise training to equip the participants for implementing the learnt concepts in an organization.
Uplatz Course Completion Certificate will be awarded upon the completion of the SAP MM Overview course training.
The SAP MM certification exam verifies that the participants possess sound knowledge and can prove their competencies in the area of SAP Material management and able to implement the learnt knowledge practically in projects.
Below given are the certification Details of SAP Certified Application Associate- Procurement with SAP ERP 6.0EhP7
• Certification Level: Associate
• Exam Name: SAP Certified Application Associate- Procurement with SAP ERP 6.0 EhP7
• Exam Code: C_TSCM52_67
• Exam Mode: Online
• Total Number of Questions: 80
• Pass Score: 60%
• Time Duration: 180 Minutes
• Exam fee: $550
The SAP MM Consultant draws an average salary of $114,371 per year depending on the competencies, knowledge and hands-on experience.
The SAP MM Consultants are recognized across the globe. The SAP MM Consultant is responsible formanaging material and support data modeling in an organization.
The SAP MM certification is targeted to those participants who are from SAP ERP and business consulting background and excel as SAP MM consultant
The following are the job titles:
• SAP MM Associate
• SAP MM Developer
• SAP MM Functional Consultant
• SAP Consultant
The SAP MM Overview online course provides you with an opportunity to explore career opportunities as an SAP MM Consultant.
1) Explain what is SAP MM?
SAP MM (Material Management) is a functional module in SAP that deals with procurement handling and material management. The MM module contains master data, system configuration and transactions to complete the procure to pay process.
2) What are the essential components in SAP MM?
- Determine requirements
- Source determination
- Vendor Selection
- Order Processing
- Order follow up
- Goods receipts and Inventory management
- Invoice Verification
3) Mention what are the types of special stock available?
The types of special stock available are subcontracting, consignment, project, pipeline, sales order, stock transfer, returnable packaging with customer, etc.
4) List out important field in purchasing view?
The critical fields in purchasing view are
- Base unit of measure
- Order unit
- Purchasing group
- Material group
- Valid from
- Tax indicator for material
- Manufacturer part number
- Manufacturer, etc.
5) Explain the importance of the batch record?
A batch tells about a quantity of a particular product, which is processed or produced at the same time with the same parameters. The materials produced in such batch have the same values and characteristics. While, the batch record gives the information about a particular batch product and helpful in knowing whether the product has gone through GMP (Good Manufacturing Process).
6) Explain how you can link a document to a vendor master record?
To link the document with the vendor master record by using the XK01 transaction code or by using the following menu path
- SAP Menu > Logistics > Material Management > Purchasing > Master Data > Vendor > Central > XK01- Create.
7) Mention what are the major purchasing tables? List the transaction codes for them?
- Purchase requisition > EKBN
- Purchase requisition account assignment > EBKN
- Release documentation > EKAB
- History of purchase documents > EKBE
8) Mention what are the data contained in the information record?
The information record contains data related to the units of measurement, such as the products, vendor price, materials used by specific vendors, etc. It also contains information on the tolerance limit of the under delivery of data, vendor evaluation data, planned delivery time, availability status for goods.
9) Mention what is the transaction code to delete a batch?
The transaction code MSC2N is used to delete a batch. By flagging the batch master record, you can delete a batch record alternatively.
10) Mention what is the transaction code used to extend the material view?
To extend the material view transaction, code MM50 is used.
11) Explain how you can change the standard price in the master material?
The standard price for the material data cannot be updated or changed directly. However, to change the standard price you can perform the following steps
- Fill in the future fields price ( MBEW-ZKPRS ) and the effective data ( MBEW-ZKDAT) for the materials
- Select Logistics > Material Management > Valuation > Valuation Price Determination > Future Price
12) What is Source List and what is the transaction code for creating Source List?
To identify sources of supply for materials a source list is used. To create a source list the transaction code used is ME01.
13) For creating a purchasing info record what are the pre-requisites?
The pre-requisites for creating a purchase info record are
- Material Number
- MPN ( Manufacturer Part Number )
- Vendor Number
- Organizational level code
14) Explain the terms Planned delivery and GR processing time?
Planned delivery means number of calendar days required to obtain the material, and GR processing means number of workdays required after receiving the material for inspection and placement into storage.
15) What is purchase requisition as related to SAP? Mention the document types that are used in purchase requisition?
Purchase requisition in SAP determines both stock and non-stock items to the purchasing department. It can be done either manually or automatically, the document types used in purchase requisition are
- RFO (Request For Quotation)
- Outline Agreement
- PO (Purchasing Order)
16) Explain how consignment stocks are created?
In the normal purchase order or requisition, consignment stocks are created. While creating consignment stocks things to be considered is that you must enter K category for the consignment item. As a result, the goods issued are posted to consignment stores and invoice receipt is not generated.
17) Explain how is the vendor return processed without a purchase order reference?
First you have to observe the return column and then select -- Item Detail > MIGO_GR > Goods Receipt for Purchase Order. Use movement type 161 if the intention is to deduct the stock otherwise, 162 is used to undo the changes. In the end, you have to ensure that the document is a return purchase order, and then the document is saved.
You can also use transaction code M21N for this purpose.
18) Explain how you can create a vendor account group in SAP?
To create vendor account group in SAP
- Select display IMG > Financial Accounting > Accounts Payable/Receivable >Vendor Accounts > Master Records > Preparation of creating vendor master records > Define Accounts groups with Screen Layout
19) Explain what are the accounts created in SAP MM?
Assignment of account is necessary for the purchase order item, it is important in SAP MM as it determines following things
- Account assignment type
- Account that will be charged when you post the invoice or goods receipt
- Account assignment data that you should provide
20) Explain what MRP (Material Requirement Planning) list is and what is the transaction code to access MRP list?
MRP list is the initial working document from which the MRP controller starts working, and it consists of planning results information for the material. For an individual item, you can access the MRP list by using the transaction code MD05. You can also access the MRP list by navigation path
SAP Menu > Logistics > Materials Management > MRP > Evaluations > MRP List- Material
21) Explain what is CBP? What is the difference between CBP and MRP?
CBP is the past consumption values of stock; it is used to forecast future requirements. On the basis of past consumption values, the net requirement of goods is calculated.
The difference between CBP and MRP is that when you plan materials using MRP, you have to predict the materials requirement based on sales and operations planning (SOP). While in CBP you have to predict the material requirement based on historical demand for materials.