SAP Inventory Management
Take a deep-dive into SAP Inventory Management - Materials Movement & Receipt, Availability, Purchase Order, Receipt, Back-order, Inventory analysis.Preview SAP Inventory Management course
View Course Curriculum Price Match Guarantee Full Lifetime Access Access on any Device Technical Support Secure Checkout   Course Completion Certificate77% Started a new career BUY THIS COURSE (
USD 17 USD 41 )-
89% Got a pay increase and promotion
Students also bought -
-
- SAP MM (basic to advanced)
- 20 Hours
- USD 17
- 161 Learners
-
- SAP EWM (Extended Warehouse Management)
- 22 Hours
- USD 17
- 826 Learners
-
- Bundle Course - SAP Logistics (PM - PP - MM - QM - WM - SD - S4HANA Logistics)
- 200 Hours
- USD 31
- 1692 Learners
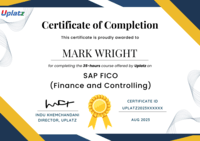
Inventory Management is the practice of managing inventory flow across an organization with maximum efficiency.
SAP Inventory Management and service-level optimisation software allows you to dynamically link customer service goals with inventory investments across the company's multistage supply chain. Best of all, SAP is a completely customizable solution. That means you can get the exact inventory management features you need without dealing with features you don’t want.
Some of the key advantages of SAP MM Inventory Management are:
a) Ensure goods are consistently available at the right time and place,
b) Reduce inventory and increase working capital with deeper insight into your supply chain,
c) Improve demand planning and decrease safety stock levels to cut costs,
d) Use enhanced supplier intelligence to minimise out-of-stock situations,
e) Enable SAP ERP to recommend specific actions that balance profitable service and inventory.
f) Automate the Order to Delivery Process
g) Manage Inventory in Real Time
h) Adapt to Changing Business Needs
Important T-codes (transaction codes) that control the movement of materials into, through, and out of your SAP system are:
a) MIGO – Goods movement
b) MB1A – Goods withdrawal
c) MB1C – Goods receipt
d) MBST – Cancel material document
e) MB02 – Change material document
SAP helps oversee the flow of materials and products in the warehouse. The process starts with managing the receipt of supplies to prevent overstocking. With that, SAP focuses on the movement of inventories and their count. Here are the primary movements of goods you will encounter in SAP.
Goods Receipt - Goods receipt can either come from suppliers or the company’s own process. The company can either approve inventories for immediate use or check them first. For inventories outside, the company can block them if they have not been ordered. In that way, it will not incur unnecessary expenses.
Goods Issue - The company may choose to process inventories for production or sell to customers. These apply mainly to intermediate goods. In either scenario, the stock level at the plant decreases. But, materials can go to scrap once they are considered unusable, damaged, or past their shelf life.
Internal Movements - Internal movement is when materials are transferred from one storage location to another. In essence, it appears to be a plant-to-plant movement. It happens before materials are used for production or sold to customers. For instance, materials are transferred to quality inspection and sent back for production.
Uplatz provides this extensive SAP Inventory Management training with self-paced videos so that you can learn the course anytime, anywhere, on any device. This Inventory Management with SAP course will help you become a successful SAP MM Consultant and an efficient Inventory Manager.
Course/Topic - Inventory Management in SAP - all lectures
-
In this video, you will get a brief introduction to ERP, history, and other details associated with the ERP software.
-
This first video on ERP introduction will teach you about the basic’s concepts of ERP (Enterprise Resource Planning) and SAP, how ERP is used in organizations to optimize the resources, what are resources, what is meant by Planning etc. Also, you will get a brief introduction to SAP, its history, and its basics.
-
In this tutorial, you will be introduced to SAP. You will learn and understand what is SAP, where is it used, its benefits, different modules of SAP and their roles, the four different types of projects involved in SAP, the different types of Roles namely Functional, Technical, Administration and Techno-Functional, what is Implementation Partner, the three different tiers of SAP Architecture, System Landscape and lastly the Data Types in SAP. It also discusses the concepts on SAP projects, implementation, roll-out, upgrade, support & its roles and implementation partners. You will also learn about Architecture and its different layers, System Landscape, Data Types and its three types namely Configuration, Master and Transaction Data Type.
