Oracle Inventory
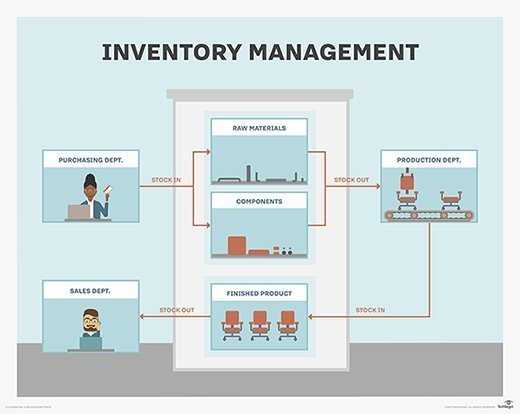
Oracle Inventory Course Overview
This course is designed to give delegates the knowledge to use Oracle 11i Inventory for day to day transaction processing as well as activities such as managing stock levels, together with periodic processes such as stock-taking, cycle counting and updating stock records to agree with physical stock counts. It provides a sound introduction to key elements of set up such as defining sub-inventories, locators and inventory items.
----------------------------------------------------------------------------------------------------------------------------------------
Who will the Course Benefit?
This Oracle Inventory course is designed for end users working either within a Finance department or in stores or equivalent areas.
--------------------------------------------------------------------------------------------------------------------------------
Course Objectives
By the end of this course delegates will be able to use Oracle Inventory to carry out daily tasks such as recording receipts and issues of stock , ensure the maintenance of appropriate stock levels, set up cycle counts and process periodic physical stocktakes and adjustments arising as a result of these. Delegates will be shown how to transfer bookkeeping entries from Inventory to General Ledger.
-----------------------------------------------------------------------------------------------------------------------------------
This is a Oracle Inventory course by Uplatz.
Oracle Inventory
Oracle Inventory Training Course
Course Introduction
- Administration and Course Materials
- Course Structure and Agenda
- Delegate and Trainer Introductions
Session 1: OVERVIEW OF ORACLE INVENTORY
- Inventory Structure
- Organizations
- Locations
- Sub-Inventories
- Locators
- Units of Measure
- Categories
- Item Defining Attributes
- Default Category Set
- Items
- Inventory Transactions
- Material Workbench
- Inventory Planning and Replenishment
- Accounting Close Cycle
- ABC Analysis
- Cycle Counting
- Physical Inventory
- Inter-Company Invoicing
Session 2: INVENTORY SET UP AND MAINTENANCE
- Control and Inventory Organization
- Review Organization Parameters
- Limit Organization Parameters
- Limit Organization Access
- Create Sub-Inventories
- Define Units of Measure
- Define Unit of Measure Classes
- Define Unit of Measure Conversion
- Create Picking Rules
- Create Cross Reference Types
Session 3: ITEM SET UP AND MAINTENANCE
- Define Items at Master Level
- Item Attributes
- Main Attribute Group
- Inventory Attribute Group
- Bill of Material Attribute Group
- Costing Attribute Group
- Purchasing Attribute Group
- Receiving Attribute Group
- Physical Attribute Group
- General Planning Attribute Group
- Lead Times Attribute Group
- Inactive Items
Session 4: INVENTORY TRANSACTIONS
- Inventory Transactions
- Account Alias Transactions
- Account Transactions
- Sub-Inventory Transfers
- Locating Inventory Transactions
- Checking Stock Availability
Session 5: RECEIPTS RETURNS AND CORRECTIONS
- Receipts Returns and Corrections
- Receipting Expected Stock Items
- Entering a Partial Receipt
- Receiving Unordered Goods
- Entering a Return
- Making Corrections to a Receipt
- Writing off Damaged Goods
Session 6: MIN - MAX PLANNING
- Organization Level Min - Max Planning
- Sub-Inventory Level Min - Max Planning
- Assigning Min - Max Levels at Sub-Inventory Level
- Running the Min - Max Planning Report
Oracle Inventory Training Course
Session 7: REORDER POINT PLANNING
- Reorder Point Planning
- Setting up Items for Reorder Point Planning
- Generating a Demand Forecast
- Creating a Forecast Set
- Assigning Safety Stock
- Manually Define Safety Stock
- Calculate Safety Stock Based on Existing Forecast
- Running the Reorder Print Point Planning Report
Session 8: REPLENISHMENT COUNTING
- Generating a Replenishment Count
- Purging Replenishment Counts
Session 9: PHYSICAL INVENTORY
- Defining a Physical Inventory
- Generating Physical Tags
- Printing the Tag Report
- Entering Counts
- Voiding Tags
- Approving Adjustments
- Posting Adjustments
- Purging Physical Inventory
Session 10: ABC CLASSIFICATION
- Reasons for ABC Classification
- ABC Analysis Setup
- Define an ABC Compile
Session 11: CYCLE COUNTING
- Set up a Cycle Count
- Define Cycle Count Classes
- Define Cycle Count Items
- Perform a Cycle Count
- View the Cycle Count Report
- Enter Cycle Counts
- Approve Cycle Count
Session 12: INVENTORY USER EXERCISES
Session 13: INVENTORY SUPERUSER EXERCISES
-----------------------------------------------------
-------------------------------------------------------------------------------------------------------------
Oracle Inventory Interview Questions
-------------------------------------------------------------------------------------------------------------1) Which Are Required Steps In Inventory Module Set Up?
