SAP PP (basic to advanced)
Learn SAP PP module. Production Planning, Master Data, Master Planning, Material Requirement Planning, Production Orders, Discrete Manufacturing, morePreview SAP PP (basic to advanced) course
View Course Curriculum Price Match Guarantee Full Lifetime Access Access on any Device Technical Support Secure Checkout   Course Completion Certificate88% Started a new career BUY THIS COURSE (
USD 17 USD 41 )-
92% Got a pay increase and promotion
Students also bought -
-
- SAP MM (Materials Management)
- 30 Hours
- USD 17
- 2423 Learners
-
- SAP WM (Warehouse Management)
- 30 Hours
- USD 17
- 1523 Learners
-
- Bundle Course - SAP SCM (Supply Chain Management)
- 140 Hours
- USD 31
- 3351 Learners
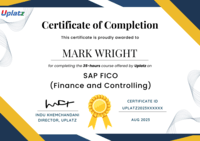
SAP PP (Production Planning) is a component of SAP ECC that allows the businesses to plan the manufacturing, sale and distribution of goods. SAP PP module handles the master data required for Bill of Materials (BOMs) activity, work center and routing, and keeps it in a separate component.
SAP Production Planning is one of the most important modules of SAP dealing with processes such as material planning, capacity planning, production planning, goods movement, and billing of goods. SAP PP facilitates the process of meeting the demand and manufacturing capacity of an organization as well as helps an organization schedule the procurement and manufacturing of products.
SAP PP is fully integrated with other modules of SAP such as SAP MM, QM, PM, FICO. SAP PP sub-modules vary as per industry type for e.g. discrete production, repetitive production, or production industries.
SAP PP module manages the key steps in executing a production order viz. Convert Planned Order to Production Order, Issue the Production Order,Issue Goods for Production Order, Production Order Confirmation, Good Receipts w.r.t Production Order.
Key Components of SAP PP include:
1. Master Data
a) Material Master: Central repository for information related to all materials managed in the system.
b) BOM (Bill of Materials): A comprehensive list of raw materials, components, and assemblies required to build a product.
c) Work Center: Defines where production activities are carried out and includes information on resources like labor and machines.
d) Routing: Describes the sequence of operations required to produce a product.
2. Planning
a) Demand Management: Determines the requirement quantities and delivery dates for finished products and components.
b) MRP (Material Requirements Planning): Calculates the material requirements and generates procurement or production orders.
c) CRP (Capacity Requirements Planning): Ensures that production capacity is utilized efficiently and identifies capacity constraints.
3. Production Execution
a) Production Orders: Detailed instructions to produce a specific quantity of a product within a specified time frame.
b) Process Orders: Used for process industries like chemicals or pharmaceuticals, where production is continuous or batch-oriented.
c) Kanban: A scheduling system for lean and just-in-time production.
4. Shop Floor Control
a) Order Confirmation: Recording of production progress and completion.
b) Goods Movement: Tracking of materials and finished products throughout the production process.
5. Integration with other Modules
a) MM (Materials Management): Integration ensures that materials are available for production and manages inventory levels.
b) SD (Sales and Distribution): Coordinates production with customer orders and delivery schedules.
c) FI (Financial Accounting) and CO (Controlling): Links production activities with cost accounting and financial reporting.
This SAP PP training by Uplatz provides in-depth knowledge of all functions within PP module with practical examples and live server configurations.
Course/Topic 1 - SAP PP Introduction - all lectures
-
In this lecture session we learn about SAP pp introduction and also cover overview and factors of SAP PP.
Course/Topic 2 - Master Data in PP - all lectures
-
In this lecture session we learn about master data in PP and also cover how we calculate and manage the master data in SAP PP.
-
In these lecture sessions we learn about configuration settings for master data and also talk about how we manage the master data.
-
In this lecture session we learn about field selection task list overview and also talk about settings of master data.
Course/Topic 3 - Material Master in PP - all lectures
-
In this lecture session we learn about material master data and also talk about how we calculate material master data in brief.
-
In this lecture session we learn about material master and also talk about why we need material master data in SAP PP.
Course/Topic 4 - BOM in PP - all lectures
-
In this lecture session we learn about bill of material and also talk about bill of material classification and how we create a bill of material in SAP.
Course/Topic 5 - Work Center in PP - all lectures
-
In this lecture session we learn about work centers in SAP PP and also talk about all types of work centers like machines, people, production lines and groups of craftsmen.