-
In this tutorial, you will learn how to login and navigate through an SAP system, the different initial screens, understand the concept of transaction codes and how to execute them while working in a real live project. You will also get a detailed understanding of what are the transaction lines and what is the work process to execute them. All these will be shown by the trainer in the SAP IMG screen.
-
This video is all about the knowledge on Projects and the roles associated with the ERP software. Starting with a detailed understanding of what is Project, along with its four different types and a brief explanation of each one of them.
-
In this tutorial, you will learn and understand about the SAP Enterprise Structure, the complete overview of the different elements like Company, Company Code, Plant, Storage Location, Purchasing Organization etc. All these will be shown with detailed demonstration by the tutor on the SAP system. You will also learn the theoretical concept of Posting Period in the tutorial.
-
This session is about the ASAP Methodology where you will start learning the five phases of its implementation process with a detailed explanation of each one of them.
-
This tutorial is about the Material Master and the Master Data, what are the different types of Master Data and what is Material Master. Along with this, you will also learn about the Material Number, Material Type and how to create Material Master in the SAP system. This video provides comprehensive explanation bout the Master Data and its different sets like Material Master, Vendor Master, Purchasing Info Record and Source Determination. You will get practical knowledge of how to work on Material Master and the Material Number in the SAP system.
-
This is a continuation of the previous video and in this SAP Material Master tutorial the trainer will be seen explaining the things associated with creating the Material Master in SAP system. Here you will get practical knowledge on how to create Material, schedule changing of material, display changes and finally flag material for deletion. All these will be shown by the trainer in the SAP system with real-time examples.
-
In this video, you will learn about the configuration of Material Master along with the concepts associated with it like the Screen Sequence, Creation of Screen Sequence and others. The trainer will be showing the configuration of Material Master in the SAP system. This video demonstrates how Material Master configuration is done in a step-by-step manner.
-
This is a continuation video to the configuration of Material Master where the trainer will be seen explaining the concept of Field Selection and displaying the practical implementation of Field Selection for Data Screen as well as its work process on the SAP system with industry scenarios.
-
In this video you will learn how to configure the Material Type Attributes in the SAP system. The trainer will be seen clearly explaining this with a practical demonstration on the system. You will learn the Material Types in the SAP system, difference between the valuated and non-valuated stock material, updating quantity/value in the SAP system and the material master. You will also understand how to create and configure the Material Groups in the SAP system.
-
This video will teach you the concept of vendor in the SAP system. Starting from the definition, you will have an in-depth knowledge of Vendor as far as SAP is concerned. In this tutorial, you will learn about the Vendor Master, the concept of vendor in terms of SAP, vendor master and assign vendor account groups. You will also be learning about the practical knowledge of how to create vendor master record, creating vendor, displaying vendor, block/unblock vendor, flag for deletion vendor and others.
-
In this video, you will learn about the Configuration of Vendor Master; how vendor master field selection is carried out, defining Screen Layout and Transaction-dependent and maintaining number ranges for Vendor Master Records. Along with this, you will also learn about defining industries. This tutorial is about the Configuration of Vendor Master along with providing practical examples in the SAP system on how to define field selection based on vendor account groups.
-
In this video, you will learn about the concept of End User Configuration - Purchasing Info Record (PIR), Info Category and also a detailed practical explanation on the system of how to create an Info Record in the SAP system.
-
In this tutorial, you will learn about the Source List and its detailed concept and how End User Configuration of the source list is done in the SAP system.
-
In this tutorial, you will learn about the Configuration of Purchasing part and how to carry out activities like defining number ranges, document types, release procedure, maintain screen layout and others. All these activities will be shown by the trainer in the SAP system taking real time examples.
-
In this video, you will learn about the Purchasing Process, Purchasing Lifecycle and the Purchasing Requisition with detailed and practical demonstration by the user on the SAP system.
-
In this video, you will learn how to create Quantity Contract and Purchasing in the SAP system from an end user perspective. The trainer will be seen explaining each and every part of the document with detailed explanation in the system.