· All the 6 key flex fields i.e. Items, Item Catalog, Account Alias, Sales Order, Locator and Item Category
· Organizations
· Change Organizations
· Intercompany Relations
· Unit of Measure Classes
· Sub inventories
· Item Attribute Controls, Categories
· Default Category set
· Item Statuses
· Cost types
· Profile Options
· Inventory Accounting Periods
2) What Is Item Master Organization?
An item master organization is a logical entity that you use to define items. After you define an item in the item master, you can assign it to any number of other organizations. You should also define one item master organization per implementation. When you define an item, Oracle automatically changes your current organization to the master organization.
3) What Is An Inventory Organization?
Inventory Organization is a facility where you store and transact items. It can be a manufacturing unit, warehouse, distribution centre, item master organization (logical entity), etc.
4) Can You Change Customer Item Name Or Item After You Save It?
Yes, you can change it if you have set the profile option INV: Updatable Customer Item to Yes and INV: Updatable item to Yes respectively.
5) What Is Item Status? Name The Related Table?
INVENTORY_ITEM_STATUS_CODE is the Colum in table MTL_ITEM_STATUS will tell you the different status for item while you defining the item in item master form (INVIDITM). You can have different status as shown in below, also u can define your own custom status in status code form in item setups (INV DOIS)like “easyapps”.
Active, Inactive, Engineer, Obsolete, Phase-Out, Prototype, OPM, Lease, Production, Concept, Design, DEM_Status, Pending.
6) Different Type Of Inventory Planning?
There are 4 inventory Planning methods as mentioned below:
o Min-max planning
o Re-order point planning
o Kanban planning
o Periodic Automatic Replenishment(PAR)
7) What Are The Flex Fields In Inventory?
- System Item
- Item Catalog
- Item Categories
- Stock Locator
- Account Aliases
8) What Is The Use Of Item Templates?
There are two types of templates: Predefined and Custom Template.
Predefined templates are planning item, purchased, outside processing item, lease item. So that once you assign any template, to new item then all default characters are assign to new item.
9) In Which Table Sub Inventory Related Information For Item Is Stored?
MTL_ITEM_SUB_INVENTORIES
10) What Are The Prerequisite Set Ups For Inter Organization Transaction?
Prerequisites:
Define an inventory item that is common to both organizations. Define at least two organizations, one of which is valid to receive material from the other. Set up inter–organization relationships and their corresponding accounts. Like Shipping Network. For direct transfers, if the item to transfer is under serial number control, the item must have the same unit of measure in each organization.
11) What is transaction action?
Transaction Action is predefined method of changing the quantity or location or cost of an item. It is used from Material Transaction form.
12) How many inventory transaction actions are available?
There are six predefined transaction actions available:
1. Subinventory Transfer
2. Issue from stores
3. Receipt into stores
4. Direct organization transfer
5. Inter-organization Transfer
13) What is Locator?
Locators are structures within Subinventories. Locators are the third level in the enterprise structuring schema of Oracle Inventory. Locators may be a row, bin, aisles in a warehouse. Stock locators are used to identify physical areas where you store inventory items. Item quantities can be tracked by locator. Items can also be restricted to specific locators.
14) Can you copy inventory org structure?
Yes. But can copy only organizations within the same operating unit.
15) What is Shipping Network?
An inter-organization shipping network describes the relationships and accounting information between a shipping organization and a destination organization. You must define a shipping network between two organizations before you can transfer material between organizations. When you setup a shipping network you must select a transfer type as Intransit or direct.
16) Explain Intransit and Direct Transfers?
In Intransit transfer, Oracle Inventory moves material to an intermediary state before it reaches the destination organization, and a receipt transaction is required in the destination organization once the material arrives in order to retrieve it.