Course/Topic 6 - PRT and Routing - all lectures
-
In this lecture session we learn about PRT and routine and also talk about functions and factors of PRT and routine in SAP PP.
Course/Topic 7 - Scrap in PP - all lectures
-
In these lecture sessions we learn about production versions and different types of scrap and also talk about factors of production version and different types of scraps.
-
In this lecture session we learn about scraps assembly and components and operations and also talk about how we manage scraps assembly and component and operation in brief.
Course/Topic 8 - Planning Procedures in PP - all lectures
-
In this lecture session we learn about MRP planning and consumption in SAP PP and also talk about consumption based planning in SAP.
-
In this lecture session we learn about forecast based planning and time phased planning in SAP and also talk about factors of forecast based planning.
-
In this lecture session we learn about automatic reorder points of SAP pp and also talk about the importance of automatic reorder points.
Course/Topic 9 - Internal Procurement Process
-
In this lecture session we learn about the internal procurement process and also talk about the difference between internal procurement and external procurement.
-
In this lecture session we learn about the internal procurement process and also talk about the importance and functions of the internal procurement process.
-
In this lecture session we learn about the internal procurement process by running MRP for independent requirements in SAP PP.
-
In this lecture session we learn about the internal procurement process of the release production process and also talk about some issues.
Course/Topic 10 - Batch Management in PP - all lectures
-
In this lecture session we learn about batch management in pp and also talk about the functions of batch management in SAP PP.
Course/Topic 11 - Serial Number Management in PP - all lectures
-
In this lecture session we learn about serial numbers and also talk about serial number management in SAP PP.
Course/Topic 12 - Sales and Operations Planning (SOP) - all lectures
-
In this lecture session we learn about sales and operation planning SOP and also talk about functions of sales and operation planning in SOP.
Course/Topic 13 - Strategy Group for MTS and MTO
-
In this lecture session we learn about strategy groups for MTS and MTO process and also talk about the importance of strategy groups for MTS and MTO process.
-
MTO Configurable Material or Variant Configuration of strategy of groups in SAP PP and also learn about how we make strategy groups.
Course/Topic 14 - SAP PP integration with SAP QM - all lectures
-
In this lecture session we learn about SAP pp integration with SAP QM and also talk about all integration with SAP QM.
Course/Topic 15 - Master Production Schedule (MPS) - all lectures
-
In this lecture session we learn about availability check in MRP and introduction of MPS and also talk about overview of MPS in SAP.
-
In this lecture session we learn about master production schedule MPS and also talk about how we manage the master production in SAP PP.
Course/Topic 16 - Repetitive Manufacturing Process - all lectures
-
In this lecture session we learn about repetitive manufacturing processes and also talk about factors of repetitive manufacturing processes in SAP PP.
Course/Topic 17 - SAP PP integration with SAP PI - all lectures
-
In this lecture session we learn about SAP PP integration with SAP pi and also talk about the importance of SAP PP integration with SAP.
Course/Topic 18 - SAP PP integration with SAP FI - all lectures
-
In this lecture session we learn about SAP PP integration with SAP FI factors and functions of SAP pp integration.
Course/Topic 19 - Order Types and Production Scheduling Profile - all lectures
-
In this lecture session we learn about creating order types and production scheduling profile and also talk about how we create order types in SAP PP.
• Master Data.
• Associated Jobs and Positions in the Industry.
• Sales and Operational Planning.
• Planning Material Requirement.
• Goods Movement in PP.
• Master Planning.
• Batch Management.
• Repetitive and distinct Manufacturing Process.