-
In this tutorial, you will learn about the Configuration of Purchasing part and how to carry out activities like defining number ranges, document types, release procedure, maintain screen layout and others. All these activities will be shown by the trainer in the SAP system taking real time examples.
-
This video will tell you about the Inventory Management which is also called as the Stock Management, the different types of stock like Unrestricted Stock, Quality Inspection Stock and the Blocked Stock. Proceeding further, you will also learn about the Goods Receipt and these all will be shown in the SAP system by the trainer.
-
This tutorial is about the Configuration of Inventory Management and how it is done. The complete configuration process will be shown on the IMG screen by the trainer throughout the video.
-
In this first part of the video, you will learn about the Special Procurement Types which is also called Special Stocks and under it what are the four different types of Special Stocks. You will be gaining practical knowledge on the Subcontract Process which is the first type of Special Stock and how it is done in the SAP system. The whole process will be shown by the trainer during the tutorial.
-
This video is a continuation video to the first part of the Special Stocks tutorial. Here you will see the trainer explaining the remaining types of Special Stocks. Along with this, you will also learn about the Stock Transfer Order and its complete work process in the SAP system.
1) Perform goods movements
2) Create material reservations and issue goods
3) Post stock transfers
4) Perform physical inventory counts and corrections
5) Run basic inventory and stock reports
6) Understand the concept of Inventory Management in SAP
7) Understand the concept of Movement types in SAP
8) Understand the concept of Reservation in SAP
9) Understand the impact of different movement types in SAP
1. Basics of Inventory Management
2. Stock Types
3. Movement Types
4. Process of Goods Receipt
5. Process of Goods Issue
6. Stock Transfers
i. What is Stock Transfer
ii. Types of Stock Transfer
iii. Transfer between Plants
iv. Transfer between Storage Locations
v. Transfer between Stock types
vi. Transfer using Stock Transport Order
7. Return to Vendor
i. Conditions under material returned to vendor
ii. Prerequisites for return to vendor
8. Cancellation
9. Initial Stock
10. Reservations
11. Physical Inventory
12. Configuration
i. Plant Parameters
ii. Number Range assignment
iii. Screen Selection
iv. End User Restrictions for Inventory Management activities
v. Movement Types and its attributes
vi. Individual transaction configuration
This SAP Inventory Management training course is designed for exploring the stock management activities.
The SAP Inventory Management is a sub-module of SAP supply chain management which is one of the main component in ERP system.
In SAP Inventory Management Course module, the participants can learn to apply the stock management activities through value or quantity. In the SAP Inventory Management course, the participants will learn about the process of ordering, storing in warehouse using inventory within an organization.
This is an essential learning for all SAP Inventory module users. The inventory management module also includes stock entry, storing records of stock or goods movements. Through this SAP Inventory Management course, the participants can demonstrate inventory management concepts and implementation of stock activities.
The SAP Inventory Management tutorial helps the participants to learn the inventory processes to improve the stock or goods development and the process of creating such items. Inventory Management in SAP course offers the monitoring the product flow activities thus making the participant an expert SAP Inventory Consultant.
Uplatz online training helps the participants to successfully apply for the SAP Inventory Management Certification provided by SAP. Uplatz provides appropriate teaching and expertise training to equip the participants with skills for implementing the learnt concepts in an organization.
Course Completion Certificate will be awarded by Uplatz upon the completion of the SAP Inventory Management course.
The SAP Inventory Consultant draws an average salary of $93,974 per year depending on the knowledge and hands-on experience. The SAP Inventory Consultant job roles are in high demand and make a rewarding career.
The SAP Inventory Consultants are recognized across the globe. The increased usage of the SAP inventorymethods and processes in many companieshelp the participants to find a job opportunity easily.
The leading companies hire SAP Inventory Consultant considering the skill of managing the stock or goods movements, recording and documenting themin an organization. The learners earn most beneficial SAP Inventory management completion certification through our expert training and course curriculum.