In Direct transfer, Oracle Inventory moves the material directly to the destination organization.
17) Explain UOM and UOM class?
Unit of measure classes represent groups of units of measure with similar characteristics. For example, quantity is a unit of measure class and each, dozen, and gross are examples of units of measure within the class.
18) What Is The Difference Between Category And Category Set?
Categories and Category Sets can be used to group the items for various reports and programs.
A category is a logical classification of items that have similar characteristics. A category set is a distinct grouping scheme and consists of categories.
19) Which Is The Table For Storing Organization Information?
mtl_parameters
20) Where To Define Inter Organization Transaction Charges And What Are The Different Options?
Depending on the inter–organization transfer charge that applies between the organizations, a percentage of the transaction value or a discrete amount that Oracle Inventory uses to compute transfer charges.
21) What Is The Difference Between Organization_id And Org_id?
Org Id is a unique ID for the Operating Unit. Organization Id: The Organization Id is an ID for the Inventory Organization which is under an Operating Unit.
22) Can You Apply Material Overheads To Average Costing Organization?
No, you can not apply it to Average Costing Organization. However you can apply it to Standard Costing Organization.
23) Can You Do Inventory Transactions In Prior Periods?
Yes, you can do by setting the profile option INV: Transaction Date validation to Provide warning when date in past period or Allow date in any open period. It allows entry of a past date.
24) What Does Inventory Interface Do?
Inventory Interface Program populates the interface tables with transactions submitted through Confirm shipment forms. It updates order lines with shipped quantities and updates inventory.
25) What is subinventory?
Subinventories are unique physical or logical separations of material inventory, such as raw inventory, finished goods, or defective material. All material within an Inventory Structure organization is held in a subinventory therefore, you must define at least one subinventory.
26) What do you mean by “Required with defaults steps”?
Required with defaults steps means setup functionality comes with pre-seeded values in thedatabase. However, you can review the default values and decide whether to make changes those valuesto suit your business requirement.
27) Which are the “Required with defaults steps” in inventory setup?
There is no setup steps with “Required with defaults steps” in Inventory Module.
28) There is no Inventory Stock Locator in your inventory organization. Do you still require to configure the Stock Locator key flex field?
You don’t need to configure the Stock Locator flex field in a specific way, but you must still want to compile the Stock Locator flex field because all inventory transactions and on hand inquiries and reports require a frozen flex field definition.
29) What is the use of Picking Rule?
When you carry out the release sales order in order execution module from Order Management, it submits the request to oracle inventory module to pick the material from subinventory based on the item picking priority setup in the inventory picking rule and generate the pick list for sales order.
30) Can you apply material overhead in Average Costing Organization?
Yes, we can apply the material overhead in the Average Costing organization.
31) What is move order?
Move Orders is a request for the movement of material transfer within a single organization. They allow the movement of material within warehouse or facility for the purpose of replenishment, shortage, quality handling. Move orders can be generated either manually or automatically. At a high level, Move Order process has two basic steps:
a) Creation of the Move Order
b) Move Order transfer transaction
32) What is move order process?
o Move Order creation through various sources
o Move Order approval
o Move Order allocation
o Print Pick slip
o Move Order transfer/Transact MoveOrder
33) Which transactions are supported by Move Order?
Two transactions are supported by move order:
o Subinventory Transfer (Move Order Transfer)
o Account issue (Move Order Issue)
34) What is the function of profile option “INV: Fill & Kill Move Order”?
This profile option enables you to close a partially allocated and transacted replenishment moveorder line.
Available values are:
No- Does not allow cancelling of replenishment move order lines.
Yes- Allows cancelling of move order lines.
35) How do you inactivate a sub inventory and what are the measures you need to take?
Enter the date on which the sub inventory becomes inactive.
36) What are the sub inventory general ledger account fields?
o Material Account
o Outside Processing Account
o Material Overhead
o Overhead
o Resource
o Encumbrance
o Expense
37) How do you enable material shortage for WIP?
By enabling the CHECK SHORTAGE filed in shortage parameters.
38) What are the exclusions you have in material shortage check?
o Bulk Components
o Material Components
o Supplier Components
39) Who will receive a workflow notification about the material shortage?
o Component Buyer
o Component Planner
o Assembly Planner
o Job/Schedule Creator
40) What is Freight carrier?
A freight carrier is a commercial company used for internal transfers between organizations, as well as shipments to and from customers and suppliers. You must associate a general ledger account with each carrier to collect costs associated with using this carrier. You assign a carrier to each inter–organization transaction.
-------------------------------------------------------------------------------------------------------------