1. Overview of ERP, SAP, SAP PP
· Understanding ERP and ERP as an ERP
· Architecture of ERP
· Discuss on the implementation methodology and importance of the same
· Importance of SAP PP as a functional module
2. SAP PP process flow
· PP total flow understanding
3. Master Data Overview
· Material Master
· BOM configuration and use in production planning
· Routings (task lists) configuration and use in production planning
· Production Versions
· Importance as per business needs
· Work Center
4. Master Planning
· Sales Operations Planning
· Demand Management
· Long term Planning
· Planned independent requirements
5. Forecasting
· Process review
· Process overview and flow to demand management
· Forecasting process and MRP control
· Example with real Business Process
6. Material Requirement Planning (MRP) and Master Production Schedule (MPS)
· Process review
· MPS
· MRP
· MRP run configuration and evaluation tools
· Consumption Based Planning
· Lot Size Procedures
· Example with real Business Process
7. Production Orders
· Scheduling of production orders
· Production order components
· Production Resources & Tools (PRTs)
8. Scheduling
· Scheduling process
· Capacity planning
· Example with real Business Process
9. Discrete Manufacturing
· Master Data involved
· Configurations needs
· Purpose
· Planned order structure
· Production order types
· Material staging and withdraw
· Production confirmation
· Goods movement
· Order settlement
10. Repetitive Manufacturing
· Master Data
· Planning
· Backflushing
11. REM
· REM process review
· Master Data involved
· Configuration needs
· Purpose
12. Support Process
· Support Process discussion
13. Integration of SAP PP with other SAP modules
· Material Management (MM)
· Sales and Distribution (SD)
· Quality Management (QM)
· Plant Maintenance (PM)
14. Reporting and Tools
· Production planning reporting
· Material requirement planning reporting
15. Other aspects of PP
· Production Planning in process industries
· Classification system
This SAP PP (basic to advanced) training course is designed to help individuals prepare and pass the SAP Certified Application Associate - Production Planning and Manufacturing with SAP ERP 6.0 EHP7 exam.
SAP PP is an important module in SAP and is used to track and keep a record of the manufacturing process flows and also the movements of stock or goods from being raw material to finished goods. The SAP PP Basic to Advanced course covers production planning master data, discrete manufacturing comprising basic to advanced concepts.
The SAP PP Associate certification exam covers material and capacity requirement planning, Production order basics and advanced, and process orders.
Course Completion Certificate will be awarded by Uplatz upon the completion of the SAP PP course Basic to Advanced training.
The SAP PP certification exam verifies that the participants possess basic knowledge and can prove their skills in the area of SAP Production planning and manufacturing. This SAP PP certification exam validates that the participant has an overall understanding about this consultant profile, and able to implement the knowledge practically in projects.
Below given are the certification details of SAP Certified Application Associate - Production Planning and Manufacturing with SAP ERP 6.0 EhP7
· Certification Level: Associate
· Exam Name: SAP Certified Application Associate- Production Planning and Manufacturing with SAP ERP 6.0 EhP7
· Exam Code: C_TSCM42_67
· Exam Mode: Online
· Total Number of Questions: 80
· Pass Score: 63%
· Time Duration: 180 Minutes
· Exam fee: $550
The SAP PP Consultant draws an average salary of $78,112 per year depending on the knowledge and hands-on experience. The SAP PP Consultant job roles have a huge demand in the growing industry.
If you're interested in a career in production and planning, then SAP PP (basic to advanced) is a great course to pursue. There is a great demand for SAP PP consultant in the field of production and planning. The scope of SAP PP module is growing exponentially considering the production management across the industry.
The SAP PP certification is targeted to beginners, managers, SAP ERP background and excel in production area.
The following are the job titles in this domain:
· SAP PP Associate
· SAP PP Consultant
· SAP PP Developer
· SAP PP Functional Consultant
· SAP Consultant
The SAP PP (basic to advanced) course helps the participants to learn and implement the PP module concepts in an enterprise.
Following are some of the key interview questions & answers of SAP PP module.
1. What is SAP PP?
SAP PP (Production Planning) is a module within the SAP ERP (Enterprise Resource Planning) system that focuses on managing and controlling the production processes in an organization. It is one of the core modules in the SAP suite and plays a vital role in ensuring smooth and efficient production operations. The main objectives of SAP PP are to plan, execute, and monitor the entire production process, from the creation of a production plan to the delivery of finished goods. It provides tools and functionalities to help businesses optimize their production operations, increase productivity, reduce production costs, and meet customer demands effectively.
2. What are the key components and functionalities of SAP PP?
Master Data, Material Requirements Planning (MRP), Production Orders, Work Centers and Routings, Capacity Planning, Shop Floor Control, Variant Configuration, Production Version, Make-to-Order (MTO) and Make-to-Stock (MTS) Scenarios, Subcontracting.
3. What is the purpose of Rate Routing in SAP PP?
Rate Routing is used to calculate the standard production time for a material based on specific conditions, such as batch size or production quantity.
4. How do you perform Material Availability Check in SAP PP?
You can perform Material Availability Check using the transaction code CO09 or by navigating to Logistics > Production > Material Availability > Check Material Availability.