The SAP Inventory management course is targeted to those participants who are from business consulting background and excel as SAP Inventory consultant/manager/end-user
The following are the job titles:
• SAP Stock Manager
• SAP Inventory Manager
• SAP MM/WM/EWM Consultant
• SAP SD/PP Consultant
• SAP Stock or Goods Consultant
• SAP Inventory Associate
• SAP MM Inventory Consultant
The SAP Inventory Management course provides you with an opportunity to explore career prospects as SAP Inventory Management Consultant / Power User.
Q1: How to cancel an invoice & payment document?
Ans)
Please follow the steps below in order to cancel the invoice & payment document:
- First go to Banking → Incoming Payments for displaying the Incoming Payment document
- Now navigate to upper menu bar and click Data → Cancel.
Note: Also please copy the Invoice to a Credit Memo, as the Invoice opens automatically when you cancel its payment.
Q2: How to remove an item from the system?
Ans)
Only those item can be removed which has no transaction and also is not included in the draft documents. When an item is removed then it totally deleted from the system and cannot be restored. Those items that have any document linked to it cannot be removed.
In order to remove an item from the system, navigate to Inventory → Item Master Data, locate the item, right-click it and then choose Remove.
Only these items can be removed which has:
- those that have no linked transactions
- no MRP Order Recommendations
- no draft documents
- no rules for Advanced GL account determination
The following queries can be used to check the items
whether the item has associated Advanced G/L determination rules:
- select "Itemcode" , * from ogar where "ItemCode"='XXXX'
whether the item was used in a historical document:
- select * from adoc where "DocEntry" in (select "DocEntry" from ado1 where "ItemCode"='XXXX')
whether the item was used in an Inventory Counting or Inventory Posting
- select * from oiqr where "DocEntry" in (select "DocEntry" from iqr1 where "ItemCode"='XXXX')
- select * from oinc where "DocEntry" in (select "DocEntry" from inc1 where "ItemCode"='XXXX')
whether the item was used in an MRP scenario or recommendation
- select * from omsn where "AbsEntry" in (select "AbsEntry" from msn4 where "ItemCode" = 'XXXX')
- select * from orcm where "ItemCode" ='XXXX'
Note: From SAP Business One version 8.8, the options to Cancel and Restore an item, have been removed.
Q3: How to remove BP (Business Partner) master record from the system?
Ans)
Please follow the steps below in order to remove a BP (Business Partner) master record from the system
- First select the Business Partner (BP) master record you want to remove from Business Partners → Business Partners Master Data.
- Now go to the upper menu bar and click Data -> Remove
Note: The Business Partners with no transaction can be removed and once removed the BP cannot be restored.
Q4: How to hide those columns which were added to marketing document but not usefull anymore?
Ans)
In order to resolve this please follow the steps below:
- First, open the equired document.
- Now navigate to the upper menu bar and click Form Settings.
- Now in the Table Format tab please uncheck required columns or click Default to return to the system default settings.
- Now atlast save the changes and close the window
Q5: How to create one inventory doc with the help of all your materials to count instead of creating one doc for each material?
Ans)
Please follow the steps below in order to create one inventory doc with all your materials:
- User can carry out transaction MI01 with the reference of their plant & storage location. Then the user can then enter as many inventory materials as per as his need
- Please set the maximum number of items for example 50 via Transaction MICN. The same can be done via using transaction OMCN.
Q6: What is the relation between GR/IR account and Inventory?
Ans) If the user is involved with inventory, then the user need a GR/IR account (Inventory Account) while posting IR. Whereas if the user is not involvedt in inventory, then the user system does not need the GR/IR account while posting IR. In this case, the system needs a G/L instead of GR/IR account.
Q7: How can we find the logical value for stock item by date?
Ans)
Use Transaction MC49
Menu path :
1. Information systems -> Logistics -> Inventory management->Material -> Document Evaluations -> Stock value -> Mean inventory or
2. Logistics -> Logistics controlling -> Inventory Controlling Environment -> Document evaluations -> Stock value -> Mean Stock Value.
Q8: How to transfer stock from one vendor to another vendor?
Ans): First perform 542 and then 541 to the new vendor.