Job Meter = High
Lean Six Sigma Black Belt
30 Hours
Online Instructor-led Training
GBP 2000
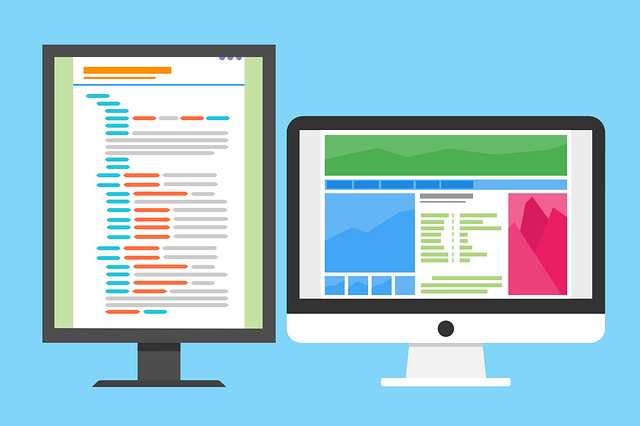
About this Course
The Lean Six Sigma Black Belt training and certification program will equip participants with the technical competencies, team leadership skills and change management skills to lead Lean Six Sigma projects using the Lean Principles and DMAIC (Define Measure Analyze Improve Control) methodology. The 10-day program will cover the most contemporary process improvement practices adopted by leading organizations and proponents of Lean Sigma Transformation in manufacturing, service, healthcare, financial, public sector as well as many other industries.
Business success in any organisation requires vision, products and services that add value, processes that are efficient, people who are competent and a culture that supports the behaviours of improvement and development. This course will address all these aspects with a significant focus on the cultural change and the role of the Lean Sigma Black Belt in the facilitation, change management and application of the tools to change a culture.
The role of the Lean Six Sigma Black Belt is a business improvement professional that is able to support the Lean and Six Sigma implementation journey in organizations, including assisting systems and tools implementation. They possess the ability to mentor multiple teams, monitor performance of all activities and engage leadership support to deliver genuine business improvements.
This programme will run over 5 months and will focus heavily on the application of the tools rather than their academic understanding.
The course covers the phases of a typical Lean Transformation utilising Lean Principles and Six Sigma: Define, Measure, Analyze, Improve and Control.
The methodology follows a structured sequence of problem solving techniques and cultural change management to arrive at a solution. Statistics aid in the decision-making process and help to validate the success of changes. Cultural facilitation embeds that change.
----------------------------------------------------------------------------------
Target Audience
This Lean Six Sigma Black Belt Training Course is recommended for all those in an organisation who will lead medium or large improvements and who will act as coaches or mentors to others involved in the improvement programme.
It is suitable for managers, internal consultants, change agents, project managers, team leaders, business improvement leaders or facilitators.
----------------------------------------------------------------------------------
Business success in any organisation requires vision, products and services that add value, processes that are efficient, people who are competent and a culture that supports the behaviours of improvement and development. This course will address all these aspects with a significant focus on the cultural change and the role of the Lean Sigma Black Belt in the facilitation, change management and application of the tools to change a culture.
The role of the Lean Six Sigma Black Belt is a business improvement professional that is able to support the Lean and Six Sigma implementation journey in organizations, including assisting systems and tools implementation. They possess the ability to mentor multiple teams, monitor performance of all activities and engage leadership support to deliver genuine business improvements.
This programme will run over 5 months and will focus heavily on the application of the tools rather than their academic understanding.
The course covers the phases of a typical Lean Transformation utilising Lean Principles and Six Sigma: Define, Measure, Analyze, Improve and Control.
The methodology follows a structured sequence of problem solving techniques and cultural change management to arrive at a solution. Statistics aid in the decision-making process and help to validate the success of changes. Cultural facilitation embeds that change.
----------------------------------------------------------------------------------
Target Audience
This Lean Six Sigma Black Belt Training Course is recommended for all those in an organisation who will lead medium or large improvements and who will act as coaches or mentors to others involved in the improvement programme.
It is suitable for managers, internal consultants, change agents, project managers, team leaders, business improvement leaders or facilitators.
----------------------------------------------------------------------------------
Lean Six Sigma Black Belt
Course Details & Curriculum
Enterprise-wide overview: history, foundations, integration of Lean and Six Sigma, business processes and systems and LSS applications
- Lean Transformation Roadmap
- Lean Assessment
- Leadership
- Responsibilities, roadblocks, change management, projects, Six Sigma roles and responsibilities
- Organizational Process Management and Measures
- Impact on stakeholders, Critical to x (CTx) requirements, Benchmarking, Business performance measures, Financial measures
- Project Selection
- NPV (Net Present Value) Analysis
- Value Stream Mapping
- Management of change
- Lean Six Sigma Teams
- Hoshin Kanri strategy deployment
Define Phase
- Voice of the customer
- Project charter
- Problem statement
- Project scope
- Goals and objectives
- Project performance measures
- Project tracking
- Project Stakeholder Analysis
- Measurable Customer Requirements
- Requirements Statements
- Process Mapping
- SIPOC
Measure Phase
- Process characteristics
- Input and output variables
- Process flow metrics
- Process analysis tools
- Data collection
- Types of data
- Measurement scales
- Sampling methods
- Collecting data
- Measurement systems
- Measurement methods
- Measurement systems analysis
- Basic statistics
- Basic terms
- Central limit theorem
- Descriptive statistics
- Graphical methods
- Valid statistical conclusions
- Probability
- Basic concepts and Distributions
- Process capability
- Process capability indices
- Process performance indices
- Short-term and long-term capability
- Process capability for non-normal data
- Process capability for attributes data
- Process capability studies and Process performance vs. specification
Analyse Phase
- Data Analysis Overview
- Pareto Analysis
- Gap analysis
- Root cause analysis
- Waste analysis
- Run Charts
- Histogram/Frequency Plot
- Cause and Effect Analysis
- Scatter Plot or Correlation Diagram
- Multi-Variant Analysis
- Correlation coefficient
- Regression
- Multivariate tools
- Multi-vari studies
- Attributes data analysis
- Inferential Statistics Primer
- Hypothesis testing
- Terminology
- Statistical vs. practical
- Significance
- Sample size
- Design of Experiments Overview
- Failure mode and effects analysis (FMEA)
Improve Phase
- Generating Creative Solutions- Brainstorming
- Analysing and Selecting Solutions- Decision Matrix
- 5S
- Autonomous Maintenance / TPM
- Quick Changeover / SMED
- Line Balancing/Operator Balance Charts
- Continuous Flow Layouts
- Kanban/Pull Systems
- Kaizen Events
- Pilot Testing
- Full-Scale Implementation
- Creativity and Innovation
- Eliminate, Combine, Redesign, Simplify (ECRS)
- Design of experiments (DOE)
- Waste elimination
- Cycle-time reduction
- Kaizen and Kaizen Blitz
- Theory of constraints (TOC)
- TRIZ
- Risk analysis and mitigation
Control Phase
- Control Plan Elements
- Statistical Process Control
- Statistical process control
- Objectives,
- Selection of variables
- Rational sub-grouping
- Control chart selection
- Control chart analysis
- Other control tools
- Total productive maintenance
- Visual factory
- Maintain controls
- Measurement system re-analysis
- Control plan
- Sustain improvements
- Lessons learned
- Training plan deployment
- Documentation
Design for Six Sigma (DFSS) Frameworks and Methodologies
- Common DFSS methodologies
- Customer Expectation
- House of Qualit
- Critical to Quality Deployment
- Critical Parameter Management
- Design for X (DFX)
- Robust design and process (Special design tools)