5. What is the difference between Lead Time Scheduling and Capacity Leveling in SAP PP?
Lead Time Scheduling determines the planned start and finish dates for a production order based on available capacity, while Capacity Leveling balances workloads across work centers to avoid capacity overloads.
6. How do you perform a Goods Issue for a Production Order with Batch Management in SAP PP?
You can perform a Goods Issue for a Production Order with Batch Management using the transaction code COGI or by navigating to Logistics > Production > Goods Issue for Production Order with Batch.
7. Explain the concept of Split Valuation in SAP PP.
Split Valuation allows materials to be valuated differently based on certain characteristics, such as quality or location.
8. How can you integrate SAP PP with other SAP modules?
SAP PP can be integrated with other SAP modules like SAP MM (Materials Management), SAP QM (Quality Management), and SAP SD (Sales and Distribution) to ensure seamless data flow and process integration.
9. What is the use of the Production Order Confirmation in SAP PP?
Production Order Confirmation is used to record the actual production quantities and activities performed during the production process.
10. How do you handle Subcontracting in SAP PP?
Subcontracting in SAP PP can be managed using the subcontracting purchase order process, where a vendor is assigned to perform certain operations on a material.
11. What is the purpose of Backorder Processing in SAP PP?
Backorder Processing helps in managing and fulfilling customer orders that couldn't be delivered due to insufficient stock.
12. How can you perform Resource-Related Billing in SAP PP?
You can perform Resource-Related Billing using the transaction code DP91 or by navigating to Logistics > Production > KANBAN > Environment > Billing.
13. Explain the concept of Production Version in SAP PP.
Production Version allows you to define different versions of routings and BOMs for a material to accommodate changes in the production process.
14. How do you handle Order Settlement in SAP PP?
Order Settlement in SAP PP involves transferring the costs incurred during production to the appropriate cost centers or cost objects.
15. What is the purpose of Capacity Evaluation in SAP PP?
Capacity Evaluation allows you to check whether the available capacity in a work center is sufficient to meet the production demands.
16. How can you perform Mass Processing of Production Orders in SAP PP?
You can perform Mass Processing of Production Orders using the transaction code COHV or by navigating to Logistics > Production > Production Control > Order > Mass Processing.
17. What is the difference between Finite and Infinite Scheduling in SAP PP?
Finite Scheduling considers the availability of resources and work center capacities, while Infinite Scheduling ignores these constraints and schedules production orders without considering resource availability.
18. How can you handle Production Version Effectivity in SAP PP?
Production Version Effectivity allows you to control which production version is valid for specific periods or conditions.
19. What is the use of the Order Type field in a Production Order in SAP PP?
The Order Type field in a Production Order defines the purpose of the order, such as standard production, batch order, or repetitive manufacturing.
20. How can you perform a Capacity Leveling in SAP PP?
You can perform Capacity Leveling using the transaction code CM21 or by navigating to Logistics > Central Functions > Capacity Planning > Leveling.
21. What is the difference between Production Planning and Production Control in SAP PP?
Production Planning involves activities like demand forecasting, MRP, and capacity planning, while Production Control focuses on managing and executing production orders on the shop floor.
22. How do you perform Long-Term Planning (LTP) in SAP PP?
You can perform Long-Term Planning using the transaction code MS31 or by navigating to Logistics > Production > Master Data > Material Requirements Planning > Long-Term Planning.
23. What is the use of the Serial Numbers in SAP PP?
Serial Numbers are used to uniquely identify individual items, making it easier to track and manage them during production and throughout the supply chain.
24. How can you handle Repetitive Manufacturing in SAP PP?
Repetitive Manufacturing in SAP PP is suitable for producing high-volume, repetitive products, and it can be managed using repetitive manufacturing profiles.
25. Explain the concept of Pegging in SAP PP.
Pegging is the process of linking dependent requirements (such as sales orders) to the corresponding supply elements (such as production orders) to understand the relationships between them.
26. How do you handle Make-to-Order (MTO) scenarios in SAP PP?
Make-to-Order scenarios in SAP PP involve creating production orders based on specific customer requirements received as sales orders.
27. What is the purpose of the Planning Strategy field in a Material Master in SAP PP?
The Planning Strategy field in a Material Master determines how the material's requirements will be planned, whether through forecast-based planning, reorder point planning, or other strategies.
28. How do you perform a Capacity Planning in SAP PP?
You can perform Capacity Planning using the transaction code CM01 or by navigating to Logistics > Central Functions > Capacity Planning > Work Center View.
