R12.2 Oracle Inventory Management Fundamentals
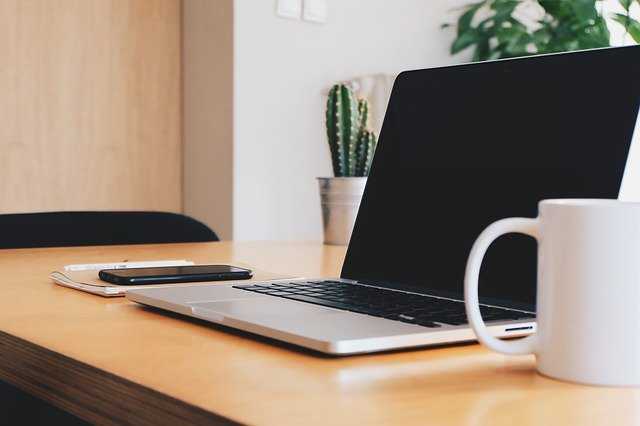
This R12.2 Oracle Inventory Management Fundamentals Ed 2 training is ideal for customers who have implemented Oracle E-Business Suite Release 12, 12.1 or R12.2. Enrolling in this course will also teach you where Oracle Inventory fits in the overall enterprise structure.
Course Objective
- Understand how to perform inventory transactions using a mobile device
- Understand how to define material statuses
- Understand how to define and maintain a cycle count
- Create an ABC ranking of items to be used in cycle counting
- Understand the overall inventory process in Oracle Inventory
- Understand how to view on-hand quantities
- Understand the structure of an inventory organization in Oracle Inventory
- Understand the planning and replenishment methods available in Oracle Inventory including min-max planning, reorder-point planning, replenishment counting, and Kanban replenishment
- Understand the role of an item-master organization
- Define items in Oracle Inventory
- Understand the concept of move orders
- Learn to implement locator, revision, serial, and lot control for items
- Perform inventory transactions such as subinventory transfer and interorganization transfer
- Set up shipping networks between inventory organizations and understand the significance of direct shipment and in transit shipment
- Understand how to create units of measure
- Understand how to create reservations
Target Audience
- End User
- Implementer
R12.2 Oracle Inventory Management Fundamentals
1. Overview of Oracle Inventory
· Receiving Inventory
· Transferring Inventory
· On-hand and Availability
· Issuing Inventory
· Inventory Accuracy
· Discussing Inventory Application Integration
2. Defining Inventory Organizations
· Overview of Inventory Structure
· Setting up the Inventory Organization Structure
· Defining Organization Parameters
· Defining Subinventories and Locators
3. Units of Measure
· Defining Units of Measure
4. Defining and Maintaining Items
· Defining Items Process
· Using Item Templates
· Assigning Items to Organizations
· Categories, Category Sets, and Catalogs
· Deleting Items
5. Lot and Serial Control
· Setting up Lot Control
· Maintaining Serial Information
· Maintaining Lot and Serial Genealogy
6. Transaction Setup
· Defining Transaction Types
· Defining Picking Rules
· Defining Account Aliases
· Opening and Closing Accounting Periods
· Setting up Move Orders
· Material Shortage Alerts and Notifications
7. Issuing and Transferring Material
· Managing Receipts
· Performing Transactions
· Performing Move Orders
· Performing Mobile Transactions
· Managing Shipments
8. On-hand and Availability
· Using the Material Workbench
· Creating Available to Promise Rules
· Managing Reservations
9. Material Status Control
· Material Status Setup
10. Inventory Replenishment
· Defining Replenishment
· Inventory Forecasting Methods
· Replenishment Counting
· Kanban
11. Inventory Accuracy Fundamentals
· Defining Counting
· ABC Analysis
· Cycle Counting
· Physical Inventory
12. Table Information
· Accessing the Electronic Technical Reference Manual (eTRM)
--------------------------------------------------