29. What is the use of the Special Procurement Key field in a Material Master in SAP PP?
The Special Procurement Key field in a Material Master is used to determine how the material will be procured for specific scenarios, such as external procurement or internal production.
30. How can you handle Lot Size Calculation in SAP PP?
Lot Size Calculation in SAP PP involves determining the appropriate quantity to produce based on factors like economic order quantity, safety stock, and lot-for-lot.
31. What is the use of Order Change Management in SAP PP?
Order Change Management allows you to track and manage changes made to production orders, ensuring proper documentation and approval processes are followed.
32. How do you handle Material Requirements Planning (MRP) for Dependent Requirements in SAP PP?
You can handle MRP for Dependent Requirements by configuring the relevant settings in the MRP views of the material master and by defining the dependent requirements in routing or work centers.
33. How do you handle Material Requirements Planning (MRP) for Dependent Requirements in SAP PP?
You can handle MRP for Dependent Requirements by configuring the relevant settings in the MRP views of the material master and by defining the dependent requirements in routing or work centers.
34. Explain the concept of Make-to-Stock (MTS) planning strategy in SAP PP.
Make-to-Stock planning strategy is used when products are produced in anticipation of customer demand based on sales forecasts and kept in stock for immediate delivery.
35. How can you perform Demand Management in SAP PP?
You can perform Demand Management using the transaction code MD61 or by navigating to Logistics > Production > Production Planning > Demand Management.
36. What is the purpose of Work Scheduling View in the Material Master in SAP PP?
The Work Scheduling View in the Material Master is used to define production-related data such as work centers, control keys, and scheduling parameters.
37. How do you handle Batch Management in SAP PP?
Batch Management in SAP PP allows you to uniquely identify and track individual batches of materials to maintain quality control and traceability.
38. What is the use of the Scrap Percentage field in a BOM item in SAP PP?
The Scrap Percentage field in a BOM item defines the percentage of material that is expected to be lost during the production process.
39. How can you handle Production Versions in SAP PP?
You can handle Production Versions using the transaction code C223 or by navigating to Logistics > Production > Master Data > Bills of Material > Production Version.
40. Explain the concept of Exception Messages in SAP PP.
Exception Messages in SAP PP are used to alert planners about any deviations from the planned production schedule, such as capacity overload or material shortages.
41. What is the purpose of Routing in SAP PP?
Routing in SAP PP defines the sequence of operations required to produce a material and the work centers involved in each operation.
42. How do you handle Variant Configuration in SAP PP?
Variant Configuration in SAP PP allows you to manage different product configurations without creating separate material masters for each variation.
43. What is the use of the Serial Number Profile in SAP PP?
The Serial Number Profile in SAP PP defines the rules and characteristics for managing serial numbers assigned to materials.
44. How can you perform Material Requirements Planning (MRP) for External Requirements in SAP PP?
You can perform MRP for External Requirements by setting the appropriate procurement type and special procurement key in the material master.
45. Explain the concept of Rate Routing in SAP PP.
Rate Routing in SAP PP is used to calculate the standard production time for a material based on specific conditions such as batch size or production quantity.
46. How do you handle Alternative Units of Measure in SAP PP?
Alternative Units of Measure in SAP PP allow you to represent materials using different units for various purposes like purchasing, sales, and production.
47. What is the use of the Production Version field in a Material Master in SAP PP?
The Production Version field in a Material Master allows you to link the material to a specific production version, which contains the BOM and routing data for production.
48. How can you perform Scrap Calculation in SAP PP?
You can perform Scrap Calculation in SAP PP by defining the scrap percentage in the BOM item and setting up the appropriate settings for scrap handling.
49. What is the purpose of the Conversion of Planned Order to Production Order in SAP PP?
The Conversion of Planned Order to Production Order in SAP PP is used to convert planned orders generated by MRP into actual production orders.
50. How do you handle Make-to-Stock (MTS) scenarios in SAP PP?
Make-to-Stock scenarios in SAP PP involve producing goods based on a sales forecast and storing them in inventory for immediate delivery to customers.
51. What is the use of the Capacity Category field in a Work Center in SAP PP?
The Capacity Category field in a Work Center allows you to categorize work centers based on their capacity requirements, such as setup time, processing time, or teardown time.
52. How can you reschedule a Production Order in SAP PP?
You can reschedule a Production Order using the transaction code CO02 or by navigating to Logistics > Production > Production Control > Order > Reschedule.